Introduction
The achievement of transforming good high-resistance concrete for compression and flexion is fundamental for the construction and stability of high-rise buildings and the design of coastal structures, pavements, tunnels, and large-dimension road bridges [1]. High-strength concrete is possible owing to the existence of new types of cement [2], superplasticizer additives [3], the use of fine materials such as silica fume (SF), ground quartz, fly ash, and the development of new types of structural fibers [4]. Much published research [5]-[11] has enhanced the performance of high-strength concrete by combining different types of materials, among which we can find the combination of SF with macro synthetic polypropylene fibers (PF) [12], [13], which achieves better ductile concrete behaviors and compressive strengths higher than 40 MPa. The inclusion of PF and SF in concrete offers a decrease in the utilization of continuous steel reinforcement bars to withstand traction and shear forces, occasionally providing a better degree of ductility (or energy absorption).
On the other hand, SF is an addition that augments the adhesion capacity in polypropylene fibers by a factor of 3 to 7, as well as the density of the interfacial area and, because of its pozzolanic activity and its filler effect, increases compressive strength (fc) by more than 100 %. The combined effect of PF microfibers and SF can increase fc, cracking at early ages, permeability, and reducing carbonation depths [9] . As for steel fibers, it has been found that the resistance to compression and flexural strength (ff) can increase by 85.5 and 64.9 %, respectively. When only silica fume and fibers are added, the increase is 113-117 % for compression and 85-136 % for flexural strength. Therefore, concretes produced with SF additions can be more resistant than those containing only SF [14]. Synthetic fiber increased the failure load of reinforced concrete beams and improved the serviceability by reducing the number and width of cracks [15].
Furthermore, the enhancements can be attributed to the internal confinement/cracks arresting mechanism and toughness [16]. For this reason, PF has become popular in constructing pavement, prefabricated elements, and projected concrete mine tunnels [17]. Cohesion in the microcracking concrete reinforced with PF area depends not only on the cohesion but also on the bridge tension of the fiber. Furthermore, the constitutive features of the concrete reinforced with PF are closely related to the nature of the concrete substrate [18].
However, despite such results, more studies are required to control and optimize the increased demand for water in concrete due to the use of silica fume [14] or fly ash [19], [20]. The PF alters the microstructure in terms of hydration, causing condensation on the concrete's microstructure [21]. Then, the use of SF must be taken into account because it accelerates the hydration process [22]. Ductility plays an essential role in the increased use of high-resistance concrete and its application areas, but SF also makes the concrete develop a more brittle structure due to the high resistance it provides.
Therefore, improving this characteristic is a significant problem for high-strength concrete when adding SF because concrete's ductility can be heightened through the use of SF in concrete; this depends on bonding with a synthetic fiber in a concrete matrix [14], [23], [24].
During the development of high-strength concrete, different PFS have been previously used. Nevertheless, microfibers or short fibers (<3 cm) are used in many studies, which, despite improving shrinkage, provide little flexural strength and influence coarse aggregates to manufacture high-strength concrete. As a result, the effect of the size of PF fibers is a factor that requires further study. Upon observing the impact and mechanical strength of concrete mixtures achieved with short fibers of polypropylene and silica fume, strength properties improve, particularly the concrete's impact resistance [7], which reaches an increase in resistance above 10 % adding fibers [6]. Beyond adding the superplasticizer, it has been found that better control of workability, drop, flow dispersion, and flow rate decreased (along with SF) when PF volume or length increased [25]. This aspect can be controlled when adding SF because the small size of microsilica particles improves the packing and contact surface [26].
Due to all of the above, this paper contributes to the search for an optimal high-performance concrete design using local sources. Herein, we provide an experimental and theoretical analysis. We examined the mechanical behavior and workability of the combined use of silica fume and long polypropylene macrofibers, along with local natural limestone and river gravel aggregates commonly used in the Colombia Caribbean cost used at two maximum nominal sizes.
Materials and methods
The fiber used in this study was monofilament polypropylene. It had a length of 55 mm, a flexural strength of 524 MPa, and a recommended use at 2 to 5 kg/m3. Coarse aggregates were one type of limestone (L), which originated from quarry exploitation, and another from siliceous river gravel (RG) fractured origin taken from old stormwater channels in the north of Bolívar, Colombia. Te characteristics of the aggregates are shown in Table 1 and Fig. 1.
