Services on Demand
Journal
Article
Indicators
-
Cited by SciELO
-
Access statistics
Related links
-
Cited by Google
-
Similars in SciELO
-
Similars in Google
Share
Ingeniería e Investigación
Print version ISSN 0120-5609
Ing. Investig. vol.25 no.3 Bogotá Sep./Dec. 2005
Claudia Marcela Sánchez R.,1 Carlos Julio Cortés R.2
1 Ingeniera mecánica, Universidad Nacional de Colombia - Bogotá, Colciencias, Programa Nacional de Desarrollo Tecnológico, e-mail: cmsanchezr@unal.edu.co, cmsanchez@gmail.com
2 Ingeniero mecánico, MSc. Materiales y procesos de manufactura, Comisión de Estudios de Doctorado en Manufactura, profesos asociado Dpto. de Ing. Mecánica y Mecatrónica, Universidad Nacional de Colombia - Bogotá, e-mail: cjcortesr@unal.edu.co
RESUMEN
Una de las metodologías utilizadas por la ingeniería concurrente o diseño integrado de productos es el diseño para manufactura, DFM. Esta técnica, que está orientada a mejorar la fabricación de piezas analizando geometrías, valores y tolerancias, es utilizada en las primeras etapas de diseño para disminuir los costos de los elementos a fabricar.
Se estudió el diseño para manufactura estableciendo reglas de diseño a fin de elaborar una metodología para diseño en microfundición.
Palabras clave: diseño para manufactura, microfundición (fundición de precisión).
ABSTRACT
Integrated Product Design uses several methodologies, Design for Manufacturing is one of them. DFM pretends to facilitate manufacturing of parts by means of analysis of geometries, values and tolerances, and is used in first design stages in order to decrease the product cost.
The design for manufacturing was studied as well as design rules to propose a methodology for Design for Investment Casting.
Keywords: design for manufacturing, lost wax process (investment casting).
Recibido: junio 15 de 2005
Aceptado: octubre 14 de 2005
Introducción
El diseño y desarrollo de productos requiere no solamente el manejo de conceptos básicos de diseño mecánico convencional, sino la selección adecuada de materiales y procesos de fabricación que permitan obtener artículos que cumplan con los requerimientos funcionales, siendo de alta calidad y con la posibilidad de adquirirse a bajos costos. Por esta causa, es fundamental además de trabajar en equipos multidisciplinarios que involucren en el proceso de diseño tanto los atributos del cliente como las variables de ingeniería y de proceso necesarias para la generación de ideas, implementar técnicas que faciliten el trabajo en equipo y orienten a los diseñadores a obtener los mejores productos desde las fases iniciales de su desarrollo. Diseño para manufactura y ensamble (Design For Manufacturing and Assembly - DFMA) es una metodología usada como parte del diseño y desarrollo integrado de productos y procesos (IPPD), que a partir de reglas y principios, orientan al equipo de diseño a generar conceptos de piezas que sean fáciles de fabricar, tengan una manufactura económica manteniendo su calidad, y al mismo tiempo sean fáciles de ensamblar.
La fundición de precisión es un proceso de copiado de forma que permite la manufactura de piezas con geometrías intrincadas con casi cualquier aleación, incluyendo las utilizadas en la manufactura de artículos aeronáuticos. Por su utilización en la producción, gran variedad de artículos en la industria moderna es utilizada cada vez más, ya que permite adicionalmente un buen costo para lotes medianos e inclusive pequeños del artículo a elaborar.
Partiendo del conocimiento de los aspectos anteriormente mencionados, se vio la necesidad de elaborar un trabajo en la cual, a partir de un diseño conceptual, se pudieran aplicar los conceptos de diseño para manufactura (DFM) teniendo en cuenta los requerimientos de los productos en cuanto a funcionalidad, materiales y facilidad para manufactura, implementados en la ingeniería concurrente. En este artículo se consigna parte del estudio realizado, particularmente los conceptos de DFM aplicados a productos microfundidos. Se estudiaron los conceptos de DFMA y se estableció la base conceptual de los principios centrales de diseño para manufactura (DFM). Posteriormente, por medio de reglas de diseño basadas en el conocimiento de las restricciones y capacidades del proceso, se desplegó la metodología necesaria para la implementación del DFM en microfundición (Design For Investment Casting - DFIC).
