1 INTRODUCTION
The biolubricant products are made up only or partially vegetable oils providing fulfill the requirements of international standars in terms of re-newability, biodegradability, toxicity and technical performance [1]. The proper base stock come from vegetable oils with high triglyceride content (sunflower, rapeseed, palm, jatropha, sesame, canola, soybean, sesame). The base stock provides lubricity, low volatility, biodegradability and it is non-toxic. However, vegetable oil has limitations such as low thermo-oxidative resistance and poor fluidity at low temperature. Therefore, these limitations can be improved by making a chemical modification on the ϐ-hydrogen atom in the glycerol backbone and unsaturation site of the fatty acid chains (transesterification, epoxidation) [2] [3] [4]. Another way to improve oil performance is achieved by using additive packages. These are formulated to: a) reduce the degradation of the oil caused by temperature, friction, with oxygen, humidity (antioxidants, demulsifiers); b) improve cold flow properties (freezing point depressants); c) increase tribological performance (friction modifiers, anti-wear agents, extreme pressure additives); d) enhance the viscosity index; e) other properties (anti corrosion agents, antifoams, surfactants, biocides).
Specifically, when analyzing the behavior of additives to improve lubricant performance, it is necessary to understand the concepts related to tribology. The lubricity is associated with the formation of the lubrication layer or tribofilm, on sliding surfaces. At higher lubricity less contact between surfaces and therefore decreases the friction [1].
The tribology studies three basic parameters: a) mechanical properties of tribo-system; b) the lubrication regime and its conditions and c) chemical and physical properties of the lubricant.
The mechanical properties of tribo-system refer to hardness of the material, the roughness of the surface, the contact geometry and the sliding mechanism of the interactive parts [1]. Three lubrication regimes have been studied. The boundary lubrication at high contact load and/or low sliding speed involves the formation of a thin tribofilm which causes the contact surfaces to rub together and generate high friction and wear [5]. The mixed lubrication occurs when sliding speed is increased or by decrease in contact load producing a mixed elasto-hydrodynamic (EHL) regime, the friction and wear rate decrease because the contact surfaces are now separated by a thicker tribofilm due to hydrodynamic elevation [5 ]. In Hydrodynamic lubrication regime the sliding contacts are now fully lubricated and the associated friction is dominated by viscous drag and lubricant resistance. In this way, there is no significant mechanical wear on moving parts, except fatigue [1] [6].
According to a study presented by Bruce [7], a typical boundary lubrication has a coefficient of friction (COF) greater than 0.1, while mixed lubrication/EHL produces a COF in the range of 0.01 to 0.10, and hydro-dynamic lubrication gives COF less than 0.01. In Wear Preventive test [8] the lubrication operates within a boundary or mixed regimes/EHL.
The viscosity of base stocks and its relationship with temperature and pressure is the main property responsible for the thickness of tribofilm. A viscous lubricant creates a thicker film but gives a lower efficiency due to a higher flow resistance, therefore the suitable viscosity value is a trade-off between lubrication and energy efficiency [1]. Other properties of biolubricant that can affect the resistance and stability of tribofilm include: pour point, volatility, temperature of thermal degradation and oxidative stability [1] [6].The tribology performance also depends on the molecular structure of base sotck, the triglycerides have the advantage that the molecule has polar (glycerol) and non-polar parts (fatty chain) [9]. The polar group is responsible for the adsorption or adhesion on a sliding surface, while backbone structure is responsible for the layer resistance of tribofilm [10]. The ester functional groups provide greater frictional properties and wear protection than mineral oils [11]. In the studies involving branching polyol ester gives better lubricity at an elevated temperature (> 100 °C) and under extreme pressure (> 981N load). Trimethylolpropane (TMP) and neopentyl glycol (NPG) esters may perform better at mild operating conditions, or in mixed/EHL lubrication regimes [12] [13 ]. The level of unsaturation can also affect the tribological performance, vegetable oils with a low degree of unsaturation such as avocado oil (0.985), olive oil (0.948), and peanut oil (1.102) exhibit superior frictional properties (for non-extreme condition) compared to high unsaturation such as soybean oil (1.451), corn oil (1.381) and sesame oil (1.232) [14].
