Introducción
Las actividades de mantenimiento prolongan la vida útil de los pavimentos. Aunque, en algunos casos estas son insostenibles porque implican costos que deben ser suministrados de manera constante durante el ciclo de vida del pavimento. Ocasionando que su intervención sea de manera reactiva o como un mantenimiento de emergencia [1], [2] con la finalidad de dar movilidad al usuario y evitar accidentes. Realizar actividades de conservación de manera inoportuna implica la aceleración del deterioro de la estructura del pavimento, la reducción del periodo de diseño, la afectación al usuario con relación a parámetros como: seguridad vial, comodidad, aumento de combustible, deterioro vehicular, mayores tiempos de desplazamiento y aumentos en el costo de operación [3], [4], [5], [6], y el retraso en las actividades de mantenimiento en las vías durante el ciclo de vida del pavimento. Lo que incrementa en dos a tres veces los costos en comparación con las intervenciones oportunas de conservación [7].
Los primeros daños que implican desprendimiento del material del pavimento flexible son los descascaramientos. Los cuales involucran pérdida de partículas de la carpeta asfáltica superficial, y pueden generar baches que presenten desintegración total de la carpeta asfáltica hasta dejar expuestos los materiales granulares [3]. Su aparición se presenta inicialmente con pequeñas fisuras que permiten el paso del agua, pero con el continúo paso vehicular se aumenta el tamaño convirtiéndose en grietas y desprendimiento de la mezcla asfáltica [4], [5], [8], [9], [10], [11]. Aquellas fallas son el resultado del daño por humedad, la calidad del asfalto, el espesor de la estructura del pavimento y la adhesión existente entre el asfalto y el agregado [9], [10]. En ese orden de ideas, el deterioro superficial presentado en el pavimento puede ser ocasionado por inapropiados procesos constructivos como: baja y/o inadecuada compactación, baja adhesión entre los materiales, desprendimiento, degradación, fisuración, envejecimiento del cemento asfáltico, exceso de cargas de tráfico para el que fue diseñado, deformación permanente o fatiga mecánica producida en el material asfáltico [3], [9], [12], [13].
Los descascaramientos o baches generan impactos sociales negativos. Por ejemplo, causan incrementos en los indicadores de accidentalidad, ocasionando un número importante de lesionados y muertes a causa del deterioro de la superficie de rodadura. Si bien los automóviles experimentan daños en la suspensión, sus choques son de menor magnitud comparados a los de los motociclistas. Ya que estos son los vehículos más vulnerables frente a la accidentalidad, porque las deficiencias en la infraestructura vial originan obstáculos fijos relacionados directamente con los casos de accidentalidad por motociclistas presentados en Bogotá D.C., Colombia [14]. Por lo anterior, se hace necesario investigar técnicas que permitan reparar daños emergentes de manera rápida y efectiva, antes de las intervenciones de mantenimiento y rehabilitación programadas.
Actualmente, las técnicas más usadas para la reparación de "huecos" o baches corresponde a los tratamientos semipermanentes, la inyección de mezclas emulsión-agregado y el lanzar-compactar mezclas asfálticas. En primer lugar, la técnica semipermanente consiste en ejecutar actividades de corte de la carpeta asfáltica alrededor del daño en forma de cuadro o rectángulo, seguidas por la aplicación de imprimante, la instalación de mezclas asfáltica en caliente y la compactación del parche ejecutado. Esta técnica, aunque busca aumentar la vida útil del pavimento, tiene tiempos prolongados de ejecución y cuenta con limitaciones respecto a la época de intervención, ya que no es posible utilizar esta técnica durante el periodo de lluvias. Además del suministro y retiro de materiales y maquinaria y el traslado de personal calificado [9], [15], [16], [17], [18], [19].
En segundo lugar, la inyección es una técnica que consiste en la instalación de una mezcla de emulsión asfáltica y agregado a presión y requiere de un equipo especializado. Su operación es realizada directamente en la zona de afectación del pavimento por medio de una tubería que repara el descascaramiento o bache [10], [15], [16], [20], [21], [22]. Por último, la técnica más sencilla y más antigua para la reparación de descascaramientos o baches es la de lanzar-compactar. El método radica en remover las suciedades y/o agua del bache, verter la mezcla asfáltica en capas de hasta 5 cm y compactar usando las llantas de un vehículo, compactador de rodillo, plato o apisonador (equipo o maquinaría al alcance) hasta de 40 a 60 mm por encima del nivel existente [10], [21]. Debido al corto tiempo de curado y la poca mano de obra, el equipo de construcción simple permite realizar la intervención sin generar mayores molestias al tráfico, como la implementación de Planes de Manejo de Tráfico (PMT) demasiados cortos. En comparación con la técnica semipermanente, este método tiende a ahorrar tiempo, generar buenos beneficios sociales y ser más económico para el mantenimiento de pavimentos [5], [9], [16], [17], [19].
