I. INTRODUCCIÓN
En el sector industrial uno de los procesos importantes es la transferencia de calor, por ejemplo, la refrigeración, pasteurización y esterilización. La industria aprovecha las propiedades de la transferencia térmica utilizando dispositivos diseñados para elevar o disminuir la temperatura de materia prima o producto, denominando a esta técnica “intercambio de calor”. Existen varios tipos de intercambiadores de los cuales el intercambiador de coraza tubo es el más común (sobre un 30% de los intercambiadores instalados) seguido por el de platos (20%) [1].
La industria del Valle del Cauca (sector químico, papelero, alimenticio, farmacéutico) emplea intercambiadores de calor para suplir los servicios auxiliares de vapor y/o agua caliente. Con la finalidad de cumplir con estándares de producción y seguridad de las plantas, se han automatizado los procesos donde intervienen el intercambiador de calor, incorporando estrategias de control que regulan la temperatura de salida del producto a valores deseados. Sin embargo, el desconocimiento de la teoría de control por parte de los operarios y técnicos encargados de las plantas ocasiona estados de ineficiencia y aumentos de costos en la operación de los sistemas de intercambio térmico. Con base a entrevistas y visitas técnicas a empresas de la región, se detectó que en el 100% de las empresas encuestadas, la sintonía de los controladores de los intercambiadores de calor se realiza a partir de pruebas empíricas de ensayo y error basadas en la experiencia, impactando la calidad del producto final. Este panorama no es un problema propio de la región del Valle del Cauca, en el 2003 [2] se realizó observaciones en lazos de control de industrias Norte Americanas detectando que el 85% de los controladores presentaban una pobre sintonía y el 30% operaba en modo manual. Entre los años 2004 y 2005, en [3] se realizó un estudio similar, mostrando los resultados de una auditoría a 700 lazos de control en 12 compañías brasileras, estableciendo las siguientes problemáticas: válvulas con excesivo desgaste (14% de los casos), válvulas con problemas de adherencia e histéresis (15%), lazos operando en modo manual (16%), controladores saturados (24%) y oscilaciones con problemas de sintonía, acoplamiento, disturbios y fallos de actuadores (41%).
Lo anterior evidencia la necesidad de fortalecer los métodos y procedimientos aplicados en la industria en torno a la sintonía de lazos de control, con el propósito de brindar solución a muchas de estas problemáticas y mejorar la productividad en la operación. El fortalecimiento del conocimiento debe realizarse en todas las etapas de la ingeniería de control [4]: ingeniería conceptual, ingeniería básica, ingeniería de detalle, implementación, puesta en marcha y mantenimiento.
En la ingeniería conceptual se analiza y se caracteriza el proceso. En el caso del intercambiador de calor, sus características no lineales y disturbios, con rangos de temperaturas de productos amplios y variables, representa un sistema difícil de controlar. Aunque el PID es el controlador más simple y comúnmente usado para el control de intercambiadores, el 62% de las empresas encuestadas lo emplean, no siendo apropiado para un proceso de características no lineales o tiempos muertos variables [5]. Considerando lo anterior, existen un gran número de algoritmos de control implementados en intercambiadores de calor: desde el tradicional PID [6] hasta controles inteligentes [7-10], robustos [11-13] y no lineales [5].
La ingeniería básica establece los requerimientos o especificaciones de diseño y define la estrategia de control. Las estrategias de control más empleadas a nivel académico y a nivel industrial son: el control realimentado [14] con algoritmos de control de PI, PID, PID avanzado y PID adaptativo; el control anticipativo, usado en conjunto con el realimentado para aumentar los grados de control del sistema; la estrategia de control cascada usada para dar robustez y velocidad de respuesta; control por derivación [15] y el control manual, empleado en aquellos casos en el que no se requiere un control preciso y robusto de la temperatura. La Fig. 1, visualiza los resultados de las visitas a la industria del Valle del Cauca.
La ingeniería de detalle implica obtener el modelo matemático del proceso y los parámetros de sintonía del controlador. Obtener el modelo matemático, es una fase fundamental en el diseño de los sistemas de control, ya que afecta directamente el desempeño y robustez de los controladores.
