I. INTRODUCCIÓN
STE artículo describe los esfuerzos realizados para consolidar una innovación en RENAULT-Sofasa en Colombia, a través de un proyecto cuyo objetivo se centra en ofrecer a varios mercados latinoamericanos un nuevo vehículo que integre tecnologías novedosas de conducción, entretenimiento y seguridad a los pasajeros, manteniendo una estética exterior e interior que garantice la calidad percibida por el cliente, a partir del desarrollo de procesos productivos automatizados y eficientes y el desarrollo de capacidades en los proveedores, para el desarrollo de las piezas.
El proceso de ensamble tradicional en RENAULT-Sofasa se transformó al acondicionar nuevos métodos, más complejos y tecnológicamente avanzados para su fabricación, tanto en la planta de ensamble como en la producción de piezas, lo que permitió obtener vehículos de mayor calidad. Fue necesario realizar una transformación de los procesos productivos tanto en el piso de producción de RENAULT-Sofasa en Medellín, como de los proveedores nacionales de piezas, integrando tecnologías que permitieran asegurar la calidad del vehículo ensamblado y su confiabilidad. En los procesos productivos de RENAULT-Sofasa se pudo observar el impacto al integrar a la línea de producción, brazos robóticos industriales de alta precisión para las uniones y soldaduras, así como el diseño y fabricación de herramentales para los procesos de ensamble y ayudas ergonómicas que tuvieron como consecuencia mejoras en la eficiencia de procesos por ejemplo con sistemas automatizados, que en el mediano y largo plazo, permitirán optimizar los procesos de producción para otras referencias de vehículos en planta. De la misma manera, se diseñaron y desarrollaron procesos, herramentales y medios de control para los procesos de fabricación de los proveedores de piezas, proceso realizado en conjunto con el equipo de ingeniería de RENAULT-Sofasa, permitiendo incrementar el conocimiento del ensamblador y los proveedores, generando un avance en el desarrollo de capacidad tecnológica de las empresas participantes.
Teniendo en cuenta que el sector automotor demanda continuamente procesos de generación y uso de conocimiento, caracterizándose por desarrollar productos de media alta complejidad tecnológica, con un nivel de inversión en investigación y desarrollo por parte de las empresas que se encuentra entre el 2 y el 5% de las ventas [1]; el desarrollo de este tipo de proyectos en los países donde se tienen plantas de fabricación o ensamble fortalece las capacidades de la industria automotriz, en mayor escala a nivel local [2], por cuanto genera encadenamientos que promueven el desarrollo y apropiación de conocimiento en áreas de ingeniería en diferentes sectores productivos (metalmecánico, plástico, textil entre otros) y fortalece las capacidades de la ensambladora, y de sus proveedores, incrementando el nivel de competencia del sector en el país, para asignación de nuevos proyectos frente a otras plantas de fabricación en la región.
La propuesta que se describe a continuación en este artículo fue objeto de reconocimiento por parte de MINCIENCIAS, como proyecto de innovación.
II. ESTADO DE LA TÉCNICA
A. Desarrollo de Productos en la Industria Automotriz
La industria automotriz se caracteriza por requerir de tecnologías y procesos especializados ya que un vehículo se compone de una serie de partes interconectadas que requieren la conjunción de varias áreas de la ingeniería. De hecho, este sector ha incrementado su nivel de inversión en investigación y desarrollo, con respecto a otros sectores empresariales, ostentando el segundo lugar en incremento de inversión desde el año 2009, por cuanto, esta industria demanda constantemente de conocimientos que le permitan estar en evolución [1].
En ese contexto, el desarrollo de productos se debe realizar en procesos sistemáticos contenidos en etapas dentro de las que se puede identificar: Planeación, Desarrollo de conceptos, Diseño de sistemas, Diseño de detalle, Pruebas y ajustes [3]. De otra parte, las etapas que incluye el diseño y desarrollo de producto son: diseño de detalle, pruebas y ajustes, que son las etapas previas al lanzamiento del vehículo a producción comercial [3].
En el desarrollo de vehículos automotores, posterior al diseño a nivel de sistema, es necesario realizar pasos simultáneos para el diseño de detalle de los diferentes subsistemas y componentes que los integran, a los cuales se les desarrollan pruebas en procesos paralelos. Este proceso es iterativo, y se realizan cambios en el diseño de los componentes y subsistemas y en los procesos en la medida en que se realizan los análisis de las pruebas individuales [4]. Por tanto, se realizan procesos de integración y pruebas del sistema complejo, que nuevamente son iterativas y solo hasta el cumplimiento de los requerimientos de diseño, de los estándares de prueba y de las normativas requeridas, se obtiene la aprobación para el desarrollo del proceso de producción en serie.
El diseño de los diferentes sistemas del vehículo incluye aspectos como la visión de arquitectura general y la disgregación del vehículo en subsistemas y componentes [3]. Posteriormente, las etapas de diseño de detalle, pruebas y refinamiento se componen de tres flujos de trabajo: diseño, prototipo y producción, como se puede ver en la Fig 1.