1.1 Additives to improve tribological performance
In most applications, the base stock itself does not guarantee optimal lubricant properties, therefore it is necessary to add active surface agents. These act as a friction modifiers (FM), an anti-wear (AW) a and an extreme pressure (EP) additives. Usually FM promotes a softer layer that reduce sliding friction, while AW and EP additives form a sacrificial layer on the slip surface to minimize wear. The COF of a FM layer (0.01-0.05) is generally lower than EP and AW layers (0.06-0.15), but higher when compared to tribofilm in a hydrodynamic regime (<0.001). The EP additives has greater reactivity and its protective layer is stronger and thicker than AW agents. EP layer allows greater load tolerance. EP and AW additives are mainly used to minimize wear and improve lubrication for boundary and mixed lubrication /EHL regimes [1][15].
Classic package of AW and EP additives for lubricants was made of substances that contained elements such as sulfur, phosphorus, chlorine and heavy metals, some representative examples are: zinc dialkyl dithio phosphate (ZDDP), tricalcium phosphate (TCP); di-butyl 3,5-di-t-butyl 4-hydroxy benzyl phosphonate (DBP); tri-n-octyl thiophosphate and synthetic tri-n-octyl tetrathiophosphate. Even some like ZDDP, amino phosphonate and antimony dithiocarbamate were successfully tested in vegetable oils. These of additives are toxic and non-degradable , which carries a serious risk of intentional or accidental exposure [6] [16].
Right now, the lubricants industry directed towards the production of environmentally friendly additives for use in biolubricants [17].
One of the alternatives is to use nanoparticles (NPs) with size around 2 to 120 nm such as TiO2; Cu; Fe2O, Cu; CuO; ZnO; Cu2O, Al2O3 [18]. These are non-toxic, have been tested as AW and EP additives in mineral, synthetic and biolubricant oils [16 ] [19]. The lubricating performance of NPs depends on several factors such as size, geometrical shape, surface roughness [20], surface roughness of the sliding materials, concentration in oil [18] [21].
On the other hand, ethylene-vinyl acetate (EVA) and ethylcellulose (EC) are known as viscosity modifiers. They can also form a thicker film to obtain better friction, wear and load properties. EVA helps reduce friction mainly in the mixed lubrication regime, while EC is more effective in the lubrication of extreme limits [22]. Quinchia et al., tested EVA in concentrations of 0% as AW agent in sunflower, soybean and castor oil, achieving a reduction of friction and wear [23]. Substances phosphorus-free derived from triazines have been studied as additives to improve the lubricating properties, for example, 2,4,6-trioctylthio-1,3,5-triazine (OTT) and octylthiol (OT) [24]. Derivatives of S- [2- (acetamido) thiazol-1-yl] dialqui dithiocarbamate, in canola oil have been shown effective to reduce wear and increase the ability to reduce friction [25]. Derivatives of N, N-dialkyl dithiocarbamate-S-hydroxyethyl borates [26]. Derivatives of S-(1H-benzotriazol-1-yl) methyl N, N -dialquildithiocarbamates have a good anti-wear and friction reduction capacity similar to ZDDP [27]. Ionic liquids have also been formed as anti-friction properties [21], among the varieties are imidazolium-based liquid ionics with great potential: 1-butyl-3-methyl-imidazolium; 1-tetradecyl-3- (2-ethylhexyl) imidazolium [28] these liquids possess excellent lubricating properties including friction reduction, anti-wear capability and high load capacity or load carrying capacity [29]. However, the immiscibility of the ionic liquid in non-polar media such as fatty hydrocarbon and vegetable oil is the main disadvantage. This technical restriction can be overcome using liquid ionic microemulsions, for use in vegetable oil with a surfactant.