Los métodos de identificación que han sido aplicados en intercambiadores de calor a nivel de investigación, con potencial para ser aplicados a nivel industrial son los métodos no paramétricos, paramétricos y el analíticos [16,17]. Sin embargo, en el 100% de las empresas consultadas, afirmaron que el modelo no es necesario a la hora de implementar una estrategia de control clásico debido a que la sintonía del controlador PID lo realizan de manera heurística. Las empresas no conocen el modelo de su proceso, por dos razones: falta de conocimiento de teoría de identificación de sistemas o por el arduo trabajo que implica esta tarea.
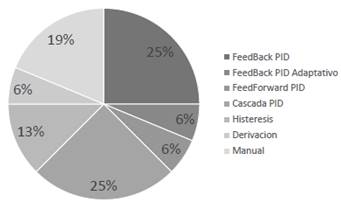
Fig. 1 Estrategias de control de la industria detectadas en la encuesta realizada por el grupo de institución UIADTI - Sena en la industria Vallecaucana.
La sintonía del sistema de control hace referencia al ajuste de los parámetros del controlador para obtener una respuesta “optima” o deseada del intercambiador de calor. Siendo una respuesta “optima” para el proceso según las especificaciones de diseño, por ejemplo: estabilidad, regulación, rechazo de disturbios, tiempo de respuesta, oscilaciones, error, eficiencia energética; siendo estas especificaciones las bases para definir los índices de desempeño para la evaluación del lazo de control en la ingeniería de puesta en marcha. Esta revisión de control de temperatura en intercambiadores de calor tipo coraza tubo aborda las principales estrategias de control empleadas en la industria y para investigación, técnicas para la obtención de modelo, algoritmos de sintonía de controladores y los índices de evaluación de desempeño de los lazos de control de temperatura.
II. CONTROL DE TEMPERATURA - INTERCAMBIADOR DE CALOR
Los intercambiadores de calor facilitan la transferencia térmica entre dos fluidos que se encuentran a distintas temperaturas, generalmente evitando la mezcla entre sí. El proceso de transferir el calor de un medio a otro en el intercambiador se lleva a cabo mediante los fenómenos conocidos como conducción y convección [18]. Por conducción, se entiende como la transferencia de energía de las partículas más energéticas de una substancia hacia las adyacentes menos energéticas, como resultado de interacciones entre esas partículas. La convección se da entre una superficie sólida y el líquido o gas adyacente que está en movimiento; cuanto mayor es la velocidad del fluido, mayor es la transferencia por convección.
Existe una gran variedad de intercambiadores térmicos, por ejemplo [19]: torres de enfriamiento (contacto directo), tubos concéntricos, tubos coraza, placas; siendo el de tubo-coraza (Fig. 2) el más utilizado en aplicaciones a nivel industrial dado que permite temperaturas y presiones superiores a los de placas (300 psia y 150 ºC).
El intercambiador de placas está orientado a aplicaciones con sustancias inocuas y el de tubo-coraza a aplicaciones de la industria en general. De acuerdo con la función en el proceso, los intercambiadores de calor se pueden clasificar en:
Enfriador de líquidos o gases por medio de agua.
Permutador, realiza una doble función, calentar y enfriar los dos fluidos que intervienen en la operación.
Calentador, imparte calor a un fluido por medio de vapor.
Rehervidor, buscar rehervir el líquido necesario para la destilación.
Condensador, condensa vapor o mezcla de vapores.
Vaporizador, es un calentador que vaporiza parte de un fluido.
Caldera de recuperación, genera vapor a partir de gases de proceso.
Dado que el intercambiador de calor es usado en la industria alimentaria, petroquímica, farmacéutica, la industria de pulpa y papel, servicios auxiliares industriales de calentamiento de agua, generación de vapor, recuperadores, enfriadores; se hace indispensable realizar un adecuado control. En operación, el intercambiador está sujeto al desgaste, ocasionado por sustancias de arrastre presente en los fluido e incrustaciones debido al almacenamiento de las sustancias que son transportadas por el fluido, por ejemplo, los gases que se separan del agua durante el calentamiento o por el fenómeno de contaminación del agua generando depósitos principalmente de sílice y lodos [20]. Además de la obstrucción y el desgaste, el intercambiador en la operación presenta perturbaciones, disturbios en el proceso, cambios intempestivos de las variables que degradan la operación del intercambiador y generan perdida de eficiencia en la operación de este, haciendo más relevante el control de todo el proceso de intercambio térmico.