El proceso de diseño se realiza en general en software especializado asistido por computador, lo que permite el intercambio entre diferentes equipos de trabajo (al interior de la empresa fabricante o con sus proveedores). Una vez se tienen versiones finales, se publican en etapas con base en requisitos como tiempos de entrega y herramentales y medios de control requeridos para producción. Se libera por etapas, para facilitar información que permita ir elaborando el herramental, con el fin de realizar durante esta fase ajustes menores y pruebas, en lugar de esperar a que el vehículo esté completamente diseñado [3]. Las últimas herramientas desarrolladas, son los dispositivos de fijación que facilitan el montaje de accesorios exteriores como los lados de la carrocería, guardabarros, entre otros [3]. Las piezas y los subsistemas realizan su propio proceso de pruebas y ajustes, hasta su aprobación. Sin embargo, antes de tener componentes y sistemas fabricados con herramientas de producción, se requiere del ensamble de prototipos de vehículos que permita verificar la integración de las piezas en primera instancia.
Los primeros prototipos se fabrican con piezas manufacturadas sin herramentales y por lo general en una instalación de pre-producción para comenzar el proceso de ajuste. Una vez se fabrican los primeros componentes con herramentales, se ensamblan los primeros prototipos de vehículos en la planta de ensamblaje del vehículo, y se realizan varias tandas de prototipos en la medida en que se desarrolla el proceso de validación de la fabricación [3].
La fabricación de herramentales, como se puede ver en la Fig. 1, se encuentra dentro del proceso de diseño, pruebas y ajustes. En este paso, se fabrican los herramentales (troqueles de metal, moldes entre otros) y medios de control. Una vez se tienen herramentales fabricados, se realizan pruebas de fabricación de piezas intentando llegar al 80% de nivel de especificaciones. Posteriormente, se ajustan las herramientas de producción de acuerdo con el nivel de cumplimiento encontrado en las pruebas de fabricación de componentes. En las piezas fabricadas, en esta fase, se les realizan pruebas tanto de funcionalidad como de precisión dimensional [3].
Una vez se han validado herramentales, piezas y prototipos, la planta de ensamblaje comienza a funcionar y se acerca al inicio del proceso de lanzamiento de producción [3].
B. Componentes y procesos de vehículos en procesos de producción
Cuando se diseña y fabrica un automotor, es necesario recordar que cada vehículo puede ser dividido en sistemas funcionales (Ver Tabla I), que varían entre sí dando lugar a variaciones de diseño y por lo tanto de versiones del vehículo [5].
TABLA I DESGLOSE DE VEHÍCULOS POR SISTEMA Y COMPONENTE. ADAPTADO DE [5].
Sistema | Componente |
---|---|
Cuerpo | Bastidor del habitáculo, vigas transversales y laterales, techo. Estructura, estructura frontal, estructura del piso inferior, paneles. |
Tren motriz | Motor, transmisión, sistema de escape, tanque de combustible |
Chasis | Chasis, suspensión, llantas, ruedas, dirección, frenos. |
Interior | Asientos, tablero de instrumentos, aislamiento, tapicería, airbags |
Cierres | Puertas delanteras y traseras, capó y puerta de cofre. |
Misceláneo | Electricidad, iluminación, térmica, ventanas, acristalamiento. |
En la industria manufacturera, particularmente la relacionada con la producción en masa, se buscan mecanismos de reducción tanto de tiempo como de costos de producción, ya que de esto depende la competitividad del negocio. Por esta causa, cada decisión asociada con el diseño que llegue a impactar el proceso de manufactura debe ser evaluada con el fin de asegurar el resultado de la fabricación y reducir la variación en la manufactura de los productos [6].
Lee et al (1996) desarrollaron el concepto de características clave de producto, que incluyen tanto las características de diseño del producto, como los parámetros de los procesos requeridos para su manufactura y ensamble, que impactan la forma, la función y el desempeño de un producto de manera significativa [7]. Al realizar el diseño de un producto, las modificaciones geométricas que se realicen sobre el mismo generarán variaciones en diferentes partes del proceso, impactando los pasos de producción, como se puede ver en el esquema de la Fig. 2.
Existen varias aproximaciones para el diseño de productos de manufactura de ensamble como el definido por Boothroyd-Dewhurst el cual es aplicado en desarrollos diversos en la industria de ensamblaje el cual contempla desde los procesos de diseño hasta el prototipado y producción [9]. Un caso de la aplicación de este tipo de desarrollo se presenta en un caso desarrollado para un vehículo-chasis de tracción humana en la Universidad de Córdoba de la ciudad de Montería en Colombia [10].
Calidad. Teniendo en cuenta que este concepto tiene muchas definiciones, si se toma una aproximación desde el punto de vista de la manufactura, la calidad corresponde al “cumplimiento de requisitos”, mientras desde el punto de vista del usuario, este concepto representa una visión idiosincrática y altamente subjetiva del producto o servicio.
Calidad percibida . Los retos del sector automotor se incrementan debido a los altos niveles de competencia asociados al desarrollo y aplicación de conocimiento, así como en la necesidad de optimizar costos al tiempo que se satisfacen las necesidades de los clientes. Por ejemplo, para tener ventajas competitivas en el segmento premium, que tiene un número limitado de actores, se ha identificado la necesidad de entender la calidad percibida por el cliente [9] en términos de evaluación de los atributos del producto. En la industria automotriz, la calidad percibida del segmento Premium se convierte en un impulsor de la competitividad de cada empresa [11].