Objetivo
Establecer una base conceptual de los principios centrales de diseño para manufactura (DFM), y desplegar la metodología necesaria para su implementación, orientada al proceso de fundición a la cera perdida.
Proceso de Microfundición
Una vez identificados los materiales, se estudió el proceso de microfundición y se establecieron sus limitaciones.
Este proceso es uno de los más antiguos de las técnicas metalúrgicas. Aunque hoy es usado en la producción de piezas para las cámaras de combustión de aviones de motor de reacción, en partes de naves espaciales, entre otras aplicaciones, sus orígenes se remontan a las culturas antiguas. Se puede decir que es una técnica que requiere una habilidad considerable para su ejecución.
Los pasos básicos para la obtención de una pieza por este método son (Figura 1): en primer lugar (Sánchez, C., 2003), la obtención de un modelo a partir del cual se genera un molde para inyección de ceras. Posteriormente se inyecta la cera en el molde a fin de obtener los patrones de la pieza; después de preparar la mezcla cerámica, que se compone de polvo refractario y un sistema de pegante coloidal, el patrón se introduce en la mezcla (baño húmedo) y después se hace aspersión de polvo cerámico (baño seco), para ser secado posteriormente. Esta operación se repite hasta que se tiene el espesor requerido de la cáscara o molde cerámico. Se pueden usar diferentes métodos para remover el patrón de cera; normalmente se utiliza autoclave. Las cáscaras son quemadas y llenadas con el metal fundido, el cual se solidifica dentro de la cáscara. Una vez se ha solidificado el metal, la cáscara cerámica se remueve a través de métodos químicos o mecánicos.
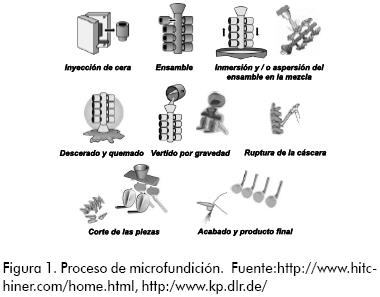
Para materiales no ferrosos y aceros inoxidables se hizo necesario hacer una revisión específica con el fin de establecer las limitaciones del proceso para su utilización. Algunos de los aspectos evaluados como la temperatura de vertido, las contracciones volumétricas y las tolerancias dimensionales relacionadas con los materiales mencionados, se ven en las Tablas 1 a 4.
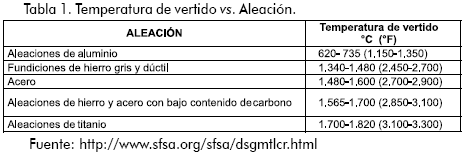
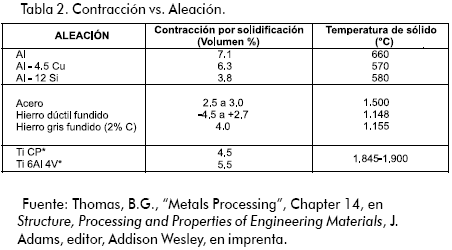
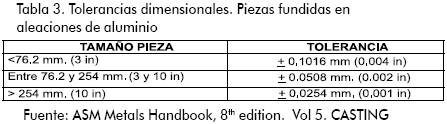
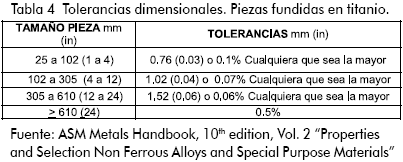
Adicionalmente, se pudo establecer que las limitaciones particulares para cada aleación en la utilización del proceso estaban relacionadas con: el material de recubrimiento (material cerámico), que incidía en la rugosidad superficial y el peso de la pieza a fundir.