In this study, virgin sesame oil was blended with two additives: PE-wax and paraffin. The tribological properties were evaluated by Wear Preventive and Extreme Pressures tests.
2 MATERIAL AND METHODS
2.1 Materials
Virgin sesame oil (Bio-Essens®, Medellin-Colombia), the lipidie profile (Table 1) was made according to ISO 15304 by SGS® Laboratory (Bogotá D.C.-Colombia), sesame oil density: 0.98 g/cm3, kinematic viscosity: 0.35 cm2/seg. Polyethylene wax (PE-wax) (A-C 617 A®, Honeywell®, Bogota D.C.-Colombia), drop point: 100 °C, density: 0.91 g/cm3. Paraffin (Colwax® Bogotá D.C.-Colombia), melting point: 58-60 °C, density: 0.80 g/cm3.
2.2 Experimental design
An experimental design of a factor with three levels (see Table 2) was carried out. Factor: Type of additive. Levels: Sesame oil without additives; sesame oil/PE-wax; sesame oil/paraffin Response variables: Wear scare diameter (WSD) and COF.
2.3 Wear Preventive test
The Wear Preventive (WP) was performed according to ASTM D 4172-94 [8], parameters: load (147 N), rotation speed (1200 rpm), temperature (75 °C), time (1 hour). Chrome alloys balls were used, reference AISI 52100 (12.7 mm of diameter, hardness 60-66 HRC). The WSD of balls was measured using an optical microscope and ruler. The coefficient of friction (COF) was determined according to ASTM D5183-05 (2016) [30], it was calculated as follows
where / is the friction force (read directly from the instrument), L is the arm length (7.62 cm) and P is the applied load.
2.4 Extreme Pressure test
Through the Extreme Pressure test the last non-seizure load and weld point were determined according to the ASTM D2783-03 [31]. Parameters: load (variable), rotation speed (1760 rpm), temperature (25 °C), time (10 seconds). Wear Preventive and Extreme Pressures tests were performed in a four-ball tribometer, the scheme of testing is shown in Fig. 1.
3 RESULTS
3.1 AW performance of PE-wax and paraffin
The statistical summary and one-way analysis of variance for the WSD and COF with 95% confidence level are shown in Tables 3 and 4 respectively. From One way ANOVA, p-value for WSD was 0.366 and p-value for COF was 0.630, therefore the null hypothesis H0 was accepted, all population means are equal (Table 4).
The preventative wear test is measured in terms of the average wear scare diameter (WSD), higher WSD means lower lubrication characteristics. The ANOVA analysis performed to the test of preventive wear indicated that there were no significant differences of the averages in the three levels of the factor (control, PE-wax and paraffin) although a slight better performance of the PE-wax is observed respect to virgin sesame oil.
The WSD was very high in all blends with respect to the reports found in the literature (Table 5). For example, the WSD value for virgin sesame oil was 2.39 mm while the reports for olive, sunflower and coconut oil had values between 0.175 and 0.16 mm. The results obtained become even more critical considering that the tests were performed at loads of 147 N while the reports of the literature were at loads of 392 N. Both the tests carried out and the literature reports refer to the use of AISI 52100 balls, 75°C and 1 hour of testing. Tests made with balls of different metal alloy are not comparable.
Respect to COF no significant differences were observed when adding PE-wax and paraffin (Fig. 2, Table 4), therefore these substances are not classified as friction modifiers for vegetable oils. The COF values obtained experimentally are in the interval 0.051-0.053. The literature offers dissimilar COF values (Table 5), which makes a real comparison impossible.