Una definición de calidad percibida asociada a la definición de Calidad percibida basada en el valor (VPQ) y a la Calidad Técnica Percibida (TPQ) [11], como se puede ver en la Fig. 3. La primera, reúne los conceptos de TPQ y la experiencia del usuario, a través de sus sentidos y conocimiento. La segunda (TPQ), corresponde a una aproximación desde el punto de vista de ingeniería, que, basándose en el nivel individual de aspectos técnicos del producto, busca cumplir con los requerimientos técnicos y de competitividad [11].
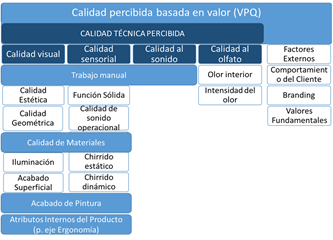
Fig. 3 Marco Conceptual de la calidad percibida con base en valores de la industria automotriz. Fuente: Adaptado de [9].
En estudios de la calidad percibida por el cliente, es fundamental medir y evaluar qué tan importantes son los atributos al momento de la elección del producto a adquirir, que sigue siendo un proceso subjetivo [11], lo que genera la necesidad de que diseñadores e ingenieros que participan en estos procesos, confíen en sus experiencias previas, para tomar las decisiones con respecto a requerimientos y atributos.
En otra investigación sobre calidad percibida, se identificó que es una propiedad, que debe incorporarse desde las etapas de diseño en el desarrollo de producto, teniendo en cuenta su ciclo de vida [6]. Por esta causa, se hace necesario vincular la fabricación y calidad percibida como un factor de excelencia desde las primeras fases del diseño. Se ha podido establecer que esta práctica puede ser determinante en el éxito de los lanzamientos en la industria automotriz y concretamente en el segmento de vehículos de lujo [6].
Para incrementar la calidad visual, con el fin de mejorar la calidad percibida, es necesario tener en cuenta, que cada factor en el proceso de fabricación de un producto puede afectar la calidad percibida frente al cliente. En un vehículo, tanto el proceso de fabricación de las piezas como el proceso de fabricación de subensambles y finalmente el ensamble del producto final, generan las características que el usuario final busca [12].
C. Procesos de ensamble de vehículos
El proceso de manufactura de un vehículo automotor inicia con el conformado de los paneles del cuerpo del vehículo, realizados por lo general en prensas (hidráulicas y mecánicas) y usando matrices de estampación. Posteriormente, una planta ensambladora de vehículos las partes estampadas se unen para formar la cabina, que corresponde a la estructura del vehículo, a través de procesos de soldadura. La cabina ensamblada pasa a un proceso de lavado, pintado (primer, base y pintura) y horneado, para posteriormente iniciar el proceso de instalación del trim en el auto [13]. En las operaciones, correspondientes a la instalación de trim, hay una alta dependencia del recurso humano, por cuanto tiene requerimientos de procesos no automatizados [13].
Los procesos de ensamble actuales requieren sistemas de manufactura con lead time cortos, menor número de procesos y de operaciones de manufactura, así como altos niveles de eficiencia para fabricar un vehículo completo. Una vez se ha desarrollado el vehículo, es necesario el incremento de niveles de estandarización de la producción, así como disminución de re-trabajos y desperdicios [13].
Cuerpo del Vehículo . Es uno de los sistemas más complejos del vehículo, debido a la necesidad de coordinación que demanda de diversos grupos de personas (dentro de la empresa ensambladora y en los proveedores de partes), los cuales realizan interacciones desde el diseño del producto, el diseño tanto de piezas como de herramentales y materias primas [14].
El desarrollo de esta parte del automóvil requiere procesos de fabricación con mayores costos, asociados con cambios de producto, por cuanto la transformación en la estructura de un vehículo es determinante en la satisfacción del usuario final, y se ha identificado que la apariencia de un automóvil determina también el deseo de compra [14], situación que demanda inversiones superiores a las que requieren otros procesos de fabricación.
Soldadura de Punto Automatizada. Una de las tecnologías de mayor predominancia en la unión de chapa metálica para la fabricación de vehículos automotores es el proceso de soldadura. Esto se debe a que la calidad de los puntos soldados se convierte en un factor determinante cuando se evalúa la funcionalidad del vehículo en términos por ejemplo de rigidez y comportamiento frente a los choques [6].
La aplicación de soldadura de punto automatizada tiene acogida en el sector de manufactura automotriz, donde es usada para soldar las hojas de metal que van a integrar principalmente el cuerpo del vehículo. Al implementar este tipo de tecnología se reducen tanto los dispositivos requeridos (lo que permite manejar restricciones de accesibilidad ocasionadas por su uso), como el tiempo de ciclo; adicionalmente, automatizar procesos de soldadura de punto, facilita el desarrollo de productos finales con mejor calidad, mientras se disminuyen los impactos en la salud y los riesgos profesionales de los operarios del área [15].
La implementación de procesos de Soldadura Automática presenta ventajas como las siguientes [15]:
− Siendo robots antropomórficos tienen la facilidad de realizar soldaduras en puntos difíciles de alcanzar para los operarios.
