1. Introducción
Las pequeñas y medianas empresas (PYMES) se han convertido en una de las principales actividades de negocio del desarrollo y crecimiento económico de Colombia. El sector agrícola en el país ha comenzado a tomar fuerza y se espera que, en un futuro cercano, se convierta en uno de los motores de la economía colombiana; un hecho que respalda dicha hipótesis es el informe del Departamento Nacional de Estadística donde se evidencia un crecimiento del 2,6% en el sector agropecuario, silvícola y pesquero, durante el tercer trimestre de 2019 frente al mismo periodo de 2018.
Partiendo de la importancia que hoy en día representa la agricultura colombiana, se hace necesario trabajar con las pequeñas y medianas empresas de este sector con el propósito de identificar la cadena de valor para sus clientes y de esta forma mejorar el desempeño de sus procesos. Se debe tener en cuenta que la cadena de valor se define como aquellas actividades que le dan un valor agregado al cliente y que involucra todo el camino que debe seguir el producto desde la recepción del pedido hasta la entrega al cliente final (Singh, Bahl, Kumar y Mann, 2018).
Las organizaciones presentan desperdicios de tiempo, espacio y costo a lo largo de su cadena de valor (Paredes-Rodríguez, 2017), lo cual impide cumplir con los estándares de productividad y rendimiento requeridos para responder ante la demanda del cliente final. Las metodologías Lean Manufacturing son de vital importancia para el diagnóstico de deficiencias en la cadena de valor, ya que con la implementación de estas herramientas se logra obtener buenos resultados en el desempeño operacional de las industrias (Nguyen y Do, 2016). la herramienta Lean Manufacturing llamada Value Stream Mapping o mapa de cadena de valor surge como una estrategia para investigar procesos, identificando actividades de valor agregado y sin valor agregado en forma de diagrama, para comprender cómo fluye el valor a través de una compañía (Baumont De Oliveira, Forbes, Schaefer y Miliisavljevic Syed, 2020).
De Steur, Wesana, Dora, Pearce y Gellynck (2016) utilizaron una revisión de literatura para mostrar el potencial del Value Stream Mapping (VSM) no solo para identificar y reducir las pérdidas y el desperdicio de alimentos, sino también como una forma de establecer vínculos con la retención de nutrientes en las cadenas de suministro agroalimentarias. Por el contrario, en esta investigación se pretende usar la herramienta mapa de cadena de valor como una estrategia para identificar todas aquellas actividades que no agregan valor en los procesos de cosecha y postcosecha de la piña, buscando la minimización de desperdicios generados a través del flujo continuo de toda la cadena de valor.
El artículo se encuentra distribuido de la siguiente forma: en la sección 2 se presenta una revisión de literatura sobre el uso de la herramienta VSM; en la sección 3 se expone la metodología utilizada para la aplicación de la herramienta de mapeo de cadena de valor, posteriormente en la sección 4 se presentan los resultados obtenidos luego de la aplicación de la metodología en los procesos de cosecha y postcosecha de la piña, terminando con las principales conclusiones en el apartado 5.
2. Revisión de literatura
A continuación, se presentan algunos estudios sobre la aplicación de la herramienta Value Stream Mapping (VSM) en diferentes escenarios, con lo cual se valida su amplia aplicabilidad.
Masuti y Dabade (2019) aplican la herramienta Value Stream Mapping a una empresa de producción de excavadoras, la cual presente problemas en la línea que impiden que la tasa de producción sea igual al takt time (ritmo al que se debe producir para cumplir con la demanda). Inicialmente los autores realizan un mapa de cadena valor actual para identificar aquellos inconvenientes en la línea, entre los que se puede destacar las averías de máquinas, la escasez de inventario en algunas estaciones y la falta de disponibilidad de herramienta. Luego de esto proceden a establecer unos kaizen de mejora al proceso, para luego simularlas en el mapa de cadena de valor futuro. Entre los principales resultados de la investigación se encuentra una reducción de 156 minutos de las actividades de valor agregado que sincrónicamente reduce 430 minutos de actividades sin valor agregado, lo que contribuye a una disminución de 586 minutos del tiempo de producción actual.
Huang, Kim, Sadri, Dowey y Dargusch (2019) realizan un mapa de cadena de valor dinámico en tiempo real para almacenar, analizar y visualizar el comportamiento de un determinado proceso de producción en una pequeña y mediana empresa considerando el flujo de material, la eficiencia de la máquina y el rendimiento laboral. Esta herramienta permite a la compañía tomar decisiones rápidas y eficientes sobre los procesos de fabricación que no están agregando valor al producto.