Hoy por hoy, existen en el mercado mezclas asfálticas prefabricadas que tienen características similares a una mezcla asfáltica en caliente. Estas mezclas están compuestas de asfalto o emulsión asfáltica, agregado grueso, agregado fino y algún aditivo polimérico. Los aditivos presentes en la mezcla permiten que sea almacenada en bolsas o canecas de 25 kg, y que a la postre pueda ser instalada mediante la técnica de lanzar-compactar [18]. A pesar del crecimiento en el uso de estas mezclas, y con base en la literatura consultada, es escasa la evidencia de la evaluación del comportamiento mecánico y período desempeño de estos materiales; entendiéndose este como el tiempo de duración del material desde su instalación hasta la culminación de la vida útil. Por consiguiente, el objetivo de la presente investigación es evaluar el periodo de desempeño de mezclas prefabricadas almacenadas para actividades de parcheo.
Antecedentes
En 1986, estudios realizados en Estados Unidos evaluaron el tiempo y la rentabilidad de las diferentes técnicas de reparación para descascaramientos o baches. De esta investigación se pudo establecer que los materiales innovadores pueden llegar a tener mayor beneficio/costo, ya que implican menores tiempos de intervención y más durabilidad del material [21]. Uno de los estudios más extensos sobre el comportamiento de parches se llevó a cabo entre 1991 y 1996 bajo el Programa de Investigación Estratégica de Carreteras (SHRP).
Este proyecto concluyó, mediante pruebas de laboratorio y estudios de campo en diversos estados de Canadá y Estados Unidos, que la técnica de lanzar-compactar era, por un lado, eficiente en su instalación, y por el otro más rentable que la técnica semipermanente [15].
Por su parte, el Departamento de Transporte de Virginia (VDOT) evaluó mezclas mediante la técnica de lanzar-compactar y la semipermanente a través de ensayos de laboratorio para valorar su recubrimiento y adherencia de la emulsión asfáltica, desprendimiento, cohesión y trabajabilidad. Además, se llevó a cabo una evaluación mecánica sobre la estabilidad y flujo (empleando el aparato Marshall), resistencia a la tracción y de tracción indirecta (IDT) y carga acelerada de la rueda (mediante un simulador de carga móvil). De esta investigación se concluyó que los parches reparados mediante la técnica de lanzar-compactar se deterioraron más rápido a pesar de presentar un menor tiempo de intervención en comparación a las mezclas evaluadas mediante la técnica semipermanente [23], [24].
Por otra parte, investigaciones realizadas con el objetivo de determinar la efectividad de las técnicas para parcheo concluyeron que el tiempo estimado de duración para la reparación de los descascaramientos o baches con las técnicas de inyección y lanzar-compactar eran entre tres y veintiún meses. Mientras que para la técnica semipermanente era entre doce meses y dos años. Como conclusión, se estableció que estos tiempos estimados dependían de las condiciones en que se encontrara la estructura de soporte del material. Ya que el desempeño del material estaba directamente relacionado con la calidad de la estructura de soporte de la mezcla asfáltica [10].
Hubo otros estudios desarrollados en Canadá durante 2016 que evaluaron prácticas de reparación de parches en diferentes estaciones del año mediante la técnica de lanzar-compactar y la semipermanente. Allí se obtuvo que las mezclas analizadas por la técnica de lanzar-compactar presentaron periodos de duración de tres a nueve meses. Mientras que, para mezclas instaladas mediante la técnica semipermanente, se presentaron rangos entre uno a dos años [10], [25].
En Bogotá D.C., la Unidad de Mantenimiento Vial (UMV) para la reparación de baches utilizó la técnica de inyección con mezclas en frío y encontró que los corredores a implementar mediante esta técnica deben corresponder a bajos tráficos (N < 500.000 EE) y a la malla vial local e intermedia. Puesto que este no es un material apto para tráficos altos (N > 1'000.000 EE). Además, la estructura de pavimento a reparar no debe presentar daños importantes en las capas de la base y la subbase [26]. Con relación a las otras técnicas (lanzar-compactar y semipermanente) no se evidenciaron registros o investigaciones a nivel nacional donde se estudie el comportamiento mecánico, periodo de desempeño y/o evaluaciones a mezclas prefabricadas como mecanismo de reparación a daños (como descascaramientos o baches presentados en el pavimento asfáltico).