Diseño para manufactura (DFM)
Se ha definido la ingeniería concurrente (IC) (Institute for Defense Analisis IDA, 1986) como un acercamiento sistemático al diseño integrado de productos y los procesos relacionados, incluyendo manufactura y soporte. Pretende que los diseñadores consideren todos los elementos del ciclo de vida del producto, desde el diseño conceptual hasta su disponibilidad en el mercado, incluyendo calidad, costos y los requisitos del usuario.
Una de las metodologías de diseño utilizadas en IC (Figura 2), particularmente las relacionadas con la productividad, es diseño para manufactura (Design for Manufacturing DFM), que se puede definir como una colección de programas, técnicas, métrica, herramientas y métodos para mejorar la fabricación de partes o simplificar el ensamble de productos, analizando valores, tolerancias, movimiento, complejidad y conveniencia para el ensamble manual, automático o flexible (robótico) para que encaje de manera óptima en un sistema de manufactura particular que resulta en costo y calidad excelente.
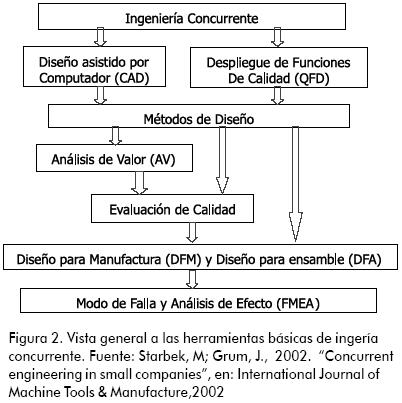
Mediante esta metodología se pretende que además del diseñador, personas del equipo de producción, e inclusive los proveedores, participen en el proceso de diseño, a fin de garantizar la manufacturabilidad. Sin embargo, no solo se utiliza, como se mencionó anteriormente, sino que es una herramienta de benchmarking que permite estudiar los productos de la competencia y cuantificar las dificultades de manufactura y ensamble.
El diseño para manufactura utiliza información de muchos tipos como: planos, especificaciones del producto y alternativas de diseño, un entendimiento detallado de los procesos de producción y ensamble, y una estimación de costos y volúmenes de producción, para lograr su objetivo último, que es obtener un artículo de alta calidad con el mayor aprovechamiento de los recursos. Por lo tanto, es necesaria la colaboración de miembros del equipo de desarrollo, así como de expertos externos a él (Ulrico, K., 1995).
Para la aplicación de DFM en general, es decir, sin especificaciones para un proceso, se pueden tener en cuenta los siguientes elementos: 1. Estimar el costo de manufactura, 2. Reducir el costo de componentes, 3. Reducir el costo de los ensambles, 4. Reducir el costo de producción, 5. Considerar el impacto de las decisiones de DFM sobre otros factores. La Figura 3 muestra la metodología general propuesta del diseño para manufactura.
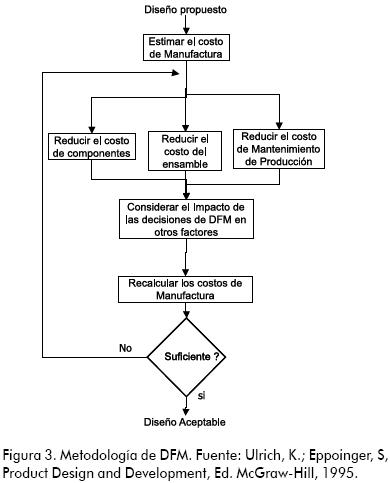
El objetivo de utilizar diseño para manufactura aplicado a un proceso en particular, es diseñar productos que sean fáciles de mantener, confiables, en menor tiempo y que sean más simples (Vernon, C., 2001), es decir, menos costosos para manufacturar, manteniendo la calidad de los mismos. Para alcanzar la meta, hay algunos principios que el equipo de diseño debe tener en mente (Tien-Chien, Wysk, y Hsu-Pin ,1998, pp 596-598).