Para realizar el control del intercambiador es importante conocer los elementos que componen el proceso de intercambio térmico. La Fig. 3 hace referencia a un intercambiador de calor [21] al que le entran dos fluidos, que corresponden al “producto” o fluido que se pretende calentar y el “fluido calor portador”, fluido que va a calentar al producto.
El caudal del producto de entrada, Q P (t), es medido mediante un transmisor de flujo FIT 002, este fluido pasa a través de la válvula de control FCV 001, a la salida del intercambiador pasa por el caudalímetro FIT 005. La temperatura del producto es medida tanto a la entrada, T EP (t), como a la salida del intercambiador; en la entrada mediante los instrumentos termómetro TI 001, sensor TE 001 y el transmisor indicador de temperatura TIT 001, y en la salida a través del termómetro TI 003, el sensor TE 003 y el transmisor indicador de temperatura TIT 003.
El caudal de entrada Q C (t), fluido calor portador, es medido por el caudalímetro FIT 004, flujo que también pasa por la válvula de control FCV 002 y a la salida del intercambiador es medido por el transmisor de flujo FIT 005. La temperatura de entrada T EC (t) del fluido calor portador es medida mediante los instrumentos termómetro TI 004, sensor TE004 y el transmisor indicador de temperatura TIT004 y la temperatura de salida es medida por los instrumentos: termómetro TI 002, sensor TE002 y el transmisor indicador de temperatura TIT002.
Dentro de los factores para tener en cuenta en el control de los intercambiadores de calor se destacan la presión del vapor o del fluido de alimentación, las fluctuaciones en el caudal del producto, las variaciones en la temperatura del producto, calor específico, retardos del proceso. Considerando estos factores, es posible controlar: la temperatura en la línea de fluido calor portador, la temperatura en la línea de producto, temperatura en la línea de fluido energético con control de nivel de producto, control de temperatura mediante regulación primaria de presión y secundaria de flujo energético, control anticipativo (FeedForward) para la compensación de perturbaciones en un intercambiador de calor. En un adecuado sistema de control se espera que el proceso funcione en condiciones estables de operación independiente de perturbaciones y desajustes, que responda de manera oportuna, continua y que trabaje bien ante diferentes cambios o condiciones de operación del proceso.
III. ESTRATEGIAS DE CONTROL
En general, el objetivo de los sistemas de control es cumplir con las especificaciones de desempeño dadas para el proceso, definiendo valores o rangos considerados como aceptables para el comportamiento deseado. Típicamente, existen dos problemas de control [22]: seguimiento de la referencia y rechazo de disturbios. Sin embargo, en muchos procesos industriales el seguimiento de referencia es menos crítico que el rechazo de disturbio, debido a que los cambios de la referencia pueden darse únicamente cuando cambia la producción. La robustez e incertidumbre del modelo y sensibilidad al ruido de medición son objetivos secundarios de control. Entre las estrategias empleadas para realizar la transferencia calor y controlar la temperatura del producto, encontramos: Control realimentado (FeedBack), control anticipativo (FeedForward) [11,23], para el rechazo de perturbaciones; control cascada [21] y el control por derivación para aplicaciones específicas.
A. Control realimentado - FeedBack
El objetivo del sistema es controlar la temperatura de salida del producto. El controlador cambia su salida en función al error entre la temperatura de referencia y la temperatura de salida del producto T SP (t). La principal ventaja de esta estrategia radica en su simplicidad de implementación y la capacidad de compensar cualquier tipo de perturbación del sistema [24]. En la Fig. 4 puede verse el esquema de control realimentado actuando directamente sobre la válvula de calor portador.
B. Control anticipativo - FeedForward.
Aunque el control realimentado es el más usado a nivel industrial, su desventaja radica en que la compensación de los disturbios no se realiza hasta que la variable controlada T SP (t) se desvíe del punto de operación, es decir, la perturbación debe propagarse en todo el proceso antes de ser compensada. Si se requiere recuperar el punto de operación rápidamente, se puede optar por la implementación de control anticipativo, de la Fig. 5, justificando la inversión en instrumentación adicional.