Knoll, Reinhart, y Prüglmeier (2019) elaboran una herramienta de toma decisiones empresariales que incluye la minería de datos sobre procesos logísticos internos unidos a un mapa de cadena de valor con el objetivo de que pueda ser utilizado por cualquier compañía para identificar desperdicios y derivar recomendaciones para las propuestas de mejora. La herramienta es probada en una empresa que se dedica a la fabricación de automóviles donde se tuvieron en cuenta 7500 partes y 15 procesos de referencia. Entre los principales resultados encontrados se resalta un tiempo de espera prolongado de ciertas piezas críticas y una baja capacidad de rastreo de algunos procesos.
Wesana, Gellynck, Dora, Pearce y Steur (2019) utilizan Value Stream Mapping como una herramienta para medir los desperdicios generados en la cadena de suministro de la leche en Uganda. Durante todo el proceso, de principio a fin, las pérdidas de alimentos a nivel de cadena se estiman en una magnitud de hasta el 14% lo que se traduce en un valor nutricional sustancial que desaparece del sistema alimentario, lo que compromete la capacidad de las personas para cumplir con sus recomendaciones nutricionales.
Acero, Torrealba, Pérez Montoya y Pozo (2019) aplicaron distintas metodologías de la filosofía Lean Manufacturing en la industria militar con el objetivo de mejorar los procesos logísticos, específicamente los tiempos de procesamiento de pedidos. Para lograr el objetivo se empleó la herramienta VSM, buscando identificar aquellas actividades que no agregan valor y definir planes de acciones, cuyos resultados probables de implementación son bosquejados en el VSM del estado futuro.
Deshkar, Kamle, Giri, y Korde (2018) implementan la metodología mapa de cadena de valor en una empresa que se dedica a la fabricación de bolsas de plástico, con el objetivo de identificar los recursos que no agregan valor y las estaciones cuellos de botella. Tanto el mapa de estado actual como el futuro se simulan y analizan en busca de diferentes atributos, como los tiempos de TAKT, los plazos de producción y el tiempo de procesamiento para evaluar la ganancia general obtenida mediante la implementación de las mejoras en los procesos (kaizen). Los resultados de la simulación predijeron una reducción en el tiempo TAKT de 46 minutos a 26.6 minutos. El número de rollos realizados por día aumentó de 28 a 50. La implementación general de los kaizen en el proceso de fabricación aumentó el tiempo de valor agregado en un 74.5%.
Paredes-Rodríguez (2017) implementa la metodología lean llamada Value Stream Mapping o mapeo de cadena de valor en una empresa embaladora de productos de vidrio, con el propósito de identificar y eliminar aquellas actividades que no agregan valor al proceso y a su vez mejorar el desempeño del área logística de la compañía, disminuyendo la sensación de un bajo nivel de servicio. Al final de la investigación se logra concluir que la implementación de la herramienta permite reconocer el comportamiento y las relaciones subyacentes dentro del proceso actual, y con base en este proponer mejoras que conlleven a un funcionamiento ideal del sistema, donde las actividades que generen desperdicio dentro del proceso sean mínimas y solo queden aquellas tareas que le den un valor agregado al producto por el cual el cliente sí esté dispuesto a pagar. Asimismo, Moreno Castillo, Grimando León y Salmanca Molano (2018) utilizan la herramienta Mapeo de la Cadena de Valor o VSM para diagnosticar una línea de producción de lácteos. El principal hallazgo correspondiendo al tiempo Takt es que la línea produce dos veces más rápido de lo que le demandan los clientes. Lo que ocasiona desperdicios por inventarios y transportes. Esto sirve para plantear alternativas de solución.
Viteri Moya, Matute Déleg y Viteri Sánchez (2014) desarrollaron un diagnóstico en una fábrica de bloques de concreto utilizando los principios de la filosofía de producción esbelta en pro de disminución de tiempos de producción y costos. Inicialmente los autores analizaron la situación actual de la empresa y reconocieron sus puntos débiles, haciendo uso de la herramienta mapa de cadena de valor (VSM). Luego procedieron a implementar la metodología 5s y la filosofía justo a tiempo. En contraste, Solding y Gullander (2009) realizaron mapas de flujo de valor dinámicos, ya que estos permiten el análisis de sistemas más complejos comparado al VSM tradicional. Esto se realiza mediante simulación ya que permite visualizar varios escenarios de uno o varios productos para así elegir la solución más factible.
Grewal (2008) uso la metodología VSM para visualizar el flujo de valor, desde la entrada del pedido del cliente hasta la compra, fabricación y envío del producto terminado en una pequeña empresa de manufactura, con el objetivo de identificar las oportunidades de mejora y así emprender el plan de mejora; dicho plan se plasmó en el VSM futuro. Los logros de la implementación fueron la reducción del tiempo de entrega, el tiempo del ciclo y el nivel de inventario. De igual forma, Barcia y De Loor (2007) diagnostican la situación actual de la logística de una empresa, para detectar problemas y eliminar posteriormente dichos desperdicios en el ensamblado de computadores.