Principios de DFM
- Reducir el número total de partes
- Desarrollar un diseño modular
- Usar materiales y componentes estandarizados
- Diseñar partes multifuncionales
- Diseñar para fácil fabricación
- Evitar partes separadas
- Minimizar las operaciones de manipulación
- Utilizar tolerancias amplias
- Minimizar el número de operaciones
- Evitar operaciones secundarias.
- Rediseñar componentes para eliminar pasos de proceso.
- Minimizar las operaciones que no añadan valor.
- Diseñar para el proceso.
Antes de llevar a cabo la selección del proceso, es necesario hacer algunas consideraciones en cuanto a los factores que afectan la selección del mismo, como: a. Factores de material, específicamente las propiedades mecánicas y físicas, b. Factores geométricos, entre los que se encuentran la forma, el tamaño y el peso de la pieza, y las tolerancias y acabados superficiales de la misma, c. Factores de producción, entre los que están el tiempo de mercadeo y la cantidad y la tasa de producción.
Diseño para microfundición (DFIC)
Una vez estudiados los principios del DFM, se dio inicio a la aplicación específica de DFM en el proceso de fundición a la cera perdida (Investment Casting). La microfundición es un proceso tecnológico de copiado de forma. Aunque es un método que permite la obtención de muchas morfologías que por otras técnicas serían de difícil fabricación, para ser utilizado de manera eficiente deben tenerse en cuenta las limitaciones que presenta.
Se estableció el estudio del DFIC como un estudio de reglas de diseño, estrategia que se puede emplear sin tener en cuenta una estimación muy aproximada de los costos. Las reglas de diseño para piezas elaboradas por una técnica de manufactura específica, parten del profundo conocimiento del proceso, de manera que se puedan fijar tanto la capacidad del mismo como las limitaciones que presenta en cuanto a dimensiones, material y geometrías.
Consideraciones de diseño
Antes de establecer estas condiciones es necesario haber evaluado a grandes rasgos si el proceso es adecuado para la producción de las piezas que se tienen en el proceso de diseño.
Según Bralla, el momento ideal para decidir si las piezas se van a hacer por medio de fundición en molde con revestimiento es cuando se están haciendo los bocetos preliminares (Bralla, 1993). Una vez conocidas las ventajas y limitaciones del proceso de microfundición, es posible establecer las variables que se deben tener en cuenta para realizar un diseño óptimo de productos. Existen muchos factores que afectan el diseño de piezas producidas por microfundición (Investment Casting); a continuación se describen los más relevantes.
Selección de material
La selección de un material adecuado afecta la fundibilidad de la pieza en términos de estabilidad dimensional e integridad interna. Aunque los materiales son por lo general seleccionados para satisfacer los requerimientos funcionales del producto partiendo de las propiedades específicas de cada aleación, en particular cuando se seleccionan materiales para fundición, estos se caracterizan por propiedades como la temperatura de vertido, la fluidez, la contracción volumétrica, entre otras, que permitan establecer una fabricación sencilla con alta calidad (Ravi, 2002).
Con el proceso de microfundición se pueden utilizar gran variedad de aleaciones ferrosas y no ferrosas. Estas pueden ser fundidas en hornos normales, de inducción o de gas. Casi cualquier material que puede ser vertido en condiciones normales, es decir no al vacío ni con atmósfera inerte, puede ser utilizado en este proceso (Simmons, 2000). Así mismo, es utilizado para conformar materiales con alto punto de fusión y materiales de difícil utilización en los procesos de mecanizado convencional.
Especificaciones técnicas
Las especificaciones técnicas están relacionadas con limitaciones de tamaño que tiene el proceso, particularmente en aspectos como: nervios, partes macizas, prevención de poros, conjugación de paredes, espesor de pared, corazones de cerámica, roscas de tornillos, radios, cuñas y cuñeros, agujeros, contracciones.