El control anticipativo se combina con el control realimentado, donde el primero compensa la variable controlada antes de que se desvié midiendo directamente las perturbaciones; y el segundo mantiene el punto de operación de la temperatura de salida. Las perturbaciones medibles en el proceso son: temperatura de entrada de producto T EP (t) y el flujo del producto Q P (t) manteniendo como la variable manipulada el flujo del fluido CalorPortador Q C (t).
C. Control Cascada
En el esquema de control cascada, Fig. 6, la salida del controlador de temperatura es la referencia del controlador interno de flujo o vapor basado en un lazo de realimentación simple [24]. Esta estrategia elimina los efectos de disturbios internos de entrada o salida del proceso, corrige las alinealidades e incertidumbres del lazo interno.
Para el caso de un controlador externo de temperatura y un controlador interno de flujo (ver Fig. 6), las variaciones del flujo CalorPortador son corregidas inmediatamente, por el controlador de flujo interno y el controlador de temperatura externo se encarga de compensar las variaciones de temperatura por otras causas. El significado físico de la señal del controlador de temperatura sería el flujo CalorPortador que se requiere para mantener la temperatura en el punto de operación. Hay que notar que el lazo de control interno debe ser mucho más rápido que el externo, cancelando las variaciones de flujo antes de que afecte la temperatura de salida del producto.
D. Control Integrado
La Fig. 7 muestra un control integrado de realimentación, anticipativo y cascada [15], que brinda un mayor grado de libertad en el ajuste de las especificaciones de diseño del sistema de control, por ejemplo:
Rechazo de perturbaciones (Control anticipativo).
Minimizar variación de flujo del fluido CalorPortador (Control cascada).
Seguimiento de la referencia (control realimentado).
La integración de estas tres estrategias permite la optimización del control de temperatura del intercambiador de calor para minimizar la variación del proceso, maximizar la calidad del producto y garantizar la eficiencia energética del proceso.
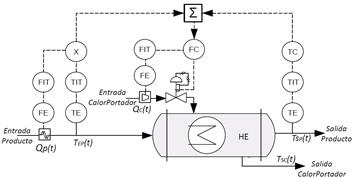
Fig. 7 Estrategia de control cascada más un control anticipativo para un intercambiador de calor [15].
E. Control por derivación
Si el intercambiador responde lentamente, la regulación de la temperatura se realiza con un controlador actuando sobre una válvula de tres vías para derivar el flujo del intercambiador. En [15,25] se muestra dos variaciones para este esquema de control: derivación en la línea CalorPortador y derivación en la línea del producto. Este esquema logra una respuesta más rápida frente a lazos de control con válvula de dos vías, debido a que se afecta casi inmediatamente la temperatura de salida al evitar que el flujo CalorPortador o producto atraviese el intercambiador. Hay que tener en cuenta que la derivación del producto no se puede realizar en aquellos procesos donde se requiera que todo el producto aumente o disminuya su temperatura, por ejemplo: procesos de pasteurización y esterilización.
IV. MODELO DEL INTERCAMBIADOR DE CALOR PARA EL CONTROL
En el control de procesos, la identificación del sistema permite determinar, con suficiente exactitud para fines de control, la estructura y parámetros de un modelo matemático que reproduzca las variables de salida del proceso ante un conjunto de señales de entrada en el sistema real. Estos modelos matemáticos son usados para describir o entender la realidad de procesos químicos, mecánicos, eléctricos y biológicos.
En forma general existen tres metodologías de identificación de procesos [26]: la primera metodología, identificación analítica, hace uso de relaciones establecidas, por ejemplo leyes físicas o químicas, que se pueden aplicar al sistema; la segunda metodología, identificación no-paramétrica, se basa en aplicar señales especiales de prueba al sistema para luego ajustar un modelo matemático; y tercera, la identificación paramétrica [27], que permite caracterizar al sistema con un mayor grado de ajuste ya que incorpora modelos de perturbación en su estructura.
A. Identificación analítica
El desarrollo del modelo se basa en las relaciones fisicoquímicas del proceso como balances de energía y masa [26]; obteniendo un modelo complejo y no lineal en la mayoría de los casos, requiriendo de una gran experiencia y conocimiento del proceso para su desarrollo.