Covas Varela, Martínez Curbelo, Delgado Alvares y Díaz Peña (2017) aplican la herramienta mapa de cadena de valor a una empresa agropecuaria, donde se proponen mejoras en los procesos logísticos, especialmente en las rutas de transporte en el que se utiliza una matriz de kilometraje para la entrega de productos permitiendo reducir costos y mejorar la satisfacción de los clientes. Asimismo, Delgado Alvarez, Covas Varela y Martínez Curbelo (2018) emplearon la herramienta Mapeo de la Cadena de Valor para determinar y eliminar las actividades que no agregan valor en los procesos logísticos de las cadenas de suministro agroalimentaria. Por el contrario, en este artículo se pretende identificar oportunidades de mejora específicamente dentro de los procesos de cosecha y post cosecha de una empresa productora de piña, a través del uso de la metodología Value Stream Mapping.
3. Metodología
La empresa en la cual se realizó el trabajo de investigación es una PYME ubicada en el área limítrofe de Guadalajara de Buga, en el departamento del Valle del Cauca, que se dedica al cultivo y comercialización de piña para el mercado nacional e internacional. En el mercado nacional cuenta con clientes minoristas y mayoristas y en el mercado internacional ha realizado exportaciones para países europeos como España, Portugal y Francia.
El proceso productivo de la empresa se puede observar en la Figura 1. La primera etapa consiste en la siembra, en el cual se selecciona la semilla de la piña apta para ser cultivada, denominada colino. Después de la siembra el cultivo empieza su etapa de mantenimiento donde se fertiliza, limpia y riega la planta para garantizar que tenga un desarrollo óptimo durante su periodo vegetativo. Cumplido el periodo vegetativo del cultivo se procede a la cosecha, en la cual un grupo de colaboradores recolectan la fruta en un remolque, transportado por un tractor que lleva la fruta a la planta de postcosecha. El proceso de postcosecha consiste en la clasificación de la fruta que llega de campo, esta selección se lleva a cabo por calibres que van del selecto hasta el corriente. Siendo el calibre selecto de calidad alta y el corriente de calidad baja. Cuando ya se ha clasificado la fruta se procede a empacarla en cajas de cartón, después se paletiza y estiba la carga para cargar el camión.
Los procesos más representativos que centralizan la actividad productiva de la empresa son los procesos de cosecha y postcosecha. Actualmente estos procesos presentan algunos problemas como retrasos por ineficiencia en el transporte interno, fallas de tiempo en cuanto a la entrega de la fruta, pedidos incompletos por las fallas de tiempo, entre otros; por este motivo se hace necesario la implementación de una herramienta como el VSM ya que permite buscar la forma de rediseñar los procesos con el propósito de eliminar las barreras e identificar las actividades que no agregan valor, descubriendo en el transcurso de su aplicación las oportunidades de mejora, por medio de diagramas que ilustran, analizan y comprenden el flujo de materiales e información necesaria en los procesos, usando una simbología específica y más amplia que otras herramientas Singh et al. (2018). Para el desarrollo de la investigación se tuvo en cuenta la metodología desarrollada por Nash y Poling (2008), la cual consiste en los pasos que se presentan en la Figura 2.
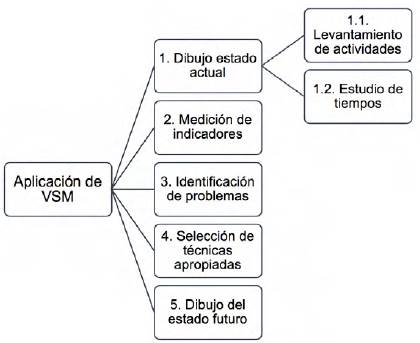
Fuente: Elaboración propia a partir de investigación realizada por Nash y Poling (2008).
Figura 2 Metodología de Aplicación de mapa de cadena de valor (VSM).
4. Resultados
Fase 1. Dibujo de estado actual
Esta etapa consiste en la elaboración de un diagnóstico de los procesos objeto de estudio con el propósito de realizar un levantamiento de las actividades que actualmente se realizan, identificando aquellas que no agregan valor al proceso y que constituyen desperdicios ya sea de tiempo, espacio, material o personal. Para lograr realizar el dibujo de estado actual se deben realizar previamente dos actividades: levantamiento de actividades y un estudio de tiempos en los procesos. A continuación, se presentan los resultados obtenidos.
4.1. Levantamiento y descripción de las actividades
Se realizó una visita de reconocimiento a la empresa productora de piña, visualizando sus procesos misionales. Se inició con la determinación de las actividades que se realizan en los procesos de cosecha y postcosecha; para esta caracterización se utilizó el diagrama de procesos, como representación gráfica del orden de las operaciones, transportes, inspecciones, demoras y almacenamientos que se presentan durante el proceso productivo (ver Figura 3).