• Nervios
El parámetro dimensional principal del nervio es el espesor (s) del nervio en la cúspide. En la cúspide de los nervios deben hacerse obligatoriamente redondeos con un radio no menor de 1 mm. Las cúspides de los nervios de espesor inferior a 6 mm se redondean con radios de R = 0.5s. Para unir los nervios con las paredes es necesario hacer redondeos de R = 0.5S (Figura 4)

Los espesores de los nervios de acuerdo con su ubicación en la pieza se ven en la Tabla 5, y una indicación gráfica, en la Figura 5.
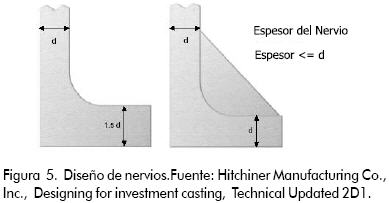
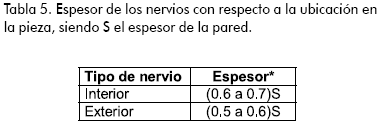
• Conjugación de paredes
Se aconseja hacer las paredes interiores aproximadamente igual a 0.8S, donde S es el espesor de las paredes exteriores (Orlov, Cap.3) (Figura 6). Es necesario que la conjugación de una pared a otras se haga con redondeos.
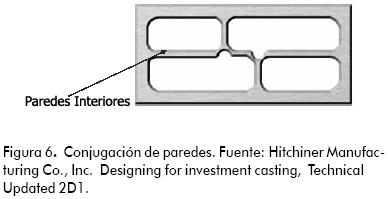
Se recomienda hacer la conjugación con radios trazados desde distintos centros. El radio exterior se hace desde 1 hasta 0.7 veces el radio interior.
Las paredes convergentes bajo ángulo obtuso se unen con los radios R = (50 a 100)s, donde s es el espesor de las paredes internas. Es conveniente en estos casos emplear paredes curvilíneas descritas con un radio de gran magnitud.
Juntas de pared:
La mejor manera de diseñar juntas de paredes es evitando ángulos agudos. La Figura 7 muestra varias maneras de unir paredes.
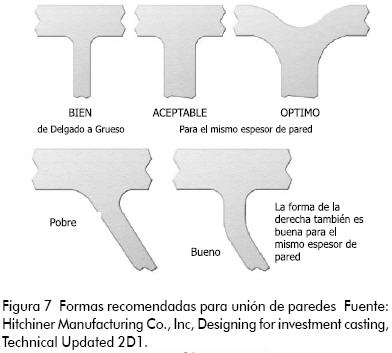
Las paredes de distinto espesor conviene unirlas con transiciones cuneiformes, con inclinaciones desde 1:5 a 1:10. Esta transición conviene reforzarla con nervios.
Una fundición bien diseñada tiene el mínimo número de secciones juntas evitando ángulos agudos, además de tener cada sección el espesor requerido específicamente para alcanzar la resistencia deseada y prevenir enfriamientos locales a baja velocidad. Una sección se enfría libremente en todas sus superficies, pero al añadirle una segunda sección se crea un punto caliente, y en esa área la tasa de enfriamiento se incrementa en un 50%, como en la Figura 8.
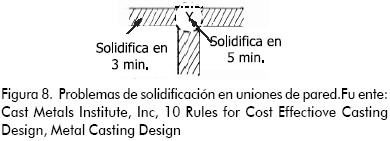
Algunas recomendaciones para evitar problemas de solidificación en la unión de dos o más paredes son:
- Evitar la concentración de metal escalonando las partes en cruz.
- Un agujero con macho puede agilizar la solidificación cuando se unen un número de secciones (Figura 9a).
- Se prefiere una red circular con secciones adjuntas (Figura 9b).
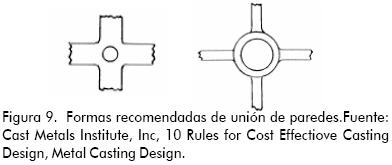
Cambios de sección:
Es recomendable evitar cambios abruptos de sección (Figura 10), y eliminar esquinas agudas (apuntadas) en secciones adjuntas.