TABLE 5 WP reports of vegetable oils from literature (Load 392 N)
Base stock | Additive | WSD(mm) | COF | Ref |
Olive | None | 0.175 | 0.078 | [34] |
Coconut | None | 0.601 | 0.101 | [34] |
Sunflower | None | 0.616 | 0.060 | [34] |
TMP ester jatropha | None | 1.280 | 0.022 | [21] |
TMP ester jatropha | 0.1% hBN | 1.514 | 0.026 | [21] |
Epoxidized oleic acid | None | 0.89 | 0.58 | [35] |
TMP ester palm | None | 0.8053 | 0.081 | [36] |
NPG ester palm | None | 0.659 | 0.092 | [12] |
Polyol ester | ILs | 0.0681 | 0.750 | [21] |
|3.2 Extreme pressure Evaluation of additives
By means of this test, the performance of polyethylene wax and paraffin was evaluated as extreme pressure additives, in terms of last non-seizure load and weld point (Figs. 3 and 4). The paraffin slightly showed a better performance with respect to the PE wax in both last non-seizure load and the point of weld point. The weld points were: virgin oil 235 N, PE-wax 235 N and paraffin 314 N (Fig. 4), both additives are not considered as extreme pressure additives, because the weld points were very low. Typical weld point values reported in the literature using ISI spheres: polyol ester (> 1569 N) [13]; trimethyl ester palm oil 1000 N [13 ], polyol ester (1569 N) [32], mineral oil (1000N) [13]. The last non-seizure load was 127 N for virgin sesame oil and additive with PE wax, slightly higher was found for the oil additive with paraffin 157 N (Fig. 4).
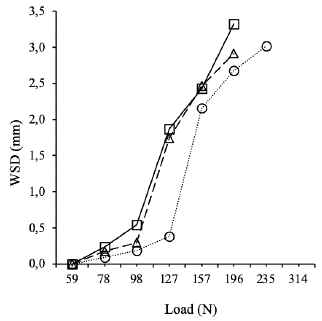
FIG. 3 EP test. DPH vs Load: sesame oil (squares); sesame oil+PE-wax (triangle), sesame oil+paraffin
In this study, the performance of wax and paraffin as an anti-wear and extreme pressure additive was analyzed and these additives were chosen because they are act as both external and internal lubricants by increasing the low of polymer by decreasing the friction of the melted plastic in plastics transformation processes, such as injection, extrusion, blowing, among others [33]. However, when used as additives to improve lubricating performance in vegetable oil, the result was low.
In general, the additives used as anti-wear and extreme pressure agents are molecules that have specific chemical structure, which interacts with the metal surface through various mechanisms: i) Physical adsorption of polar materials (Cl- or OH-) on metal surfaces example: Long-chain fatty acids and esters, sulfurized fatty acids, molybdenum compounds, long-chain phosphites, and phosphonates [37]. ii) Reacts chemically with the metal surface to from a layer (normally a metal soap) that reduces frictional wear at low-medium temperature and loads. Example: Neutral organic phosphates and phosphites, zinc di-alkyldithiophosphates [38]. iii) Reacts chemically with the metal surface to form a layer, e.g. as a metal halide or sulfide which reduces frictional wear at high temperatures/loads example: Sulfurized or chlorinated hydrocarbons, acidic phosphorus-containing materials, and mixtures thereof; some metal soaps, e.g. of lead, antimony, and molybdenum [37]. Therefore, the chemical structure of paraffin and wax-PE do not meet the characteristics that must have anti-wear and extreme pressure additives. Paraffins are waxy products derived from petroleum, it is composed of straight chain hydrocarbons, without branches, they have a "macro-crystalline" structure and lengths from C18 to C40, without polar or reactive groups at the ends of the chain. The wax-PE, is a homopolymer of LDPE, with molecular weight of 2,000-8,000, with slightly branched structure, without polar or reactive groups at the ends of the chain.
4 CONCLUSIONS
The polyethylene wax and paraffin wax did not improve the lubricating characteristics of virgin sesame oil. The results of wear scare diameter and coefficient of friction derived from Wear Preventive testing did not show significant differences when adding 1% wax (1% w/w) and paraffin (1% w/w) with respect to the virgin oil. With respect to the extreme pressure test, the addition of paraffin slightly improved the last non-seizure load and the weld point, however the data determined experimentally allow to conclude that wax-PE and paraffin did not have a performance as extreme pressure additive.