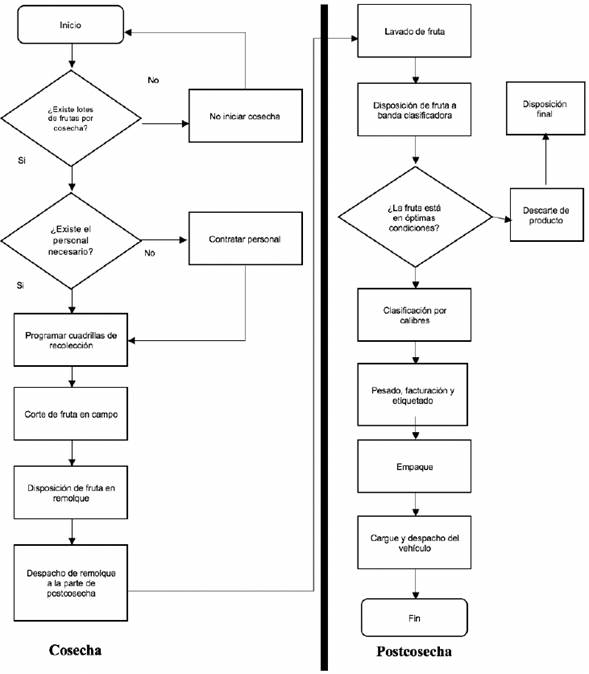
Fuente: Elaboración propia.
Figura 3 Representación gráfica de las actividades del proceso de cosecha y postcosecha.
El proceso de cosecha se activa con la revisión por parte del jefe de cosecha, donde este decide que lotes están listos para ser recolectados. Esta información es entregada a los operarios en campo, los cuales proceden a realizar el respectivo corte de la piña y apilar el producto en un remolque a través de una banda transportadora. El proceso finaliza con el transporte del remolque a la planta de postcosecha. Por su parte, el proceso de postcosecha inicia con el ingreso del remolque de piña recolectada por los operarios en campo. Luego se procede a realizar el lavado del producto y se ingresa a una banda transportadora, cuya función principal es llevar la fruta a los operarios de la planta, los cuales deben realizar la clasificación de la piña de forma manual. Cada tipo de piña debe ser pesada, etiquetada y empacada en cajones para el mercado nacional y cajas para exportación. Luego se procede a enviar a la zona de descarga para su posterior despacho al cliente final.
4.2. Estudio de tiempos de las actividades que involucra el proceso
Para la realización del estudio de tiempos de las diferentes actividades ejecutadas en los procesos de cosecha y postcosecha, se debe definir una unidad de medida. Se decide tomar el tiempo en segundos, con una unidad de seis piñas para cada actividad, ya que esta muestra favorece a la hora de calcular el ritmo promedio de ejecución de cada elemento, cuanto más largo sea, más difícil será formarse una idea de ese promedio. Se aplica la fórmula para calcular tamaño de muestra de las actividades de los procesos de cosecha y postcosecha con base al método estadístico propuesto por la Organización Internacional del Trabajo (OIT). El método estadístico consiste en efectuar un cierto número de observaciones preliminares (n') y luego aplicar la fórmula para un nivel de confianza de 95,45% y un margen de error de 5% (Ver ecuación 1).
Siendo:
n= Tamaño de muestra que se desea determinar.
n'= Tamaño de muestra preliminar.
x= Valor de las observaciones.
Para el caso de estudio se estableció una muestra preliminar de 6 observaciones para cada tarea y con ayuda de la ecuación 1, se procedió a calcular el tamaño de muestra de cada elemento de las actividades de los procesos previamente definidos en el levantamiento y descripción de las actividades que se realizan actualmente en los procesos.
Luego se procede a estimar el lapso que se demora la muestra representativa en pasar por todo el proceso, teniendo en cuenta el ritmo al cual trabaja el operario y un tiempo de suplemento basado en las condiciones del ambiente y trabajo. De manera seguida, se establece el tiempo requerido de cada una de las actividades de los procesos y con estos valores se calcula el tiempo de ciclo de la muestra representativa. La Tabla 1 resume el tiempo de ciclo de cada una de las actividades en los procesos de cosecha y postcosecha.
Tabla 1 Resumen de los tiempos de las actividades de los procesos de cosecha y postcosecha.