− Debido a la posibilidad de programación, los robots de soldadura pueden realizar tareas repetitivas en producción (producción por lotes) con información adecuada del programa asociado a cada modelo de pieza que debe manufacturar.
En el sector automotor la robotización del proceso de soldadura, en la fabricación de partes donde inicialmente se realizaba por completo con intervención humana, requiere de un diseño de procesos que permitan que el vehículo o carrocerías a ser procesadas sean trasladados secuencialmente por la línea de producción donde robots realizan tareas particulares, para agilizar y asegurar la ubicación de los puntos de soldadura. Los robots de soldadura actualmente tienen capacidades de carga (entre 50-100 Kg), y 5 o 6 grados de libertad en su estructura, lo que permite posicionar bien sea la pinza o las partes del vehículo, logrando acceder a lugares donde un operario humano no lograría llegar [16].
Adicionalmente, la adaptación de las diferentes funcionalidades de las células robotizadas y cada proceso de reprogramación puede representar un desafío en términos de conocimiento y de dependencia por parte de la empresa que los adquiere. Por lo tanto, es necesario contar con profesionales con nivel de capacitación adecuado para poder realizar los cambios en programación que requiera el equipo, de acuerdo con los productos que se deban desarrollar [17].
Grafado. Este proceso es un método que se utiliza para unir dos láminas de metal; sin embargo, se considera un proceso de conformado, específicamente de doblado de metales [18]. Al usarlo para ensamblar partes, ofrece una ventaja al generar uniones compactas, aunque no tan fuertes como la soldadura de punto. Para incrementar la resistencia de las uniones con este proceso, es posible utilizarlo en combinación con métodos como unión adhesiva [19]. Se han identificado una serie de pasos comunes en los procesos de grafado: Primero el reborde del panel exterior se dobla (ángulo aproximado 45°). Posteriormente, se realiza el doblado a la posición final [19], y se realiza la unión (doblez) de un panel externo con un panel interno.
En la fabricación de automóviles, se usa este proceso en la elaboración de las puertas de un vehículo, las cuales están compuestas de dos partes: un refuerzo y la parte exterior (o piel del vehículo). Estas piezas son pegadas y unidas a través de grafado, en tres pasos: rebordeado, pregrafado y grafado, como puede verse en la Fig 4. [20].
Existen dos alternativas para realizar este proceso:
Proceso Clásico. Se utilizan prensas y dados (con formas geometrías de considerable grado de complicación) para la fabricación de las piezas. En este caso, se rebordea utilizando un set de dados, haciendo un doblez (ángulo aproximado 90°). Posteriormente, para el pre-grafado, se dobla el borde en un ángulo agudo (de 45° o inferior), usando un set diferente de dados específicos. Para finalizar, se realiza el grafado terminando el doblado del material, usando un set de dados diferente [18].
Proceso Automatizado. Es realizado por un robot, con un herramental en forma de rodillo. El rodillo se desliza a lo largo de la línea de los rebordeados requeridos, realizando un proceso de doblado progresivo en la medida en que el herramental lo permita.
El proceso automatizado presenta menor tiempo de entrega con respecto al proceso clásico, menor costo y menor cantidad de herramental requerido, por cuanto se puede usar una misma herramienta desde el prototipo hasta la vida serie del producto [20]. También se ha identificado que, aunque son procesos automatizados, son adecuados para fabricar piezas a baja escala [12], facilitan el control de medidas y tolerancias y generan una mejor calidad de superficie [21].
III. DESARROLLO
Desarrollar productos en el sector automotor demanda que los equipos de ingeniería del ensamblador establezcan especificaciones del concepto general del nuevo modelo, el cual debe ser aprobado, para posteriormente generar un plan de detalle que comprenda requerimientos como dimensiones y material para cada parte. Esta información servirá de punto de partida para la elaboración de planos de ingeniería de detalle para cada pieza [22].
La interacción entre la empresa ensambladora y cada proveedor de piezas originales, partiendo del diseño de detalle elaborado, cubre los siguientes pasos [22], que obedecieron al proceso metodológico del desarrollo del nuevo vehículo.
− El ensamblador entrega un set de requerimientos de producción para un número de productos a desarrollar [23].
− Cada proveedor inicia el proceso de fabricación de piezas con procesos iterativos de diseño de piezas, fabricación y pruebas de prototipos tanto por el proveedor, como por el ensamblador, con el fin de realizar ajustes en el diseño [24].
− El ensamblador identifica y formula cambios necesarios en cada pieza, a partir de los procesos de validación realizados, que impactarán los procesos internos del ensamblador y los del proveedor.
− El proveedor modifica los diseños de las piezas y ajusta procesos de fabricación, con el fin de entregar las piezas de acuerdo con los requerimientos del producto final.
− Una vez realizados los cambios y verificadas las variables de los productos, el ensamblador aprueba el inicio de la producción en volumen.
− El proveedor entrega el producto terminado.
A. Desarrollos de piezas y medios con Proveedores Locales
El ensamble de nuevo vehículo genera la necesidad de desarrollar nuevas piezas con los proveedores de autopartes. A nivel local, a partir de las necesidades de cada mercado se identifican segmentos de clientes y se adaptan modelos; el lanzamiento de nuevas versiones de automóviles, con incorporación de tecnologías desarrolladas para vehículos de alta gama, hace necesario la transformación de mejoras en la apariencia en el cuerpo del vehículo [22].