Metodología
Materiales y métodos
La campaña experimental consistió en evaluar tres mezclas prefabricadas almacenadas, comercializadas en la ciudad de Bogotá D.C., a través de la caracterización física de los materiales y su evaluación mecánica. Primero, se determinó el comportamiento físico y mecánico de estos materiales. A continuación, se prosiguió a determinar el número de ejes equivalentes de 13 y 8.2 toneladas mediante la metodología empírico-mecanicista (metodología racional) y la AASTHO-93, respectivamente, a través de la modelación de una estructura tipo. Por último, se determinó la estimación de la duración de las mezclas. Además, se realizó una comparación entre las mezclas prefabricadas almacenadas y el material de uso común para reparación de descascaramientos y baches pavimentos flexibles como la mezcla asfáltica en caliente.
Caracterización del material
Con el propósito de evaluar el tamaño de los agregados gruesos y finos, se efectuaron dos extracciones de asfalto, siguiendo el procedimiento de la norma INV E 732-13 [27]. Una vez retirado el asfalto del material granular, se ejecutó el análisis granulométrico a través de dos ensayos granulo-métricos desarrollados según la norma INV E 78213 [27], y se obtuvo la curva granulométrica de los tres materiales (figura 1) y el Tamaño Máximo Nominal (TMN) como se evidencia en la tabla 1.
En la tabla 1 se presentan los resultados de la caracterización física de mezclas prefabricadas almacenadas:
Tabla 1 Caracterización física de las mezclas prefabricadas almacenadas.
Ensayo | Norma | Unidades | Tipo I | Tipo II | Tipo III | Requisitos mínimos E. IDU 580-11 |
---|---|---|---|---|---|---|
% Asfalto + aditivo + polímero + emulsión* | % | 6.25 | 8.94 | 8.65 | No se especifica | |
Tamaño Máximo Nominal (TMN) | Normal (mm) Alternativa | 9.5 (Tamiz 3/8") | 12.5 (Tamiz 1/2") | 12.5 (Tamiz 1/2") | No se especifica | |
Gravedad Específica Bulk | INV E 733-13 INV E 734-13 | g/cm3 | 1.86** | 2.34 | 2.25 | No se especifica |
Gravedad específica máxima | INV E 735-13 | g/cm3 | 2.28 | 2.48 | 2.38 | No se especifica |
Porcentaje de vacíos | INV E 736-13 | % | 18.0 | 4.5 | 5.0 | 4-7 |
Estabilidad | INV E 748-13 | kg-f | 170 | 1545 | 1795 | Min. 750 |
Flujo | INV E 748-13 | mm | 0.339 | 3.20 | 3.27 | 2-4 |
Relación Estabilidad/Flujo | INV E 748-13 | - | 501.47 | 482.81 | 548.93 | 200-400 |
Fuente: elaboración propia.
Nota:
*El contenido del asfalto, aditivo, polímero y emulsión se calculó por diferencia a partir de la masa del agregado extraído mediante proceso INV E 732-13.
** Se determinó inicialmente la gravedad específica bulk mediante la norma INV E 733-13, y se registró un porcentaje de agua absorbida superior al 2%, por lo que se continuó con el procedimiento de la norma INV E 734-13 que consiste en el recubrimiento de las probetas con parafina.
Al compararse con la especificación técnica IDU 580-11 [28], los resultados de las características físicas de las tres mezclas muestran que la mezcla tipo I no cumple con los criterios establecidos respecto a porcentaje de vacíos, estabilidad, flujo y la relación estabilidad-flujo. Además, de acuerdo con el porcentaje de vacíos obtenido, se establece que la mezcla tipo I (18%) es una mezcla abierta, y que tanto la mezcla tipo II (4.5%) como la mezcla tipo III (5%) son densas [3], [29]. Con respecto a la relación estabilidad-flujo, estos requisitos se cumplen parcialmente, ya que se evidencian valores más altos de los rangos establecidos en la especificación. Este parámetro incide en el comportamiento de las mezclas en ensayos mecánicos porque una mayor estabilidad mejora el comportamiento al ahuellamiento y reduce el comportamiento a la fatiga. En el caso de estas mezclas prefabricadas, este comportamiento puede asociarse al tipo de aditivos del asfalto que contiene cada mezcla.