Cosecha | Postcosecha | ||||||
---|---|---|---|---|---|---|---|
Actividad | Tiempo | Minutos | Acumulado | Actividad | Tiempo | Minutos | Acumulado |
Revisión del informe de la fruta disponible para cosecha. | Llegada del remolque | ||||||
789,36 | 13,16 | 13,16 | que transporta la piña recolectada. Sumergir la fruta en el | 505,53 | 8,43 | 8,43 | |
Corte de la fruta por parte de | 34,64 | 0,58 | 13,73 | tanque, el cual contiene | 71,74 | 1,20 | 9,62 |
un operario. | agua, jabón para fruta e hipoclorito. | ||||||
Disposición de la fruta en la | Traslado de la fruta por la banda clasificadora. | ||||||
banda de cosecha por parte | 5,43 | 0,09 | 13,82 | 11,35 | 0,19 | 9,81 | |
de un operario. | |||||||
Clasificación de la fruta por parte de un operario. | 20,19 | 0,34 | 10,15 | ||||
Recibo de la fruta en la banda. | 11,73 | 0,20 | 14,02 | Selección del carril por | |||
Organización de la fruta por | donde se transportará | ||||||
parte de un operario en el remolque. | 26,27 | 0,44 | 14,46 | la fruta según las especificaciones de calidad. | 20,19 | 0,34 | 10,48 |
Empaque de la fruta en | |||||||
Diligenciamiento del reporte de cosecha. | 72,12 | 1,20 | 15,66 | cajones, para mercado | 83,37 | 1,39 | 11,87 |
nacional, y en cajas, para supermercados o exportaciones. | |||||||
Despacho del remolque con | Etiquetada (cuando es | ||||||
la fruta para la planta de postcosecha. | 4.282,11 | 71,37 | 87,03 | fruta para supermercado o exportación). | 11,12 | 0,19 | 12,06 |
Total | 5.221,66 | Pesado y facturación de la fruta. | 102,11 | 1,70 | 13,76 | ||
Transporte de la fruta a la | 247,27 | 4,12 | 17,88 | ||||
zona de carga y descarga. | |||||||
Cargue del vehículo con la fruta. | 8.867,37 | 147,79 | 165,67 | ||||
Total | 9940,24 |
Fuente: Elaboración propia.
El mapa de cadena de valor es una herramienta que puede ayudar no solo a mejorar los procesos en los cuales existen desperdicios, sino también, es una de las primeras metodologías a ser utilizadas en una organización que desee implementar distintas técnicas asociadas a la manufactura esbelta (ver Figura 4).
Las herramientas de Lean Manufacturing están enfocadas a la toma de decisiones, técnicamente factibles y económicamente óptimas, que afectan la actividad de la empresa tanto en el largo plazo como en el corto plazo. La Figura 4 muestra la forma en que se deben ser implementadas las herramientas de Lean Manufacturing en los procesos de las empresas manufactureras y de servicios, para mejorar la competitividad y productividad en el mercado.
Después de haber determinado el tiempo que se demora la muestra representativa en pasar por todas las etapas de los procesos, se procede a realizar el trazado del Value Stream Mapping de la situación actual. Para cumplir con este objetivo se utiliza programas como Microsoft Excel y Microsoft Visio Professional. En este software se logra consolidar el estudio de tiempos y la definición de actividades del proceso para crear así el mapa de cadena de valor actual.
Mapa del Flujo de Valor Actual del proceso de Cosecha
En el VSM actual presentado en la Figura 5, se puede observar el proceso de cosecha de la empresa productora de piña, el cual está conformado por un operario conduciendo el tractor, seis operarios haciendo la recolección de la fruta, un operario como empalme de la piña que se transporta por la banda cosechadora, y por último un operario que almacena la piña de manera provisional hasta el proceso de postcosecha. En total son 8 operarios que trabajan 8 horas, desde 7 a.m. hasta 4 p.m. Con base al estudio de tiempos, se recolectan 1500 piñas diarias en un promedio de 78,82 minutos, de los cuales 49,35 minutos representan tiempo que no agrega valor al proceso.
Mapa de Flujo de Valor Actual del proceso de Postcosecha
En el VSM actual exhibido en la Figura 6, se puede observar el proceso de post cosecha de la empresa productora de piña, donde se encuentra un operario recogiendo la piña del remolque de cosecha e insertando la fruta en un tanque para limpieza y desinfección, un operario la retira del tanque para disponer de la fruta en la banda clasificadora, un operario realiza la inspección y clasificación, un operario almacena la fruta en cajones, un operario verifica el tamaño y peso de la piña para colocarlas en cajas para mercado internacional, un operario la etiqueta cuando está dentro de las cajas, un operario la organiza transportándolas, en un gato hidráulico con estibas de 40 cajas, para pesado, facturación y el posterior cargue y envío al cliente final. En total son 7 operarios que trabajan a producción diaria, en total son 134,07 minutos para organizar 900 piñas de labor diaria aproximadamente, de los cuales 55, 58 minutos representan desperdicio de tiempo dentro del proceso y por ende se consideran actividades que no agregan valor.