El modelo matemático de un intercambiador de calor es escrito en términos de ecuaciones diferenciales parciales (PDEs) en [28,29]. La solución de las ecuaciones PDEs puede ser complicado, por lo tanto, un modelo de parámetros concentrados es recomendable cuando el propósito es el control del intercambiador, tal como se presenta en [30,31]. El modelo se obtiene dividiendo el largo de intercambiador en N regiones de igual tamaño y se asume que en cada región la temperatura es uniforme. El número de regiones depende de la precisión que se quiere obtener con el modelo. Para cada región se realiza un balance energético. Las Ec. 1 y Ec. 2 describen el balance energético en cada una de las regiones:
Donde y
son las temperaturas promedio.
los coeficientes de calor especifico de cada fluido
;
,
son los flujos volumétricos de los fluidos
;
,
volumen de cada región
son las densidades de los fluidos
coeficiente del intercambiador
área de contacto
y
es el tiempo
. El modelo matemático definido con las Ec. 1 y Ec. 2 tiene la habilidad de aproximar el comportamiento transitorio de diferentes tipos de intercambiadores, tal como se muestra en [30].
B. Identificación experimental
Obtener el modelo matemático mediante la identificación analítica requiere de una gran cantidad de tiempo de ingeniería, sin mencionar las dificultades en el modelado ocasionadas por las dinámicas complejas y desconocidas del intercambiador. La alternativa a este problema es implementar un método experimental para realizar la identificación del sistema. Esta identificación realiza la aproximación de un modelo matemático a la respuesta, asignando valores numéricos a los parámetros del modelo mediante la observación de datos experimentales [32]. De acuerdo con [33], los métodos experimentales se pueden dividir en dos categorías: paramétricos y no paramétricos.
1. Métodos no paramétricos
Estos métodos de identificación se caracterizan por ser usados cuando las dinámicas del sistema no pueden ser expresada por un número finitos de parámetros y al ser aplicados no entregan valores a los parámetros del modelo sino curvas o funciones. Entre las señales de pruebas experimentales utilizadas para la identificación se encuentran las de tipo escalón y las secuencias binarias pseudoaleatorias (PRBS) [26]; en algunos casos se emplean también señales sinusoidales para determinar la respuesta en frecuencia del sistema.
La limitación de esta técnica radica en que los modelos obtenidos son completamente determinísticos, es decir no consideran modelos de perturbación, no apropiado para el desarrollo de estrategias avanzadas de control. Aunque estas técnicas son sensibles al ruido y de baja precisión, son empleadas a nivel industrial debido a la fácil implementación. Sin embargo, perturbar mediante una señal de prueba a un proceso industrial en operación puede ocasionar modos no deseados, alterando la producción, por tal razón las empresas optan en no realizar la identificación en línea.
Los métodos implementados a nivel industrial se basan en la curva de reacción del proceso, como el método de la tangente de Zieglers-Nichols que aproxima la dinámica del sistema a un primer orden mediante una recta tangente al punto de inflexión de la curva de reacción; en [7] se emplea para el diseño de un control difuso. En [33], en lugar del punto de inflexión se emplea el valor del 63% de la salida. Otro método de identificación que aproxima la dinámica a un primer orden se muestra en [34] (método de Smith).
Para aproximaciones del intercambiador de calor a un sistema de segundo orden, el método de polos múltiples de Strej con o sin tiempo muerto es utilizado en [9], donde se emplea una multiplicidad de polo de dos y en [8], y en [13] con multiplicidad tres para el diseño de un controlador H2 y un H∞.
En [35], se presenta una comparación de técnicas de identificación de modelos matemáticos para sistemas de primer y segundo orden. Algunas de estas técnicas como: método de tres puntos (Jahanmiry y Fallanfi, Startk), Métodos de áreas característica de Nishikawa, Vitecková; no se han implementado en ambientes industriales para la identificación del modelo de intercambiadores de calor. Sin embargo, estas técnicas pueden emplearse sin limitaciones en la identificación del modelo.