Por otra parte, en la bibliografía existente y según valores presentados para la relación estabilidad-flujo, los materiales evaluados pueden soportar adecuadamente tráficos de T2 y T3 [12]. Sin embargo, se reportan valores mayores a los sugeridos. Lo que significa que el material no es apto para su utilización y, por el contrario, refleja un mejor comportamiento a la resistencia y a la deformación. Aunque esto podría implicar comportamientos frágiles a temperaturas bajas.
1.3. Diseño Experimental
Las mezclas prefabricadas almacenadas se evaluaron con el material adquirido de los fabricantes. Se aclara que el material no fue transformado o modificado de su estado de recepción. Las probetas se construyeron en el laboratorio de la Pontificia Universidad Javeriana, considerando los criterios de normas nacionales e internacionales y tomando en cuenta las condiciones del ensayo como se evidencia en la tabla 2.
Tabla 2 Especificaciones generales de los ensayos mecánicos.
Tipo de probeta | Dimensiones | Cantidad | Ensayo | Norma |
---|---|---|---|---|
Cilíndrica | Diámetro (Ø=10.2 cm), altura (h=5.0 cm). | 8 | Cántabro | INV E-760-13 [25] |
Diámetro (Ø=10.2 cm), altura (h=6.35 cm). | 24 7 | TSR Módulo resiliente | INV 725-13[25] une - en 12697 - 26: 2012 anexo C [30] | |
Prismática | Largo (l=30 cm), Ancho (a=5 cm) y Altura (h=30cm) | 6 | Ahuellamiento | pren 12697-22 parte 22 [29] y la INV E 756-13 [25] |
Trapezoidal | Base mayor (Bm= 5.6 cm), base menor (bm=2.5 cm), altura (h=30cm) | 36 | Fatiga trapezoidal | prEN 12697-24 parte 24 [31] |
Fuente: elaboración propia.
Para la evaluación de susceptibilidad al agua utilizando la prueba de tracción indirecta (TSR) el ensayo Cántabro y el módulo resiliente se fabricaron probetas cilíndricas, según su granulometría y el porcentaje de vacíos. Considerando que la mezcla tipo I tuvo un porcentaje de vacíos del 18%, no se realizó el ensayo de TSR. No obstante, sobre esta mezcla se realizó el ensayo Cántabro para determinar la pérdida por desgaste evidenciado en el material, ya que presenta una granulometría abierta [31]. En el caso de las mezclas tipo II y III para el ensayo TSR se fabricaron probetas en el compactador giratorio Superpave hasta alcanzar el porcentaje de vacíos entre el 6% y el 8% requerido.
El ensayo de módulo resiliente se ejecutó con el equipo de Nottingham Asphalt Tester (NAT) a temperaturas de 10° C y 15° C, similares a aquellas alcanzadas en la ciudad de Bogotá D.C. bajo frecuencias de 2.5, 5 y 10 Hz [32]. Para la mezcla tipo I, se tuvieron tres ensayos fallidos en la mezcla tipo I, debido a que las probetas se disgregaron antes de aplicar la carga al material como se refleja en la figura 2.
Por otra parte, para el ensayo de deformación permanente (ahuellamiento), las probetas prismáticas se compactaron en la máquina universal de carga a 600 kPa. El ensayo se realizó a 42 revoluciones por minuto (r.p.m.), simulando el paso de una llanta con 0.662 MPa de presión y peso por eje de 13 toneladas, a una temperatura de 60°C [30], [33], siguiendo la norma NLT-173/84. El ensayo de fatiga trapezoidal se ejecutó en los bancos de la Pontificia Universidad Javeriana. Como dato de entrada se modeló el Tamaño Máximo Nominal (< 14 mm) especificado en la tabla 1. Este se desarrolló bajo el parámetro de deformación controlada a tres niveles de amplitud: 90x10-6, 150x10-6 y 220x10-6, con el objetivo de obtener las leyes de fatiga. Todos los ensayos se realizaron a una frecuencia de 10 Hz y a una temperatura de 15 °C [34], [35].
El equipo utiliza el mecanismo de flexión por tracción, en donde las cuatro (4) briquetas se someten a la aplicación de una deformación sinusoidal en la parte superior de la probeta trapezoidal empotrada en su base [36], [37]. El ensayo de fatiga permite determinar el número de ciclos que soporta la estructura de pavimento antes de generar la falla [36]. El criterio de falla para la evaluación del ensayo de fatiga ocurre cuando el material llega al 50% de la rigidez inicial [38]. Para el caso de la fatiga trapezoidal, se evidencia una fisuración en la probeta al tercio central de la misma [37].