Fase 2. Medición de indicadores
Es necesario aclarar algunos conceptos básicos para poder determinar el estado de la situación actual del VSM de la empresa productora de piña:
Tiempo de ciclo: Es el tiempo promedio entre la producción de dos unidades consecutivas.
Tiempo takt: es el máximo tiempo de ciclo permitido para producir un elemento y poder cumplir la demanda. La situación ideal es que el takt time sea igual al tiempo de ciclo, de lo contrario se puede incurrir en costos de faltantes o sobreproducción.
Tras haber explicado estos conceptos, se continua con el análisis de los resultados obtenidos de la simulación del estado actual. En la Figura 7 se observa como el tiempo de ciclo tanto en los procesos de cosecha y postcosecha son muchos mayores que el takt time, esto implica que si se mantiene el ritmo al que se trabaja en estos procesos, no se puede cumplir con las órdenes de pedido diarias establecidas por la compañía, por lo que cualquier mejora que provoque un menor tiempo de ejecución en estos procesos provocará una mayor productividad para la empresa objeto de estudio y por ende una mayor competitividad de esta en el mercado.
Fase 3. Identificación de problemas en el proceso actual
Dentro de los procesos de manufactura y servicios, se presentan actividades que no agregan valor y que se consideran desperdicio de tiempo, espacio, material o personas. Comúnmente en la literatura a estas actividades como "mudas" y se clasifican en 7 categorías según Pérez Rave et al. (2011), las cuales se presentan a continuación:
Sobreproducción: se refiere a programar la utilización de recursos en un momento y en cantidades que realmente no se requieren para satisfacer el consumidor.
Inventarios: su sostenimiento prologando y excesivo es perjudicial. Se divide en: materia prima, producto en proceso y terminado, genera costos de almacenaje y manipulación, propicia obsolescencia, defectos y sensación de poca capacidad.
Transporte: se caracteriza por el desplazamiento de elementos, bien sea materiales, producto en proceso/ terminado, personas o herramientas
Movimientos innecesarios: Representa todos aquellos desplazamientos innecesarios del operario o material dentro del lugar de trabajo. Normalmente una de las causas principales que lo provocan son un diseño de planta inadecuado
Tiempos de espera: Representa aquellos momentos en la que el producto no está fluyendo a través del proceso y se ve obligado a esperar. Estos tiempos se deben principalmente a carente nivelación de cargas de trabajo, fallas en la programación en equipos, ausencia de 5S, entre otros.
Procesos innecesarios: comprende actividades que existen por el diseño de procesos poco robustos e ineficientes, o por presencia de defectos.
Defectos: se refiere a aceptar, producir o enviar productos que no cumplen con las especificaciones del cliente, bien sea interno o externo. Genera, a su vez, procesos innecesarios. Esta muda genera altos costos de reproceso y una afectación al cliente final.
El proceso de levantamiento de actividades y estudio de tiempos no solo fue una herramienta para realiza el bosquejo de la situación actual de la organización, sino que también permitió la identificación de tres problemas que afectan el desempeño de los procesos objeto de estudio, a continuación, se presenta cada uno de ellos:
Exceso de manipulación de la fruta: En muchas de las actividades, el producto tiene demasiada manipulación por parte de los operarios, lo que genera una degradación de la calidad del producto y por ende genera que se convierta en producto no apto para la venta internacional o nacional. Este problema se encuentra englobado en un desperdicio (muda) provocada por movimientos innecesarios.
Falta de equipos y maquinarias óptimas para el desempeño de la compañía: Ya que la organización no cuenta con un plan de mantenimiento predictivo, preventivo y correctivo, debido a lo observado en la toma de tiempos, se evidencia una deficiencia en la banda cosechadora, por tener un diseño que no favorece a la eficiencia del proceso, generando retrasos. La ausencia de un plan de mantenimiento provoca que haya fallas mecánicas por falta de alguna pieza que se daña en cualquier momento.
Falta de capacitación: La existente falta de una base de conocimientos de cierto personal en cuanto a la disposición de la piña en la banda transportadora, la cual es el medio que se utiliza para el desplazamiento de la piña dentro del lote para llevarlo hasta un remolque, utilizado como centro de acopio provisional de la fruta.