Table 1 Characteristics of coarse aggregates
Parameter | Limestone | River gravel |
---|---|---|
Resistance to degradation: Los Angeles testing machine (%) | 28.24 | 12.48 |
Clay lumps (%) | 0.84 | 0.71 |
Absorption | 4.5 | 1.00 |
Uniformity coefficient | 1.58-2.17 | 1.8-2.13 |
Dry density | 2266.79 | 2462.66 |
Saturation density | 2368.80 | 2487.29 |
Apparent density | 2425.00 | 2525.00 |
Source: Own elaboration
The sand used was of the siliceous type, with a 2.51 g/cm3 dry density, fineness modulus of 3.28, absorption at 2.35 %, and an evaporable moisture content of 3.08 %. The cement was a high-strength type (or High Early Strength (HE) type as per ASTM C1157) [27], because, in Colombia, this cement is frequently recommended and used in all significant urban infrastructure works. The SF used had a SiO2 content greater than 95 %, a specific surface higher than 30 m2/g, and 3 to 5 % water content. The type F superplasticizer additive based on polycarboxylates and type D retardant setting additive had proportions below 1 %.
Method
The mixtures were made with a 7 % wc (water-cement) dosage of SF at a 0.47 wb ratio. For each aggregate, two gradations were used: 3/8 in and 3/4 in the fiber volume ranged from 0.0, 0.39, 0.63, and 0.79 in % Vf. The mixture design is shown in Table 2. Three cylindrical test tubes with a diameter of 100 mm and a height of 200 mm were used to evaluate the compressive strength under the ASTM C39M standard [28] for each fiber dosage and aggregate. Then, the procedures were repeated for mixtures with 7.0 % wc of SF. For ff, the same combinations were made in prismatic specimens with dimensions of 50x150x150 mm3 following the ASTM C78-2 standard methodology [29]. A total number of 48 compressions and 48 flexural strength tests were performed after seven days when the cure was at 100 % humidity. The sample preparation procedure and curing were made according to the ASTM C192/C192M-18 [30]. The mixtures were compacted in three layers with 25 strokes, taking the slump value as an indicator of workability following the ASTM C143 test methodology [31].
Table 2 Mix proportions
Mix | C | W | s | SF | CA | F | AT-F | AT-D |
---|---|---|---|---|---|---|---|---|
L | 448 | 210 | 660 | 0 | 930 | 0;0.39; 0.63; 0.79 | 0.8 | 0.4 |
RG | 448 | 210 | 660 | 0 | 930 | 0;0.39; 0.63; 0.79 | 0.8 | 0.4 |
L+SF | 448 | 226 | 660 | 31 | 930 | 0;0.39; 0.63; 0.79 | 0.6 | 0.4 |
RG+SF | 448 | 226 | 660 | 31 | 930 | 0;0.39; 0.63; 0.79 | 0.6 | 0.4 |
*c: cement (Kg/m3); w: water (Kg/m3), s: sand (Kg/m3); CA: coarse aggregate (Kg/m3), F: fibers (%Vf), AT-F: admixture type F (%wc), and AT-D: admixture type D (%wc)
Source: Own elaboration
Results and Discussion
Workability
The workability of the concrete was evaluated according to the settlement or slump value (Fig. 2).
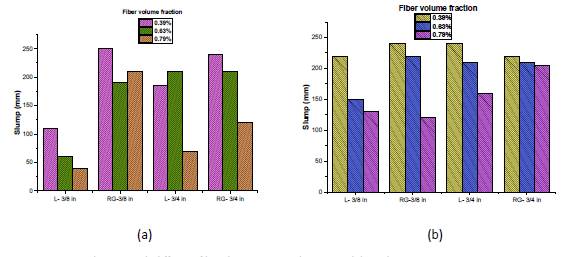
Source: Own elaboration (b)
Fig. 2 Mixture settlement with different fiber dosages: (a) without SF and (b) with SF.