2 Resultados y discusión
En la figura 3 se muestran las probetas antes y después del ensayo Cántabro, donde se observa que las probetas después de las 300 revoluciones en la máquina presentaron un desprendimiento del material en sus aristas curvas. Por otro lado, en la tabla 3 se presentan los resultados para el ensayo Cántabro en la mezcla prefabricada almacenada tipo I.
Tabla 3 Valores obtenidos en el ensayo Cántabro-pérdida de desgaste en la mezcla tipo I.
No. De Probeta | Peso inicial (g) | Peso final (g) | % de pérdida de desgaste |
---|---|---|---|
1 | 868.25 | 0 | 100.00 |
2 | 890.61 | 406.16 | 54.40 |
3 | 893.66 | 387.06 | 56.69 |
4 | 896.91 | 416.16 | 53.60 |
Promedio | 66.17% |
Fuente: elaboración propia.
El valor promedio de la pérdida de desgaste de la mezcla tipo I es de 66.17% (tabla 3). Según lo consultado en el Manual de Carreteras de España, para mezclas asfálticas convencionales para tráficos T0 a T2 (tráficos bajos) debe ser < 25% de pérdida, y para tráficos altos (T3 a T5) debe ser < 20% de pérdida. Por lo anterior, se evidencia que el material presenta un porcentaje de disgregación por encima de los parámetros permitidos [39] en comparación con las demás mezclas prefabricadas almacenadas. Adicionalmente, y conforme a evaluaciones realizadas con anterioridad a materiales de parcheo [5], se puede concluir que el resultado en el ensayo Cántabro está directamente relacionado con el bajo contenido de asfalto del material para la mezcla l.
Respecto al ensayo de deformación permanente para mezcla tipo I, esta no soportó el ensayo de ahuellamiento debido a que se presentó un desplazamiento en el material del 42.22 mm a los tres minutos con solo 126 ciclos de carga (figura 4). Conforme con lo estipulado en la norma INV E 756- 13, una vez alcanzado los 15 mm se detuvo el proceso. Esta condición puede explicarse porque el material mostró un alto contenido de vacíos (18.07%), y un contenido de ligante de medio a alto (6.25%). Lo que implicó una significativa deformación permanente de la mezcla tipo I.
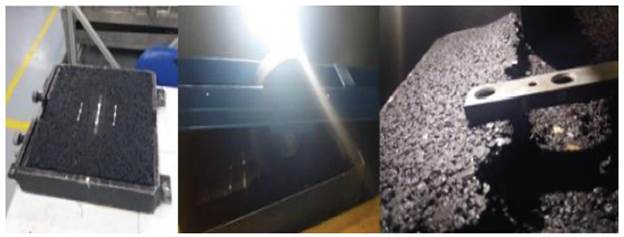
Fuente: elaboración propia.
Figura 4 Probeta antes, durante y después del ensayo de ahuellamiento de la mezcla tipo I.
Por su parte, el comportamiento ante el ensayo de ahuellamiento de las mezclas tipo II y III se muestra en la figura 5.
Al evaluar el comportamiento de la deformación permanente de las mezclas tipo II y III, se comprobó que soportaron cerca de 1500 y 1200 ciclos, respectivamente, para una deformación plástica de 14 mm. La comparación de estos resultados frente a lo reportado por Dong et al. [15] sobre mezclas utilizadas para la reparación de parches en pavimento flexible (14 mm a 200 ciclos), indica que estas mezclas prefabricadas almacenadas tienen una resistencia superior a la deformación en comparación con mezclas en frío. Asimismo, esto demuestra que las pendientes de las curvas muestran una transición gradual ante la deformación permanente. Los valores de módulo resiliente para las mezclas prefabricadas almacenadas tipo II y III se muestran en la tabla 4 a una temperatura de 10° C y 15° C, respectivamente.
Tabla 4 Valores para módulos resilientes de las mezclas prefabricadas almacenadas tipo II y III a una temperatura de 10° C y 15° C.
Fuente: elaboración propia.