Se observó que algunos trabajadores la organizaban de forma errónea en la banda, averiando la corona de la fruta y esto genera represamiento de esta, otros trabajadores dejan de recolectar algunas piñas en las plantas por falta de conocimientos básicos o consejos que le den indicios de que ya se puede recolectar dicha fruta. Esto contribuye primero a que se generen tiempos muertos por parte del operario del vehículo tipo tractor, el cual debe realizar constantes paradas, para que un trabajador desatasque la banda, o para que otro compañero de labor recolecte la fruta dejada en el surco, por parte del colaborador con menos capacitación, esto en cuanto a manipulación y recolección de la fruta. A lo anterior se puede agregar que estás inconformidades acarrea daños colaterales en cuanto a los requerimientos de la calidad del producto, debido a que hay algunas frutas que sufren cambios visibles en cuanto a su aspecto físico, como abolladuras o cambios en la tonalidad de su color, esto generado por la fricción o roce que sufren estas al estar represadas entre sí, y que en el primer contacto visual pueda que no sea percibido por parte del personal de almacenamiento provisional de cosecha.
Fase 4. Selección de las técnicas apropiadas para mejorar el proceso
No todos los desperdicios pueden eliminarse, pero con su reducción es posible impactar favorablemente el sistema productivo Pérez Rave et al. (2011). Para cumplir con este paso, se utilizó la misma metodología utilizada por Barcia y De Loor (2007), los cuales usaron una tabla donde se especificaba el problema, el tipo de desperdicio que este involucraba y la técnica que ayudaría a solucionarlo. En la Tabla 2 se evidencian dichas características.
Tabla 2 Mejoras propuestas para los problemas encontrados en los procesos de cosecha y postcosecha.
Problema | Desperdicio identificado | Técnica Lean a aplicar |
---|---|---|
Exceso de manipulación de la fruta | - Todas las actividades vinculadas a los procesos productivos de la empresa. | 5’s |
Falta de capacitación | - Corte de la piña por parte de operarios, en Cosecha. - Clasificación de la piña por parte de operario, en Post Cosecha. | Standard Work |
Falta de equipos y maquinarias óptimas para el desempeño de la compañía | - Despacho del remolque con la piña para la planta de Post Cosecha, en Cosecha. - Transporte de la piña a la zona de carga y descarga, y carga del vehículo con la piña, en Post Cosecha. | JIDOKA y TPM |
Fuente: Elaboración propia.
Para el primer problema se sugiere la aplicación de la metodología 5'S, debido al exceso de manipulación de la fruta se requiere organizar el trabajo de una manera que minimicé el desperdicio, asegurando que las zonas de trabajo estén sistemáticamente limpias y organizadas, mejorando la productividad y la seguridad.
Para el segundo problema identificado se propone utilizar la herramienta Standard Work, buscando incluir la documentación del proceso actual para los posibles cambios, las reducciones en la variabilidad, la capacitación más fácil de los nuevos operadores e inducción de cambios en los procesos.
En el tercer y último problema el cual es la falta de equipos y maquinarias óptimas para el desempeño de la compañía se propone como solución la herramienta Jidoka, ya que se busca que el operario detecte el problema durante el proceso de producción. Inmediatamente se informa a su supervisor o líder para que se programe un mantenimiento preventivo o correctivo si es necesario. También se requiere de la filosofía del TPM (Mantenimiento Productivo Total) cuyo objetivo es eliminar las pérdidas en producción debidas al estado de los equipos, es decir, mantener los equipos en disposición para producir a su capacidad máxima productos de la calidad esperada, sin paradas no programadas.
Fase 5. Dibujo del estado futuro
Para identificar las soluciones a los problemas que están presentes dentro de los procesos productivos de la empresa, es necesario plasmar las técnicas de Lean Manufacturing que se han diseñado para mejorar las actividades que no agregan valor en los procesos de cosecha y post cosecha de la empresa, teniendo como objetivo simular el comportamiento ideal del sistema en el mapeo de la cadena de valor futuro, comprándose con el VSM actual.
Mapa de flujo de valor Futuro del proceso de Cosecha
En la Figura 8 se puede observar como la primera mejora a establecer es la ejecución de Standard Work en la actividad de corte de la piña por parte de operarios, la cual busca reducir los desperdicios mejorando la capacitación de los trabajadores. La segunda mejora por efectuar es la aplicación de las 5's en la actividad de organización de la piña en el remolque por parte de operarios, con la que se disminuye el exceso de manipulación de la fruta. La tercera mejora que se sugiere es la implementación de Jidoka y un plan de mantenimiento productivo (TPM) en la actividad de despacho del remolque con la piña para la planta de post cosecha, la cual examina la falta de planes de mantenimiento de los equipos y maquinaria óptima que mejorarían el desempeño de la compañía.
Mapa de flujo de valor Futuro del proceso de Postcosecha
En el mapa futuro de Postcosecha (ver Figura 9), se indica como la primera mejora a realizar en este proceso, consiste en la aplicación de la metodología 5's en la actividad de limpieza de la piña, la cual trata de corregir el exceso de manipulación de la fruta. La segunda mejora implica el desarrollo de la herramienta Standard Work en la actividad de clasificación de la piña por parte de operario, ejecutándose para mejorar la falta de capacitación debido a conocer la adecuada realización de las actividades por parte personal. La tercera mejora consiste en la generación de un plan de mantenimiento productivo (TPM) en la banda clasificadora y en los equipos de transporte de la piña a la zona de carga.