As shown in Fig. 2, the mixture settlement was found to be within a range of 115 to 240 mm, thus indicating high workability, which is typical for the use of high-strength concrete. In the first mixture made with 9 mm L aggregate without SF, slumps below 100 mm were obtained. As such, the superplasticizer dosage increased, thus achieving a slump value greater than 100 mm in all mixtures. When the correction was applied on average, the slump value for the 3/8 in limestone aggregate (L) was 118 mm and, for the size of 19.0 mm, it was 179.1 mm. However, for the 3/8 in siliceous aggregate (RG), the average slump was 204.1 mm, and for the size of 3/4 in, it was 200.8 mm. In cases where the limestone-type aggregate was used, the workability of the concrete mixture was more excellent when river gravel was used (Fig. 2a). As the maximum nominal size of coarse L aggregates increased, the workability with polymeric fibers improved, reducing the superplasticizer. The effect of coarse aggregates on workability is shown in Fig. 2b, increasing a slump between 10 and 20 % when the maximum aggregate size increased from 3/8 to 3/4 during the maximum fiber dosage. In the L-type aggregate, a 0.2 % higher superplasticizer dosage was applied to the siliceous type to maintain high slump levels, allowing for a similar degree of workability in the two aggregates. The concrete mix had more excellent workability for the 3/8 in coarse siliceous aggregate (RG). This result is possible because such an aggregate is not fractured, providing it with lower surface roughness and improving the concrete's rheological characteristics [32].
Due to its hindrance for deformation and matrix movement, aggregate fibers decreased the workability of both concrete or mortar produced and increased the demand for water and cement paste [25]. The fibers' dispersion and surface coverage are significant for maintaining isotropic conditions and ensuring the highest anchorage of the fiber. Fig. 2 shows that, despite using a superplasticizer, the slump of the mixtures was not constant and the workability hinged on the mixture's fiber content. On the other hand, the workability decreased proportionally with the coarse aggregate size because, when the diameter was reduced, there was a greater surface area [33], [34].
Compressive Strength
The results from the tests showed a compressive strength between 36 and 71 MPa, indicating a high-strength concrete. The lowest compressive strength values were achieved when both 3/8 in and 19.0 mm river gravel aggregates were used (Fig. 3) without silica fume, which indicated that the material was conventional concrete with cement.
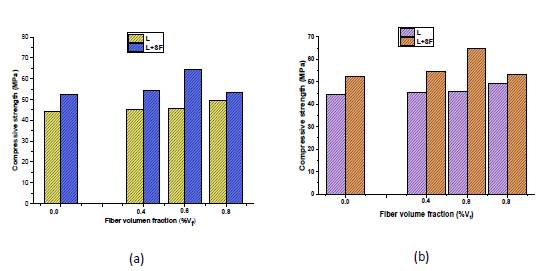
Source: Own elaboration
Fig. 3 Compressive strengths adding sf, different fiber dosages, and l aggregate sizes: (a) 3/8 in and (b) 3/4 in.
Fig. 3 shows the increase in fc when silica fume was added to the two aggregates. When a smaller maximum nominal size aggregate was used, there was a variation of the increase in f between 5-10 MPa. However, when a larger aggregate was used, the variation reached 20 MPa. The fiber used displayed an fc enhancement under a specific dosage and then declined. The increase in % Vf saturated the concrete matrix, generating agglomerates similar to the L+SF mixture with 0.79 %Vf.
Fig. 3b shows a dramatic drop in resistance for the said mixture. Such a drop was ascribed to the shortage of particles smaller than the maximum nominal size in the 3/4 type L aggregate (Fig. 2). Moreover, the 3/4 in RG type aggregate had more diverse particle sizes with no agglomerations appearing, so its resistance maintained a behavior in line with the other results. Similar behaviors were found in previous research. Hasan et al. [35] found a 4 to 7 % increase in compressive strength using 40 mm long PF without adding SF. Toutanji found an increase in fc with 0.3 % Vf and a decline when using 0.5 % Vf [11]. A greater fiber volume contributed a higher volume of incorporated air, and possibly, for high fiber percentages, the amount of extra air could lead to the formation of microcracks and a decrease in unit weight [36].