De acuerdo con los resultados mostrados en la tabla 4, se evidencia que la mezcla tipo III frente a la mezcla tipo II tiene un mayor módulo resiliente. Los resultados reportados para una mezcla asfáltica en caliente indican valores de módulos resilientes para una temperatura de 10°C y 10 Hz entre 7000 MPa y 13000 MPa [40], [41] y para una temperatura de 15°C y 10 Hz entre 6200 MPa y 7400 MPa [33], [37]. En ese sentido, la mezcla tipo II se encuentra un 32% por debajo del límite inferior de aquellas mezclas en caliente evaluadas a 10 °C y significativamente por debajo (64%) del límite inferior de las mezclas en caliente a 15 °C. En contraste, en la mezcla tipo III, los módulos alcanzados se encuentran levemente por encima del límite inferior (8%). Lo que indica que cumplen para 10 °C, y levemente por debajo del límite inferior (23%) para 15 °C. Estos resultados señalan que, frente a los módulos resilientes, estas mezclas pueden ser efectivas para reparaciones de emergencia.
En cuanto al ensayo de fatiga, para la mezcla prefabricada almacenada tipo I de granulometría abierta, el factor de fatiga no se manifestó. Suceso que se había presentado antes en mezclas asfálticas en caliente con granulometría abierta, conforme a lo reportado por Reyes et al. [37]. Este comportamiento esperado se debe al alto contenido de vacíos en la mezcla, y a que en el momento de aplicar la deformación a la probeta se efectúa una recuperación del material, provocando mayores deformaciones y evitando la falla y/o ruptura de la probeta. Lo que ocasiona que la mezcla sea más resistente a la falla [37], [42]. En conclusión, la mezcla tipo I es incomparable con respecto a la mezcla tipo II y III debido a que la resistencia de la fatiga depende del parámetro del porcentaje de vacíos. A medida que aumenta, la resistencia a la fatiga del pavimento disminuye [3]. Razón por la cual las mezclas con gradación densa presentan una mayor resistencia con respecto a las gradaciones abiertas en la evaluación del comportamiento de la fatiga [43]. Los resultados para las mezclas prefabricadas almacenadas tipo II y III, se registran en la tabla 5 y en la figura 6.
Tabla 5 Valores de la ley de fatiga para las mezclas de tipo I, II y III.
Mezcla Prefabricada Almacenada | Deformación x 10 -6 m | No. de ciclos de falla en millones | Tipo de falla | ε6x10-6 | b |
---|---|---|---|---|---|
Tipo II |
|
|
|
96.53 | -0.224 |
Tipo II |
|
|
|
68.50 | -0.406 |
Fuente: elaboración propia.
La mezcla tipo II presentó un mayor número de ciclos de carga (entre >53.4 y 1.1) en comparación con la mezcla tipo III (entre 5.81 y 0.6). Por lo que se puede inferir que la mezcla tipo II tiene un mejor comportamiento a la fatiga que la mezcla tipo III. Esto se debe a que el material tiene mayor contenido de finos y de asfalto, lo que proporciona a la mezcla una mayor trabajabilidad y resistencia a la ruptura de la probeta. Adicionalmente, la mezcla tipo III tiene una mayor pendiente, lo que significa que el material posee una mayor rigidez que la mezcla tipo II. De esta manera, se confirma que el comportamiento de la fatiga en las mezclas asfálticas está directamente relacionado con los parámetros de estabilidad-flujo, porcentaje de vacíos, tipo y cantidad del ligante asfáltico [2], [9], [38], [44], [45].
Para mezclas asfálticas en caliente se presentan pendientes de la curva de fatiga entre -0.23 y -0.44 [33], [35]. Mientras que para materiales con adiciones de polímeros se presentan entre -0.26 y -0.21 [33], respecto al comportamiento del ensayo en mezclas prefabricadas almacenadas. Dentro de la búsqueda de literatura nacional e internacional no se evidenciaron ensayos de fatiga trapezoidal para este tipo de materiales. En los resultados obtenidos de la mezcla tipo III (-0.406) se evidencia que esta se encuentra en el límite del rango establecido para una mezcla en caliente. Por su parte, los resultados de la mezcla tipo II (-0.224) muestran que esta se halla en el rango presentado para una mezcla con adición de polímeros.
Por último, en la tabla 6 se exponen los resultados de daño por humedad para las mezclas tipo II y III.
Tabla 6 Valores de daño por humedad en las mezclas tipo II y III.
Fuente: elaboración propia.