2. Métodos paramétricos
La adaptación de la teoría de mínimos cuadrados en la identificación se basa en aceptar como cierto de que el proceso puede ser representado por un modelo de estructura fija, generalmente una ecuación lineal en diferencias, lo que implica que dicho modelo tiene naturaleza discreta [26]. Estos algoritmos pueden emplearse tanto fuera de línea (no recursiva) para determinar un modelo invariante con el tiempo o en línea (recursiva) para estimar parámetros variables con el tiempo.
En muchas investigaciones se han usado métodos paramétricos para obtener el modelo matemático de intercambiadores de calor, donde se aplican señales seudo aleatorias (PRBS) como señales de prueba. Los resultados muestran que es posible describir el comportamiento del intercambiador con estos modelos. En [16], se aplica el modelo ARX a cuatro intercambiadores de calor de diferente tipo. En [36] se hace uso de un modelo ARMAX para obtener el modelo del intercambiador y luego hacer uso del modelo para diseñar dos controladores PID's diferentes.
V. ALGORITMOS DE CONTROL Y SINTONÍA
A nivel industrial se emplean pocos controladores, Ver Fig. 1, sin embargo, existen una gran variedad de controladores avanzados aplicados a nivel académico siendo en su mayoría simulaciones. El controlador PID sintonizado con el método de curva de reacción de Ziegler-Nichols (ZN) [24] es el método tradicional en la industria gracias a su simplicidad en las reglas de sintonía basadas en el decaimiento de 1/4 del error; este criterio de sintonía puede ocasionar un pobre amortiguamiento y poca robustez debido a las altas ganancias del controlador. En [10,12,23,37] se realiza un control basado con estas reglas de sintonía para intercambiadores coraza-tubo simulados, en [11] se realiza una simulación adicionando un control anticipativo para el flujo de entrada, el cual disminuye el tiempo de establecimiento y el sobrepaso. En [21] se realiza un control PI Ziegler-Nichols versus la herramienta PIDTuner de Matlab® en un intercambiador de laboratorio de nivel industrial.
Ziegler-Nichols es un método basado en tablas, de ahí radica su gran acogida en la industria, pero debido a los grandes sobrepasos que puede ocasionar, algunos autores han modificado los valores de sintonía del controlador PID [25]. En [8,13,37] se aplica en simulación las reglas de Cohen-Coon obteniendo respuestas similares al ZN; en [37] se hace uso de las reglas CHR (Chien-Hrones-Reswick), la cual tiene una variación para realizar un ajuste para seguimiento o regulación, este controlador presenta menores sobrepasos. Por último, en [8], se implementa un controlador Strej para un modelo de intercambiador de polos múltiples.
Ziegle-Nichols tiene una segunda metodología de sintonía, la cual implica llevar al sistema al borde de la inestabilidad para determinar la ganancia y frecuencia critica. Este proceso puede no ser seguro para el intercambiador de calor, por lo cual se emplea el método de oscilación por relé [38]; en [23] se simula este controlador y en [36] se implementa en un control real obteniendo la ganancia y frecuencia critica sin necesidad de llevar al sistema a un punto de operación no segura.
Como se mencionó en la sección IV, el modelo del intercambiador de calor posee una dinámica de tiempo muerto, por lo cual un controlador lineal como el PID no puede compensar efectivamente este efecto; por lo que se requiere el uso de controles predictivos. El controlador Smith es considerado como el primer algoritmo predictivo de control [39] al contener en su estructura el modelo matemático del sistema. En [11], el predictor Smith prueba que puede compensar los efectos del tiempo muerto solamente si se conoce el modelo exacto del intercambiador de calor; además, se implementa en conjunto con una estrategia FeedForward con lo cual disminuye las fluctuaciones de temperatura debido al cambio del flujo de entrada. En [40], se realiza la comparación de un predictor Smith con un PI por Ziegler-Nichols y un PID Tyreus-Luyben. El control por modelo interno (IMC) [41], es una estructura que hace uso de un modelo lineal del proceso en paralelo con el proceso real, para la compensación del tiempo muerto; mediante el ajuste de un solo parámetro. En [8,23] se prueba en simulación que el control IMC limita los efectos del error causados por la incertidumbre en el modelo; en [36] se demuestra que el IMC responde mejor que el controlador por relé de Aström.