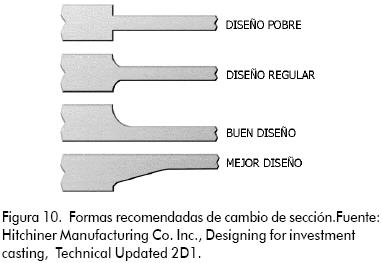
Se recomienda cuando hay cambios de sección, que la diferencia relativa en el espesor de las secciones adjuntas sea mínima y no exceda la relación de 2:1. Cuando un cambio de espesor es menor que 2:1, puede tomar la forma de un filete; cuando la diferencia es mayor, se recomienda hacer el cambio en forma de cuña.
Los cambios de sección en forma de cuña, no deben exceder 1:5 (Figura 11).
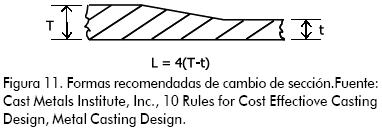
• Espesor de pared
Se recomienda diseñar todas las secciones tan uniformes en espesor de paredes como sea posible.Espesor mínimo de pared
El espesor mínimo de pared se determina particularmente por la fluidez del material que se va a vaciar y la distancia que el metal fundido debe viajar. En la Tabla 6 se muestra una relación entre los espesores mínimos de pared para diferentes materiales.
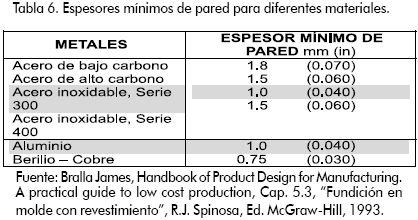
El espesor mínimo de sección para áreas limitadas y para áreas grandes está relacionado con el punto de fusión de las aleaciones, como se indica en la Tabla 7:
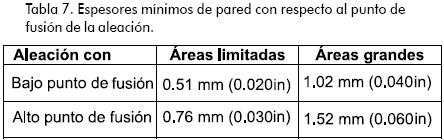
Espesor máximo de pared
El proceso está limitado para fundiciones con un espesor máximo de pared de 25.4 mm. (1 in) (Yankee, 1979).
• Radios
The Investment Casting Institute recomienda introducir radios y filetes internos para reducir contracciones y agrietamientos, ayudando a disipar calor, mejorando la solidificación y por lo tanto mejorando la resistencia y la integridad de la fundición. Es preferible siempre que se pueda en el proceso, dejar radios y filetes amplios, para facilitar la obtención de piezas más exactas y de mejor calidad.
El número de radios o filetes en un patrón debe ser el mínimo posible, preferiblemente solo uno. Por lo general, el radio de un filete, no debe exceder la mitad del espesor de la sección unida, desde el punto de vista del fundidor (Figura 12).
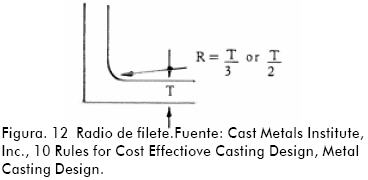
A pesar de que es posible producir esquinas agudas, es necesario de acuerdo con Bralla, especificar filetes con radios mínimos de 0.75 mm. (0.030 in). Yankee, por su parte, afirma que la tolerancia general para los radios es de 0.397 mm (1/64 in), mientras que los tamaños para radios de filetes que se prefieren según el mismo autor, son de 1.588 a 3.18 mm (1/16 a 1/8 in).
• Agujeros
La recomendación más importante al respecto es no ser práctico fundir piezas si los agujeros:
- Se hacen en materiales ferrosos y tienen menos de 1.5 mm. (0.060 in) de diámetro.
- Se hacen en materiales no ferrosos y tienen menos de 2.2 mm. (0.087 in) de diámetro.
En cuanto a la posición de los agujeros, la tolerancia recomendada de control de posición es ±0.127 mm por 25 mm desde cualquier punto de referencia único.