Conforme a los resultados de la tabla 6, se evidencia que los valores son similares entre los dos materiales prefabricados evaluados. Con respecto a los datos obtenidos en las mezclas asfálticas en caliente, convencionales y de alto módulo, los rangos establecidos fueron entre 76% y 94% [35], [46], [47], [48]. En contraste, para mezclas utilizadas en actividades de parcheo de materiales fríos en bases acuosas de mezclas de asfalto emulsionado con epoxi, los rangos reportados fueron de 75.2 % y 76.1 % [47]. Lo que implica que las mezclas tipo II y tipo III se encuentran dentro de los rangos constituidos. Aunque en algunos casos reportan valores mayores que aquellos que se reportan en la literatura. Se puede afirmar que la resistencia TSR en presencia de agua de estos materiales prefabricados es favorable y cumple con los requisitos del artículo 450-13 INVIAS, ya que el promedio supera el 80% requerido [27], [35]. Asimismo, y conforme a lo propuesto por el Departamento de Transporte de Carolina del Norte (NCDOT), el criterio mínimo de TSR es del 85% [46]. Por lo tanto, las mezclas prefabricadas pueden cumplir con otras normativas.
Evaluación del periodo de desempeño de las mezclas prefabricadas almacenadas
El cálculo del periodo de desempeño se desarrolló para las mezclas prefabricadas almacenadas tipo II y tipo III. Ya que para las modelaciones son requeridos los resultados de los ensayos de resistencia a la fatiga del material y módulo resiliente, fenómeno que no se manifestó en la mezcla tipo I. Para realizar la comparación con la mezcla asfáltica en caliente convencional, se tomaron valores de referencia [33], [37], [46] en cuanto a parámetros como fatiga y módulos resilientes.
Para determinar el periodo de desempeño en las mezclas asfálticas, se realizaron los cálculos para la metodología empírico-mecanicista de la guía francesa (metodología racional) y AASTHO-93. Para las modelaciones se hicieron las estimaciones de los parámetros N (Tráfico acumulado en ejes equivalentes de 13 toneladas) y W18 (Número de ejes equivalentes de 8.2 ton) de la ecuación 1 y 3 respectivamente. Para determinar el periodo de desempeño en meses se utilizaron las ecuaciones 2 y 3. Además, se estableció una estructura de tipo de pavimento, como se muestra en la figura 7.
Metodología empírico-mecanicista:
Los parámetros estimados para la ecuación 1 fueron los factores de corrección. kc= evalúa el comportamiento del material en laboratorio (1.1), ks= tiene en cuenta la resistencia a fatiga de la capa que la soporte (1/1.1), kt= es un coeficiente por corrección de temperatura (1) y k= es el coeficiente que ajusta el valor de la deformación (1) [50], [53]. (deformación a tracción máxima) es obtenida para cada material mediante la relación modular entre la capa asfáltica y la subrasante. Teniendo en cuenta que la evaluación mecánica se desarrolló para las mezclas prefabricadas únicamente, en cuanto a los parámetros de la mezcla asfáltica en caliente para la resistencia a la fatiga, se establecieron los parámetros de y b= -0.442 [33], [37], [50].
Para la ecuación 2, se supusieron los siguientes valores: MJA tránsito pesado promedio anual diario de 1500 [39], para el CAM un valor de 0.4, ya que este depende de la clasificación del tráfico obtenida (T1) [35], y un i que corresponde a una tasa de crecimiento anual del 2.5% [50].
Metodología AASTHO-93:
Los parámetros teóricos estimados para la ecuación 3 fueron Zr = desviación estándar normal (Valor asumido -1.645); So = error estándar combinado de la predicción del tráfico y de la predicción del comportamiento estructural (valor asumido 0.45); SN = número estructural (se estimaron los coeficientes estructurales a1, a 2 , a 3 para cada una de las capas que conforman la estructura de pavimento en función del módulo resiliente indicado en la figura 7 [8] para los coeficientes de drenaje mi = 1, mi= 0.9 y ms = 0.9); APSI = diferencia entre índice de servicio inicial y final (valor asumido: 1.7 [12]) y Mr = módulo resiliente (conversión para el cálculo en ), según lo expuesto en la figura 7.
Para la ecuación 4, los valores presentados corresponden a una vía intermedia característica de la ciudad de Bogotá, un TPD (Tránsito Promedio Diario) de 1500 [39], para el F.C. factor de camión de 4.72 [8], y un i que corresponde a una tasa de crecimiento anual del 2.5% [50].
Tabla 7 Valores mediante las metodologías empírico-mecanicista y AASTHQ-93 para actividades de parcheo.