En [37], presentan controladores óptimos en un intercambiador de calor simulado basados en los criterios de la integral (Ver sección VI) de López [42]. El criterio de desempeño consiste en la minimización de algún criterio integral y la respuesta sólo es óptima para este criterio. El articulo [37] presenta dos tipos de sintonía dependiendo de los objetivos de control: para seguimiento o regulación. Y demuestra mejorar la respuesta transitoria del intercambiador de calor comparado contra un ZN y Cohen-Coon.
En [5] se emplea en un tren de intercambiadores de coraza tubo de cuatro etapas para un proceso de condensado de vapor, dos algoritmos de control no lineal: Generic Model Control - GMC y Process model based control - PMBC [43] para obtener un rango de operación más amplio que el controlador PI clásico (modelo linealizado en el punto de operación) y contrarrestar las no linealidades del proceso. La ley de control se determina mediante un modelo y respuesta de proceso deseada, es decir son controladores basados en modelos: predictivo y adaptativo. Los controladores permiten la sintonización en línea, pudiendo ser posible utilizar los procedimientos heurísticos de un PI clásico. El GMC permite manejar las no linealidades del intercambiador, pero el PMBC compensa alinealidades y tiempos muertos variantes mediante un solo parámetro de sintonía. La dificultad de este algoritmo radica en la sintonía, la cual es considerada un arte, debido a que la especificación del modelo afecta a la ley de control resultante [44].
En cuento a las técnicas de control robusto tenemos el controlador H2 en [13], que garantiza la estabilidad interna del sistema y muestra una respuesta amortiguada y el controlador H∞ [12,13] que garantiza estabilidad y desempeño (sub)óptimo. Ambos controladores garantizan margen de módulo, dinámica de seguimiento rápida y rechazo de ruido dependiendo de las restricciones físicas del sistema. Sin embargo, el controlador H∞ es un controlador de alto orden difícil de implementar y requiere un gran conocimiento del sistema para selección de las funciones de peso. En [45] se presenta dos controladores robustos diseñados por el criterio de frontera de estabilidad y el teorema de pequeña ganancia.
Los controladores inteligentes toman en cuenta la lógica del proceso, optimización, probabilidad, percepción, razonamiento humano, toma de decisiones y aprendizaje; su objetivo es integrar agentes inteligentes en los sistemas de control [46]. En [10] se hace uso de algoritmos genéticos para resolver el problema de optimización de los parámetros del controlador PID para un amplio rango de puntos de operación del intercambiador de calor. En [8] un controlador predictivo basado en modelo de red neuronal es usado para predecir el comportamiento futuro del intercambiador de calor y minimizar un criterio de desempeño. En [7] se realiza la comparación entre un controlador ZN, un controlador difuso lineal y no lineal, mostrando que el difuso no lineal presenta un mejor desempeño de regulación y amortiguamiento de la respuesta del intercambiador. En [47], se compara un controlador difuso convencional contra un PI difuso híbrido en un intercambiador coraza tubo de laboratorio y empleando el software Matlab para implementar el controlador, el controlador híbrido demuestra tener un mejor desempeño evaluado mediante los criterios de IAE e ISE.
VI. ÍNDICES DE EVALUACIÓN DE DESEMPEÑO
Los requerimientos de control de un intercambiador de calor se definen por el proceso, ya que es este el que indica el punto de operación de temperatura, presiones y flujos de entrada. Por lo tanto, no existen índices estandarizados y valores que se consideren únicos para el intercambiador de calor. La evaluación de los lazos de control en la Industrial del Valle en la mayoría de los casos depende de la experiencia del operario y del ingeniero de control, quienes seleccionan los índices de evaluación de desempeño y el rango de valores que se consideran aceptables. El tiempo de estabilización “ts”' y el sobrepaso máximo de la respuesta “Mp”, son los índices de mayor uso en la literatura académica, en su mayoría en simulación del intercambiador 74%; sin embargo, a nivel industrial no se consideran relevante, se encontró que la variación de la temperatura del punto de operación (error) es el índice de evaluación empleado. Las variaciones de flujo y presión indican fallas en el proceso. La mayoría de los índices de evaluación que se encuentran en la literatura sobre lazos de control de temperatura en intercambiadores de calor pertenecen al dominio del tiempo.