En el caso del proyecto que dio lugar al presente artículo, se requirió el desarrollo de 145 referencias. En cada caso, de acuerdo con las metodologías de diseño del proveedor y las compartidas por RENAULT-Sofasa en otros proyectos, cada proveedor debió diseñar, desarrollar y fabricar tanto los herramentales, como los medios de control, a ser usados de manera exclusiva en la fabricación de las piezas del nuevo vehículo. Tanto los herramentales como los medios de control fueron usados en diferentes fases: desde la fabricación de piezas prototipo, durante los procesos de validación de las mismas, hasta llegar a las piezas integradas en los vehículos comercializables.
Entre los grupos de piezas locales, desarrolladas para la plataforma del vehículo, se incluyeron piezas de los sistemas tren motriz, chasis y climatización. Lograr desde el punto de vista técnico las mejoras requeridas en el proceso fabricación y ensamble de las piezas y el vehículo tuvo repercusiones importantes en las necesidades de transformación de los procesos de manufactura, para lograr los niveles de calidad especificados.
Una breve descripción de las transformaciones requeridas por los proveedores en sus procesos, se relacionan en la tabla II.
TABLA II CAMBIOS EN LOS PROCESOS DE LOS PROVEEDORES.
Piezas por Sistema | Descripción general de cambios en los procesos |
---|---|
Piezas de Chasis | Desarrollar o adquirir dispositivos, herramientas o máquinas para verificar el impacto de los subensambles elaborados, en condiciones de fuga, nivel de fijación de las piezas en el ensamble y condiciones geométricas |
Diseño y desarrollo de moldes. | |
Piezas de Tren Motriz | Diseño y fabricación de moldes, rediseño de procesos, diseño de nuevos herramentales y nuevos medios de control. |
Piezas para climatización | Diseño y fabricación de herramentales. |
El proceso de fabricación implicó el desarrollo de piezas prototipo y de una serie de pruebas para validar el cumplimiento de su funcionalidad, antes y durante las pruebas en los prototipos que se ensamblaron de los vehículos.
B. Mejoras significativas requeridas en los procesos de la planta de ensamble RENAULT-Sofasa
Con el ensamble del nuevo vehículo se buscaba mejorar las características asociadas con la calidad percibida por parte del cliente en aspectos estéticos (visuales), al tocar el vehículo (tacto) y de acústica en el habitáculo, con el fin de impactar en aspectos que actualmente son relevantes principalmente en vehículos de alta gama. Se busca reducir los juegos o los afloramientos entre las diferentes piezas que componen la carrocería, para mejorar la imagen del vehículo, con respecto a otros vehículos del mismo segmento, generando la necesidad de implementar cambios en los procesos productivos tanto de la planta ensambladora, como en los proveedores de piezas.
Adicionalmente, la Plataforma del nuevo vehículo fue reforzada con el objetivo de integrar las nuevas motorizaciones, la dirección asistida eléctrica y de mejorar la seguridad pasiva del vehículo.
A partir de las condiciones de diseño de las piezas, se realizó un análisis de los procesos de la planta ensambladora, para la cual se identificaron los requisitos de los procesos internos.
Soldadura. La fabricación de la cabina del nuevo vehículo hizo necesario un proceso de automatización que incluyó implementación y adaptación de robots para el área de soldadura, que permitieran garantizar las condiciones geométricas del diseño, así como aspectos de calidad percibida y aspectos de seguridad del vehículo.
El rediseño del proceso tuvo en cuenta las condiciones críticas de una planta multimodelo, de media/baja cadencia, buscando la disminución de costos de implementación de procesos robóticos, partiendo del análisis de los tipos de dispositivos requeridos, para lo cual se estableció una estrategia de implementación y operación que permitiera optimizar el uso de dispositivos convencionales. El diseño del proceso que se estableció para hacer posible durante la operación se lista a continuación.
− Medios de fabricación que aseguren los niveles de calidad percibida requerida para el nuevo vehículo.
− Realizar un mayor número de puntos de soldadura.
− Se diseñaron herramentales y matrices que permitieran optimizar el uso de la célula robotizada para el nuevo modelo y los modelos existentes, validando las matrices a través de pruebas del herramental y pruebas en producción de piezas prototipo, que permitieran el proceso de soldadura y para garantizar las condiciones geométricas del vehículo.
− Realizar la programación de los brazos robóticos para aplicación de soldadura, garantizando un control total sobre cantidad y calidad de puntos aplicados.
En el proceso de implementación, se instalaron los sistemas, equipos especializados, se realizaron pruebas de funcionamiento, antes de la instalación de los herramentales, trabajando en paralelo, para mantener la fabricación de los vehículos, mientras se completan los diferentes aspectos del diseño en el área del nuevo proceso.