The enhanced compressive strength of the fiber-reinforced concrete (Fig. 4) was attributed to the ability of the ibers to restrict and delay the spreading of cracks and reduce the degree of stress concentration within the crack [37]. PP microfibers performed a bridging function in microcracks more efficiently, while PP macrofibers effectively participated in the conveyance of efforts when the maximum load point was reached. Moreover, close to the time of failure, polypropylene microfibers increased ductility and prevented the propagation of cracks [12]. Previous research showed that without the silica fume, fiber raised the fc to an optimal point [35], while the addition of silica fume facilitated the dispersion of fibers and provided additional resistance [7]. In previous studies, PF improved the shrinkage of the concrete allowing for three-dimensional reinforcement on a small scale [21]. In this manner, the packing effect that enhanced compressive strength prolonged the final state prior to a compression failure.
Flexural Strength
Fig. 5 shows an increase in ff induced by adding SF to the mixture. The values were significant for the limestone aggregate. The dosage of 0.39 % Vf did not significantly impact the resistance variation, whereas the 0.79 % Vf dosage exceeded the pattern sample. In the case of the RG aggregate, the fff diminished with dosages of 0.39 and 0.63 % Vf. PF improved the bridging behavior of the fibers within the cracks. SF as an addition in concrete resulted in a better transfer of tensile stress to the fiber [9].
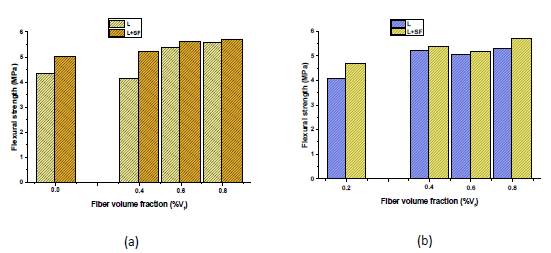
Source: Own elaboration
Fig. 5 Variation of flexural strength for limestone aggregate at seven days: (a) 3/8 in aggregate; (b). 3/4 in aggregate.
Fig. 6 shows that the increased behavior in ff was maintained by adding SF to the mixture. The values were more significant for the limestone aggregate, and all the dosages increased above the pattern sample. Furthermore, the ff values for the 3/4 in aggregates were generally lower than those for the 3/8 in samples, indicating that there may be a reduction in ff from the increase in aggregate size.
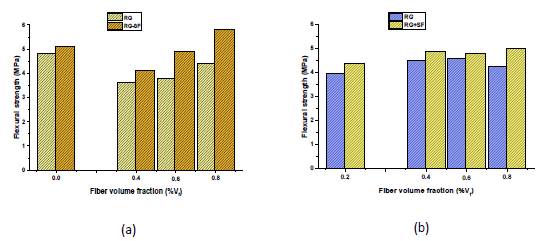
Source: Own elaboration (b)
Fig. 6 Flexural strength for river gravel aggregate: a. 3/8 in; b. 3/4 in.
Using siliceous aggregates, their high rigidity and smooth surface may lead to a weaker interfacial transition zone than crushed aggregates, affecting fracture mechanisms due to the "incompatibility" of river gravel deformation with the surrounding cement paste. Consequently, when integrated into a cement-based matrix, they can significantly affect the rheology and mechanical performance of selff-compacting concrete and fiber-reinforced concrete matrices. Such aggregates reduced deformation capacity in the matrix, which resulted in a more fragile mechanical response under compression stress and flexural strength [32]. In the case of microfibers, PF exerts a bridging effect on both sides of the concrete's fracture section, specifically when the matrix breaks. The PF that bonded the microcrack tensed when the crack developed and supported the tensile stress transferred from the fracture section.
At the same time, the concentration of stress in the area of the fracture became weak. This effect postponed the development of cracking damage and improved the ductility of the stress from silica fume. As a result, ff improved with PF [10]. As for macro-fibers, the effect was expected to work similarly but with a more incredible crack opening.
Fig. 7 shows the maximum increases for each aggregate type and size regarding the sample without silica fume and fibers. This figure shows that, on an individual basis, SF and PF raised the f and ff, but the combined use heightened the value even above the sum of the increases each addition brings. For both aggregates, there was a similar increase in fc by individually adding fiber and silica fumes when the coarse aggregate had a size of 3/8 in (Fig. 7a). When the size of the RG aggregate was raised, the increase in fc decreased.