NE*: número de ejes equivalentes - P**: periodo de desempeño (meses).
Fuente: elaboración propia.
Según la bibliografía existente [25], [54], se estimaron periodos mayores a tres meses y menores a veintiuno meses para mezclas en frío (técnica inyección y lanzar-compactar) como el tiempo de desempeño en reparación de descascaramientos y baches. Para mezclas en caliente se establecieron rangos entre un año y dos años con técnica semipermanente. Comparando estos resultados con los reportados en la tabla 7, las mezclas prefabricadas almacenadas y la evaluada para la mezcla en caliente se encuentran dentro de los rangos de las consultas de referencia. Asimismo, presentaron la misma tendencia: el mayor tiempo estimado de desempeño es para las mezclas en caliente en comparación con las mezclas prefabricadas almacenadas.
Por otra parte, al desarrollar las modelaciones para el periodo de desempeño mediante la metodología empírico-mecanicista y AASTHO-93, se evidenciaron diferencias entre los periodos calculados. En primera medida, las mezclas en caliente y la mezcla tipo III presentaron un aumento en el tiempo estimado entre una metodología y la otra. En cambio, la mezcla tipo II presentó una disminución en el periodo de desempeño. Estas variaciones se deben a que como insumo para el análisis de la metodología empírico-mecanicista es necesario dos ensayos de laboratorio evaluados en las mezclas prefabricadas (como el de fatiga y módulo resiliente). Debido a que dentro de la modelación se tiene en cuenta el estado de esfuerzo y deformación que experimentan las capas que conforman la estructura del pavimento, lo que influye en el comportamiento del mismo [49].
Por su parte, la metodología AASTHO-93 dentro de su análisis tiene como insumo principal el ensayo de módulo resiliente. Lo que involucra la rigidez del material. De acuerdo con los resultados de los ensayos de laboratorio evaluados anteriormente, las características propias de cada material de análisis influyen en el resultado presentado para el periodo de desempeño de los mismos.
Conclusiones
Para la mezcla tipo I, los resultados se presentaron por fuera de los rangos contemplados en la especificación técnica IDU 580-11 (caracterización física), y con relación a la literatura nacional e internacional para la caracterización mecánica, pues no fue posible la ejecución, ni el análisis de los ensayos: módulo resiliente, ahuellamiento, TSR y fatiga. Con relación al ensayo Cántabro, se presentó un porcentaje de pérdida por fuera de los rangos requeridos en las normas internacionales. De esta manera y según la experimentación realizada, la mezcla tipo I no se recomienda para ser implementada en actividades de parcheo en mezcla asfáltica, o como mecanismo de reparación para daños como descascaramientos y baches. Pues evidenció un comportamiento desfavorable durante y después de la ejecución de los ensayos en laboratorio, dado que el material se desintegraba.
Con respecto a la caracterización física y mecánica, el comportamiento de las mezclas tipo II y III, en comparación con la especificación IDU ET 580-11, estuvo dentro de los parámetros mínimos requeridos. Con relación a la literatura consultada, estas mezclas instaladas mediante la técnica de lanzar-compactar presentaron valores menores a los establecidos para mezclas asfálticas en calientes, implementadas a través de la técnica semipermanente. No obstante, aunque fueron menores los valores, las mezclas prefabricadas evidencian una solución adecuada para realizar actividades de parcheo en un menor tiempo de intervención.
La caracterización física y mecánica obtenida en las mezclas prefabricadas almacenadas tipo II y tipo III corresponde con el número de ejes equivalentes resultante de la evaluación para 8.2 y 13 toneladas. La clasificación del tráfico estimado fue de T1 y T2. Por consiguiente, se puede afirmar que estos materiales son favorables para realizar intervenciones que soporten tránsitos bajos y que se ejecuten para efectuar actividades de emergencia en la malla vial de Bogotá. Lo anterior con el propósito de dar movilidad y seguridad vial a los usuarios a corto plazo, prolongando la vida útil del segmento vial hasta que se realicen actividades a largo plazo, con intervenciones como mantenimiento periódico, rehabilitación o reconstrucción.
Recomendaciones
Dados los resultados obtenidos, se recomienda para futuros proyectos de investigación realizar una evaluación en campo donde se sometan estos materiales a cargas y condiciones ambientales reales y se efectúe un seguimiento a lo largo de la vida útil del material. Esta estimación suministraría información que serviría como mecanismo de comparación entre tiempos estimados mediante el presente artículo y valores in situ.