Para el nuevo vehículo, se adquirieron tres estaciones robotizadas con 17 robots con el objetivo de mejorar la productividad y calidad percibida del nuevo vehículo, una isla de sertissage con tres robots ABB de origen francés con 6 grados de libertad, una capacidad de carga de 235 kg y un alcance máximo de 2,65 m, una isla para el ensamble del compartimento motor con tres robots de soldadura y un robot de manipulación y aplicación de mastic FANUC de origen Japones con 6 grados de libertad, una capacidad de carga de 210 kg para los de soldadura y 280 kg para manipulación y un alcance máximo de 2,655 m para los de soldadura y 3,103 m para manipulación, y una última isla para el ensamble general de la cabina con 6 robots de soldadura FANUC con posibilidad de hacer cambios y uso de hasta 10 tipos de pinzas de soldadura diferentes; 4 robots de manipulación FANUC con intercambiadores de grippers para poder ensamblar los tres modelos de vehículo que pasan por esa estación, con una capacidad de carga de 210 kg para los de soldadura y 400 kg y 700kg para manipulación y un alcance máximo de 2,655 m para los de soldadura y 3,704 m y 2,832 para manipulación. Cada una de las islas cuenta con sus respectivos módulos de control y potencia. El proceso de soldadura diseñado e implementado puede verse en la Fig. 5.
Para validar la implementación, se realizaron pruebas de ciclo de trabajo en los sistemas diseñados, y simulación de movimientos. Algunos ejemplos de los tipos y variables de pruebas realizadas se encuentran en la Tabla III. Adicionalmente, se evaluaron variables específicas, de acuerdo con los requerimientos tanto del proceso, como del diseño del nuevo vehículo.
TABLA III PRUEBAS REQUERIDAS PARA LA VALIDACIÓN DE LOS PROCESOS Y PIEZAS DE SOLDADURA
Pruebas | Variables |
---|---|
Pruebas de ciclo de trabajo | Tiempos de ejecución |
Variables asociadas a la calidad de los procesos | |
Pruebas a las piezas: Calidad de los puntos de soldadura | Fuerza de apriete de láminas, corriente programada vs. aplicada, tamaño del botón de soldadura, entre otros. |
Pruebas a los medios: Repetibilidad de los medios de fabricación | Se mide la capacidad de los medios de fabricar piezas con las mismas dimensiones |
Pruebas a las piezas: Calidad dimensional | Verificación de zonas y sistemas de seguridad, validación de las condiciones de movimientos manuales y automáticos |
Otros Procesos. De acuerdo con la necesidad de ajustes y cambios ocasionados por los diseños de los nuevos vehículos se rediseñaron o diseñaron procesos de fabricación.
Se diseñaron matrices para la fabricación de piezas a través del proceso de Grafado. Adicionalmente, se rediseñaron las cabinas para el proceso de pintura de piezas plásticas, implementando adicionalmente un proceso de limpieza con robot de flameado para piezas plásticas.
Con respecto a los procesos realizados en el área de montaje se diseñaron e implementaron ayudas ergonómicas en diferentes puestos de trabajo, para facilitar el levantamiento de piezas y su ubicación al interior del vehículo, con el fin de cumplir con las condiciones de diseño, eliminando riesgos laborales para los operarios.
Los cambios en los procesos asociados con la cabina como Grafado, así como en procesos de la zona de armado, generaron la necesidad de realizar pruebas de validación, tal como se puede ver en la tabla IV.
TABLA IV CAMBIOS GENERADOS POR EL NUEVO VEHÍCULO EN DIFERENTES PROCESOS DE LA ENSAMBLADORA.
Pruebas | Variables | Objetivo |
---|---|---|
Grafado (sertisaje) | Diseño y Fabricación de matrices para ensamble de partes (por ejemplo, puertas de vehículo) | Asegurar la calidad percibida |
Variables asociadas a la calidad de los procesos | ||
Prueba de Piezas | Fuerza de apriete de láminas, corriente programada vs aplicada, tamaño del botón de soldadura, entre otros. | Asegurar condiciones geométricas |
Pruebas de Piezas | Verificación de zonas y sistemas de seguridad, validación de las condiciones de movimientos manuales y automáticos | Asegurar la Calidad dimensional |
Pruebas de herramental y asistencias ergonómicas | Funcionamiento en vacío | Validar condiciones de uso |
Habilidades y capacidades del personal. Cada fase del proceso demandó formación de las competencias y habilidades para la integración del vehículo. Por ello, se realizó una selección de operarios senior de la planta de producción (de áreas como Soldadura, Pintura, Ensamble y Montaje), quienes recibieron formación en los diferentes procesos que fueron transformados a partir del desarrollo del nuevo vehículo, con el fin de garantizar la cadencia de la línea, siendo estos operarios los encargados de formar a los demás colaboradores de planta en los procesos que requiere el nuevo vehículo. Por ejemplo, en el área de soldadura, el personal operativo y de mantenimiento, recibió formación en programación y automatización, así como en el diagnóstico y modificación de los robots, con el fin de garantizar la apropiación de la tecnología instalada e incrementar sus competencias.
IV. RESULTADOS
Los resultados que se obtuvieron a raíz del desarrollo del nuevo vehículo se presentan con respecto a los impactos en el desarrollo de piezas locales, y por otro lado, en el desarrollo en la ensambladora.