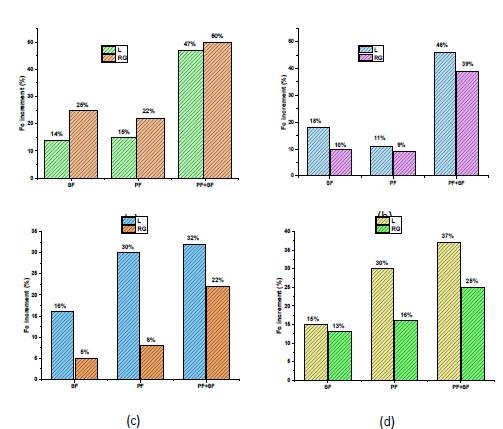
Source: Own elaboration
Fig. 7 Increase in resistance when adding SF, with an optimum dose of PF, and when combining the optimum PF and SF for each type of aggregate with maximum size (a and c) for 3/8 in (b and d) and 3/4 in.
In the case of the flexural strength, the combined use of both increased said value, but it did not rise above the sum of the increases that each addition brought. It should also be noted that fiber had a more significant effect on ff than silica fume. Similar to other research with polypropylene macrofibers, flexural strength and compression results showed that PF, when combined with SF, increases adhesion strength and extraction energy [22]. In a study with microscopic images, Park and Lee [13] observed that the synthetic macro fiber within silica fume influenced the number and extension of scratches and tears after a pull-out test, which was attributed to the friction during the extraction of the fiber. In addition, surface abrasion and the tearing of polypropylene macrofibers showed a trend similar to the bond strength and interface strength. Therefore, silica fume improved cement-based compounds' bond strength and interfaced strength by increasing friction during polypropylene macrofiber extraction. This quality allowed for the accomplishment of higher flexural strength loads.
In research projects where the concrete's fc and ff were tested, it was possible to observe an increase in such parameters [36]. However, to compare the maximum effect of each addition to the concrete's final performance, the individual and combined fibers and SF were first evaluated. Fig. 7 shows a maximum increase of f and ff through the RG + SF combination with a maximum size of 3/8 in and increase values of 50 and 22.0 %. However, as shown in Fig. 3, the maximum strength when adding fiber and silica fume was higher for aggregate L in all cases, which means that the addition of SF and PF improved the compatibility of the mixture much more than when RG-type aggregates were used.
Furthermore, the Type L aggregates achieved a higher performance with SF and fibers due to the very nature of the material, which was reflected in a better performance in the pattern samples without fiber when aggregate L was used. The effect of better anchorage in fiber with SF allowed it to better use its bridging capacity over a surface area where it made more excellent contact with the paste. On the other hand, the potential microcracks derived from the higher rigidity of the mixture due to the inclusion of silica fume were reduced when including PF; therefore, the mixture was more compact, and the joint use of the two materials generated greater mechanical capacity compared to what was provided individually.
Table 3 shows a comparison of the data obtained by Fallah and Nematzadeh [12], who took the gradation most similar to the material (i.e., limestone aggregate with ranges between 2.2 mm and 3/8 in (L 3/8 in)). Therefore, the resistances corresponding to this material were taken. The macrofibers used had a 39 mm and 0.78 mm diameter, which provided an aspect ratio of 50. For the present study, an aspect ratio of 91.7 was taken. In previous works, the straight ibers with the highest aspect ratio were more effective for improving the performance in flexural strength [38] and compression [14].
Table 3 Comparisons with the present work.