Tiempo de establecimiento - ts: tiempo requerido para que la temperatura de salida del producto alcance y permanezca dentro de una banda determinada (δ) alrededor del valor final (usualmente δ = ±5% o ±2% del cambio de la salida). Este índice de desempeño determina la velocidad de respuesta. Es usado en [7,10-12,23,37,48].
Sobrepaso - Mp: máximo valor de temperatura de salida del producto que excede el valor final después de una alteración del sistema. Es un indicador de dinámicas subamortiguadas y/ó presencia de un cero en el semiplano complejo izquierdo. Junto al tiempo de establecimiento es usado en [7,10-12,23,37,48].
En general, el sistema de control del intercambiador de calor busca minimizar el error de la variable de proceso, en función del tiempo transcurrido, después de haberse producido una alteración en el sistema (Cambio de la temperatura de entrada del producto, cambio del flujo del producto). La magnitud del error y el tiempo durante el cual existe, contribuyen a la definición de control óptimo [49]. Los criterios de las integrales se definen por una función de costo (ver Ec. 3), donde F es función del error y el tiempo. El criterio de comportamiento φ será cero solamente si el error es cero durante todo el tiempo, situación imposible en presencia de perturbaciones en el sistema. Por lo tanto, φ no será nulo, pero cuanto más pequeño sea su valor mejor será el comportamiento del sistema.
Los índices de desempeño basado en criterios de integrales “optimas” encontrados en la literatura son: IAE (Integral of the Absolute Value of the error) [8,13,23,45,48,50], este criterio es sensible a pequeños errores, es un indicador de un pobre amortiguamiento del lazo cerrado, la desventaja de este criterio es que su evaluación requiere una gran cantidad de cálculo o simulación del proceso; ISE (Integral of the Square of the error) [8,13,23,45,48,50], es relativamente insensible a pequeños errores, pero los grandes errores contribuyen fuertemente al valor de la integral. ITAE (Integral of the time-Weighted Absolute of the Error) [26,36], es insensible a errores iniciales y penaliza fuertemente los errores que permanecen a lo largo del tiempo, indicador de tiempo de respuesta cortos y sobrepasos; por último, ITSE (Integral of the time-Weighted Square of the error) [23,48].
VII. CONCLUSIONES
El estudio del control del intercambiador de calor no es un tema nuevo en la ingeniería de control, se encuentra que varios autores proponen técnicas de control clásicas, robustas e inteligentes, entre otras; sin embargo, en su mayoría estas técnicas son aplicadas a procesos simulados despreciando las no linealidades ocasionadas por las válvulas, bombas e instrumentación presenten en un proceso industrial real. Un gran aporte a la academia y a ingeniería seria comprobar dichas técnicas de control en plantas industriales o plantas pilotos que impliquen los retos reales de implementación.
A partir de visitas realizadas a empresas en la región del Valle del Cauca se pudo evidenciar que aún se presenta un gran desconocimiento por los técnicos de las empresas en metodologías de sintonía de controladores PID detectándose aun problemas comunes en los controladores PID tales como: alta variabilidad, bajo rendimiento, poca eficiencia en los lazos de control, lo cual muestra que abordar temas de la ingeniería en capacitación y transferencia son requeridos buscando mejorar la competitividad y productividad de las empresas.
De igual forma se pudo determinar que técnicas avanzadas como controladores inteligentes y robustos no son aún usados en la industria, principalmente debido al desconocimiento en la sintonía, implementación y mantenimiento de estos controles por parte de ingeniería y operación. Implementar, validar y documentar los métodos no usados en la industria en plantas reales es otro reto para la ingeniería y la academia de la región del Valle del Cauca.
De acuerdo con el análisis realizado, mejorar el comportamiento en automático de los intercambiadores de calor implican varios componentes fundamentales: conocer el modelo proceso, seleccionar la estrategia más adecuada para dicho modelo, ajustar y sintonizar el algoritmo de control y aplicar criterios de evaluación de desempeño. Como ejemplo, la aplicación de estos componentes al tratamiento térmico llevaría a la obtención de productos inocuos, de mejor calidad y con mayor tiempo de conservación, en el caso de los alimentos.