A. Resultados asociados al desarrollo de piezas locales.
Se realizó el diseño y la fabricación de los herramentales y medios de control de los proveedores de partes automotrices. El desarrollo de los herramentales implicó la participación en procesos de transferencia tecnológica, en los cuales:
Se realizaron misiones en las que participaron integrantes del equipo de ingeniería de RENAULT-Sofasa y de los proveedores locales de piezas
Durante las misiones, los equipos internacionales brindaron asistencia técnica a los fabricantes de los herramentales locales, incrementando las capacidades de desarrollo de producto de los participantes (tanto personal de RENAULT-Sofasa, como en los proveedores).
En el caso de las piezas, se realizaron misiones de referenciación y trabajo conjunto con equipos de Rumania y Brasil. Para validar la calidad de las piezas, se realizaron pruebas de durabilidad que permitieran analizar su comportamiento bajo condiciones de uso. Algunas de las piezas desarrolladas, pueden verse en la Fig. 6.
Las piezas desarrolladas y los procesos productivos transformados fueron validados a través la realización de pruebas (Ver ejemplo en la Tabla V), que permitieran establecer el cumplimiento de los requerimientos de diseño y de las variables establecidas para cada pieza fabricada, según el diseño del producto.
TABLA V PRUEBAS REALIZADAS A LAS PIEZAS DEL NUEVO VEHÍCULO PARA VALIDACIÓN DE PIEZAS Y PROCESOS DE LOS PROVEEDORES DE PARTES.
Pruebas | Variables | Objetivo |
---|---|---|
Ensamble De Elemento Turnante Y Tren Trasero | Máquina de Estanqueidad para verificación de fugas - Herramientas de Torque - Herramientas Geométricas Test de serie, al 100% de los vehículos |
Garantizar ausencia de fuga de aire en las líneas instaladas. |
Rines | Pruebas de corrosión, rayado, desprendimiento de pintura y ensayo de impacto | Validar ausencia de daño en la llanta en caso de un impacto lateral. |
Tubos Flexibles De Combustible | Pruebas de vibración Pruebas de tracción |
Garantizar resistencia a la presión, a la temperatura y a la vibración. |
Tren Metálico y Cuna | Banco de Simulación | Garantizar la resistencia de ambos componentes a un x número de ciclos, sin perder la función (sin romperse). |
Tuberías De Escape | Pruebas de resistencia de la soldadura | Evitar la ruptura de la línea de escape o de alguno de sus componentes |
Se realizaron validaciones geométricas para determinar la posición real vs la posición teórica de los planos, a partir de un número determinado de piezas según la fase del proceso de desarrollo. Las diferentes referencias se sometieron a pruebas, y se midieron los puntos de control de la pieza. Cada no conformidad generó ajustes en herramentales, procesos y en algunos casos, en las mismas piezas. Finalmente, se validó la estabilidad estadística de cada cota crítica de las piezas que entrarían en fabricación en serie, para confirmar la estabilidad del proceso de producción de los vehículos a fabricar.
De acuerdo con los requerimientos de diseño y de funcionalidad de cada pieza, se realizaron adicionalmente pruebas dimensionales, de calidad, llegando a realizar 1822 validaciones específicas según la naturaleza de la pieza, que permitieran validar el desempeño de las mismas.
En el caso de los procesos productivos diseñados e implementados para la fabricación de piezas y herramentales, se realizaron procesos de auditoría, evaluando en cada proveedor los procesos de producción (con herramentales, procedimientos, materiales y personal definitivos), con el fin de identificar oportunidades de mejora y ajustes requeridos; se realizaron los ajustes dejando los procesos conforme a las necesidades del vehículo, asegurando que cada proveedor pueda entregar piezas conformes (con los requerimientos del producto), de manera oportuna (en tiempos de ciclo) y con cadencias representativas de la serie del vehículo.
Una vez superadas las pruebas para cada pieza, el inicio del proceso de fabricación fue aprobado por RENAULT-Sofasa.
B. Resultados de la implementación en la ensambladora
Los diferentes procesos de planta de ensamble fueron diseñados, instalados, puestos a punto, entregando a los procesos de producción con la calidad esperada.
Algunos de los impactos generados en la planta, por el desarrollo de estos cambios, se pueden ver en la Tabla VI.
TABLA VI IMPACTOS GENERADOS EN PLANTA DE PRODUCCIÓN EN RENAULT-SOFASA.
Procesos | Modificación | Verificación | Impacto |
---|---|---|---|
Soldadura | Diseño de proceso e Instalación de Robots y matrices de soldadura (específicas y comunes) | Puesta a punto en el proceso productivo y Verificación de la performance. | Cumplimiento de los objetivos de calidad y los indicadores de desempeño industrial |
Evaluación de las piezas (Ver tabla III). | Cumplimiento de los requerimientos de variables técnicas | ||
Se realizó el proceso de formación del personal para el manejo de los nuevos procesos | Validación dentro del mismo proceso de formación. Validación a través de las pruebas de calidad en cada pieza fabricada. |
Consolidación de capacidades de personal en procesos de programación básica y avanzada y automatización requeridas para soldadura y grafado. | |
Montaje | Diseñadas e instaladas 6 ayudas ergonómicas en áreas como montaje de motor, de llantas, entre otras. | Se realizaron pruebas de fiabilidad y capacidad para cada área con nuevas ayudas ergonómicas instaladas. | Facilitando el manejo de piezas y eliminando el riesgo de peso para montaje en el vehículo, se disminuyó la posibilidad de enfermedades profesionales. |
Grafado | 3 matrices robóticas entregadas al proceso para su implementación | Puesta a punto. Validación a través de Pruebas de Calidad dimensional |
Cumplimiento de los objetivos de calidad y los indicadores de desempeño industrial. |
Se realizó la homologación de los vehículos de acuerdo con las condiciones requeridas para la normativa de los diferentes mercados objetivo. Finalizó el proceso de formación de los operarios que entrarían a realizar la fabricación del vehículo.