Fallah and Nematzadeh [12] | Present work | ||||||||
---|---|---|---|---|---|---|---|---|---|
Mix | fc MPa (*) | Cv** (%) | SPA (% wb) | Slump (mm) | Mix | fc MPa (*) | Cv** | SPA (% wb) | Slump (mm) |
Mix with fibers | |||||||||
Plain | 58.8 (-) | 3.2 | 0.6 | 170 | SF0-FP0-3/8 in | 48 (-) | 1.2 | 0.8 | 240 |
MP0.25 | 63.5 (8) | 3.6 | 0.6 | 170 | SF0-FP0.39-3/8in | 54.49 (12.7) | 6.1 | 0.8 | 240 |
MP0.5 | 61.3 (4.2) | 1.7 | 0.6 | 170 | SF0-FP0.63-3/8 in | 55.67 (15.1) | 3.0 | 0.8 | 240 |
MP0.75 | 60.7 (3.3) | 6.6 | 0.6 | 170 | SF0-FP0.79-3/8 in | 55.64 (15.1) | 5.7 | 0.8 | 210 |
MP1.25 | 56.4(-4.2) | 7.9 | 0.6 | 170 | |||||
Mix with sf | |||||||||
sf10 | 81.1 (37.9) | 0.8 | 0.65 | 110 | sf7-fp0-3/8 in | 55.26 (14.3) | 4.5 | 0.6 | 90 |
sf12 | 83.0 (41.1) | 5.4 | 0.65 | 70 | |||||
Mix with sf and fibers | |||||||||
mp1.25sf10 | 70.7 (20.1) | 3 | 0.93 | 110 | sf7- fp0.79-3/8 in | 71.1 (47.11) | 2.4 | 0.8 | 130 |
sf7- fp0.39-3/8 in | 60.01 (24.16) | 2.4 | 0.8 | 220 | |||||
sf7- fp0.63-3/8 in | 68.87 (42.49) | 4.9 | 0.8 | 150 |
*% improvement of strength. ** Coefficient of variation.
Source: Adapted from [12]
The additive percentage was higher in the mixture (0.8 % wc) than in the previous work (0.6), which provided the mixture with a better level of workability; however, in the ternary mixture (MP1.25SF10), the dosage increased (0.93 %) improving the consistency, whereas the incorporated air decreased, and the resistance was raised to a value similar to the present study (70.7-71.1 MPa). The previous investigation did not use the optimal fiber dosage (0.5 % Vf), but combined SF and PF were higher (1.25 % Vf). Such higher dosages initially reduced its resistance by 4.2 %; therefore, it was assumed that the authors could have obtained an fc increase percentage higher than what was registered (20.1 %), mainly when the optimal dosage of polypropylene macroibre was used. The proportion of the coarse aggregate concerning the cement used in this study (2) was 30 % greater than the one used previously (1.7), which might explain the lower fc values when SF was not incorporated. As we noted, the finer the granulometry, the greater the density and final strength of the concrete. However, there were higher percentages of fc when fibers were incorporated, which may be because their sand was a type of crushed gravel with minimum diameters of 0.15 mm. However, for this study, natural silica sand with minimum diameters of 0.055 mm was used. Although the percentage of sand was low, the fineness provided the fiber with higher surface friction. In contrast to the previous work, there was a contribution of results in terms of the flexural strength, so it was not possible to compare such results; however, it has been highlighted that the results for flexural strength remained at values above 4 MPa, which allowed for a good balance with high compressive strengths.
Conclusions
High-strength concretes (with resistance to 4071 MPa compression and 3.6 to 5.8 MPa flexion) made with natural river gravel or limestone type aggregates, with maximum nominal sizes of 3/8 in, were achieved when adding silica fume and polypropylene macrofibers of 55 mm. The concrete maintained its workability and showed good resistance to compression and flexural strength. The above represent useful features for constructing pavements, slabs, and beams for high-rise buildings. The workability of the mixture was directly decreased upon adding silica fume and decreased with the volume of fibers, a reduction in aggregate size, and irregular geometry. The river gravel type aggregate demanded less superplasticizer usage, while the coarse aggregate demanded more water consumption. However, the proper application of the plasticizer took the abovementioned variables into account, which enabled it to achieve a level of workability that ensured a slump above 100 mm.
Moreover, concrete with polymer fibers had a variable fc and ff behavior that depended on fiber dosage, aggregate type, and granulometry. The optimal dosage for each type of aggregate was 0.63 Vf for the RG type and 0.79 % Vf for the L type. Such an optimum dosage should be studied further to improve the performance and economy of the mixture. The incorporation of SF into the mixture improved resistance to compression, especially compared to flexural strength. However, both values were still higher than the individual effects of the additions when optimum polypropylene macrofiber dosages were used. The polypropylene macroiber and silica fume resulted in a better performance when using coarse aggregates at a maximum nominal size of 3/8 in than when using a maximum nominal size of 3/4 in. The limestone-type aggregates achieved higher resistance with SF and fibers due to the nature and shape of the material, which was reflected in higher fc and ff values. However, the addition of silica fume and fiber helped the RG-type aggregates to achieve even better resistance.