En los mapas futuros de las Figuras 8 y 9 se puede notar, como afectan los cambios o mejoras que se han propuesto a lo largo del proyecto para eliminar las actividades que no agregan valor a los procesos productivos de la empresa. Señalando las áreas potencialmente mejorables con los estallidos amarillos (Kaizen burbuja de mejora). Con las mejoras que se han propuesto en este proyecto, comparado con el mapeo de la cadena de valor actual, la mejora en el tiempo total de ciclo de los procesos productivos sería aproximadamente del 19% (ver Figura 10), favoreciendo el tiempo de valor agregado, reduciendo el exceso de manipulación, la falta de capacitación y planes óptimos de mantenimiento en maquinarias.
Asimismo, por decisiones gerenciales de la empresa objeto de estudio, se decide simular el proceso de postcosecha utilizando el software de simulación Flexsim (ver Figura 11), con el objetivo de validar la efectividad de las mejoras dentro del proceso cuello de botella para la organización, comparando la simulación con el escenario actual. En la Figura 12 se exhibe el Throughput del proceso simulado en una semana de operación comparado con el proceso actual, donde se puede notar como con las mejoras propuestas para el proceso, se logra un incremento de 25% en la producción, lo que representa un mayor ingreso para la compañía en un futuro. De la Figura 13 se puede observar cómo es el comportamiento del inventario dentro de la planta de postcosecha, donde con las mejoras implementadas se logra una reducción de 40% en el inventario en proceso.
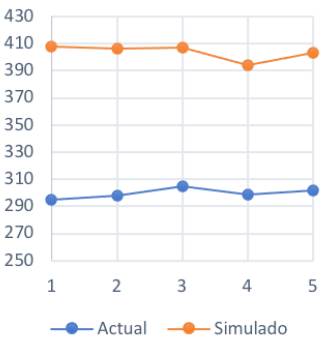
Fuente: Elaboración propia.
Figura 12 Comportamiento del Throughput actual vs simulación con mejoras en software Flexsim.
5. Discusión
En este artículo se aborda la aplicación de la herramienta mapa de cadena de valor, para analizar, modelar y estudiar el comportamiento de los procesos de cosecha y postcosecha de una pequeña y mediana empresa productora y comercializadora de piña a nivel nacional e internacional. Alineado a lo expuesto por Singh et al. (2018) la implementación de técnica mapa de cadena de valor conlleva a mejoras en la productividad de las compañías gracias a la reducción de movimientos innecesarios, reprocesos y todas aquellas actividades que no agregan valor.
Por otro lado, se considera fundamental el uso de Flexsim como soporte para la toma de decisiones de la gerencia de las compañías, siendo una herramienta vital para evaluar la efectividad de las propuestas de mejora obtenidas luego de un diagnóstico realizado a través de la técnica mapa de cadena de valor.
Por último, es necesario destacar que, aunque la herramienta mapa de cadena de valor ya había sido utilizada previamente para analizar procesos agroalimentarios Wesana et al. (2019), Moreno Castillo, Grimaldo León y Salamanca Mo-lano (2018), Covas Varela et al. (2017), Delgado Álvarez et al. (2018), esta investigación se concentra principalmente en detectar y eliminar los desperdicios generados en los procesos de cosecha y postcosecha de un pequeño productor agrícola, buscando el incremento de productividad y competitividad en el mercado nacional e internacional.
6. Conclusiones
La aplicación de la herramienta mapa de cadena de valor permitió a la empresa objeto de estudio diagnosticar los procesos críticos dentro de su operación, identificando tres problemas asociados al exceso de manipulación de la fruta, la falta de capacitación de los operarios y la ausencia de un programa de mantenimiento preventivo y correctivo para los equipos de la organización. A partir de los problemas identificados se proponen mejoras en los procesos de cosecha y postcosecha, utilizando técnicas lean manufacturing como lo son 5S, Jidoka, Mantenimiento Productivo Total (TPM) y Standard Work. Por último, se realiza un bosquejo del estado futuro de los procesos, incluyendo las mejoras identificadas, donde se logra proyectar una reducción del I9% aproximadamente en los tiempos asociados a actividades que no agregan valor dentro de los procesos.
El software Flexsim fue utilizado para validar el efecto de las mejoras propuestas en el mapa de flujo de valor futuro sobre los resultados actuales de operación del proceso en una semana. A partir de la simulación se logra concluir que las mejoras incrementan el Throughput en un 25% aproximadamente y disminuyen el inventario en proceso en un 40%.