Se logró el desarrollo del vehículo de acuerdo con las condiciones de diseño, generando las mejoras requeridas para lograr los aspectos de calidad permitida. Sin embargo, el proceso de reconocimiento de estas mejoras por parte del usuario final, sólo se pueden probar, en definitiva, al iniciar los procesos de comercialización.
V. CONCLUSIONES
El proyecto permitió la preparación tecnológica de RENAULT-Sofasa para transformar sus procesos de ensamble con elementos sustentados en la robótica y la automatización que eran necesarios incorporar para la fabricación de un nuevo vehículo. Esta transformación se extendió a los proveedores que al incorporar nuevas tecnologías aumentaron su capacidad y ofrecen productos más complejos y de mejores condiciones de calidad percibida.
Se realizaron procesos de transferencia de tecnología hacia los proveedores de piezas desde diferentes fuentes, en los que participó el personal de ingeniería de RENAULT-Sofasa. La realización de estos procesos permitió garantizar las habilidades técnicas que fueron posteriormente aplicadas en los procesos de fabricación de piezas y posteriormente del ensamble de las mismas para el nuevo producto, mejorando las capacidades de ingeniería y la posibilidad de difundir dicho conocimiento a proveedores externos de RENAULT-Sofasa.
Se observó la adquisición de conocimientos técnicos que pudieron ser aplicados directamente a procesos de ensamble, detalladamente diseñados para el nuevo producto, lo que aumentó las capacidades de ingeniería y la posibilidad de difundir dicho conocimiento a proveedores externos de RENAULT-Sofasa.
Se desarrolló un plan de validación y homologación de las piezas y los vehículos; este plan se menciona de manera sintética en este documento, a través de ejemplos como los suministrados en las Tablas III, IV, V y VI. Sin embargo, debido a la dimensión del proyecto, la cantidad de variables y pruebas evaluadas por pieza y en los vehículos, fueron desarrollados con el rigor correspondiente a un proceso de I+D+i de la industria automotriz. El logro de los procesos de homologación y validación a través de las pruebas, en laboratorios externos a las compañías y en laboratorios internos certificados, permitieron lograr el objetivo de garantizar la correcta fabricación de los mismos, así como el cumplimiento de las normativas técnicas requeridas para su comercialización en diferentes mercados.
TABLA VII RESUMEN DE LOS LOGROS GENERADOS EN PLANTA DE PRODUCCIÓN EN RENAULT-SOFASA.
Áreas de Producción | Resumen |
---|---|
Diseño e Implementación de Lay Out para el nuevo proceso de soldadura | Evaluación del flujo de piezas, ajustes y optimización |
Implementación de Procesos Automatizados (Soldadura y Grafado) | Diseño y fabricación de matrices Instalación y puesta a punto de robots Validación de piezas fabricadas Fortalecimiento de las capacidades de producción con las nuevas tecnologías al desarrollar. Procesos de formación especializados, para los operarios que intervienen en el mismo. |
Procesos de Montaje | Diseño, fabricación e implementación de ayudas ergonómicas, eliminando problemas de salud ocupacional, ocasionados, por ejemplo, por manejo de elementos pesados. |
Se lograron los niveles de calidad en los procesos intervenidos de la planta de ensamble. La implementación de los procesos automatizados mejoró los niveles de performance, con respecto a los procesos previos, logrando los niveles de producción esperados. Se cumplieron los estándares que permitieron el avance en cada fase del proyecto y durante la ejecución del mismo, finalizó el proceso de formación de operarios tanto en las nuevas tecnologías, como en los cambios de procesos requeridos para el nuevo vehículo.
En el desarrollo de nuevos productos, concretamente en el sector automotor, se presentan retos técnicos asociados con la aplicación de tecnología que permita hacer realidad las expectativas de los clientes finales y mejorar la eficiencia de los procesos productivos. Se generan cambios en atributos de diseño, que ocasionan el diseño de nuevos herramentales y procesos de manufactura, transformando la operación de las plantas. Sin embargo, para el caso del proceso descrito en el presente artículo, la aceptación de los atributos de calidad percibida de los vehículos desarrollados para el mercado latinoamericano, desde el punto de vista del usuario final, sólo es posible evaluarla una vez los vehículos se encuentran en fase de comercialización.
Por tanto, el presente artículo aporta al conocimiento de la capacidad en ingeniería automotriz colombiana que se alinea con los desarrollos internacionales y exigencias de los nuevos mercados, formando proveedores capaces de nuevas exigencias y de ingenieros que aportan en el desarrollo de líneas de ensamble con altos niveles de automatización y complejidad. Se requiere continuar con la ejecución de investigaciones y aplicaciones que permiten el constante desarrollo de capacidades de la industria nacional.