No se recomienda hacer agujeros ciegos, para evitar que en ellos queden bolsas de aire por hacer de manera errada el revestimiento. Si es necesario hacer el agujero, se requiere que su profundidad no sea mayor que su diámetro.
Agujeros pasantes
Para los agujeros pasantes se aplican las mismas tolerancias que para los ciegos. La relación entre el diámetro y la longitud de un agujero pasante (L/D) debe ser:
- En materiales no ferrosos, menor o igual a 5:1
- En materiales ferrosos, no menor o igual a 4:1
La Tabla 8 muestra una conexión entre el tipo de agujero y la relación-diámetro longitud de acuerdo con los tamaños del agujero:
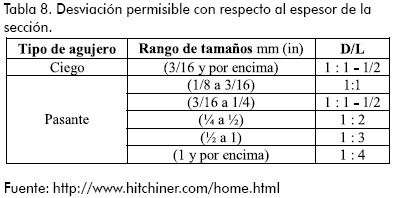
• Tolerancias dimensionales
Planitud y rectitud
La cantidad de tolerancias para lograr superficies planas y axialmente rectas varían con respecto a la longitud de la parte, el espesor y la conFiguración general de la pieza.
- Según Hitchiner, las tolerancias para rectitud axial son: ±.127 mm por cada 25 mm (±.005 in por in).
- La tolerancia de planitud es una zona de tolerancia definida por dos planos paralelos dentro de los cuales la superficie debe recaer. Por lo general es una función de la contracción volumétrica, tanto del patrón como del metal durante el enfriamiento. La Tabla 9 muestra las tolerancias recomendadas para planitud. Se toman como el LTI (lectura total del indicador) las tolerancias de deflexión de una barra inicialmente plana.
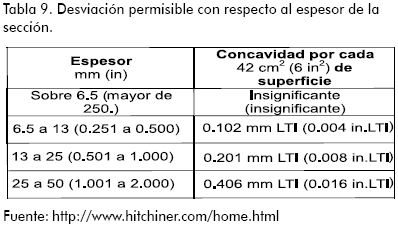
La Tabla 10 muestra las tolerancias recomendadas para rectitud.
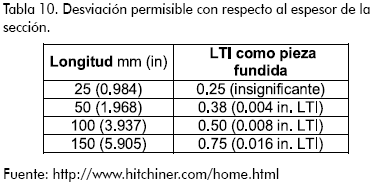
Tolerancias lineales de fundición
Para el proceso estudiado, estas tolerancias pueden ser + 0.125 mm. por cada 25 mm. (+ 0.005 in por cada in). La Tabla 11 muestra las tolerancias lineales que el proceso puede producir.
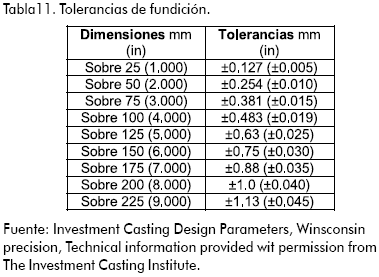
Secciones paralelas
Paralelismo es la condición en la que una superficie equidista en todos los puntos de un plano o eje dado a lo largo de su longitud. Esta condición es difícil de controlar en cualquier técnica de fundición. Es necesario controlar las relaciones entre longitud y espesor de los elementos. En general, puede utilizarse para los casos de combinaciones la tolerancia de 0.254 mm por cada 25 mm (0.010 in LTI por in). Las tolerancias de colada, que se obtienen en bruto, se pueden observar en la Tabla 12.
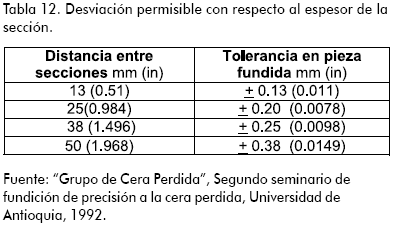
Angularidad
Es la condición de una superficie, eje o plano central que está a un ángulo específico (diferente a 90º) de un plano o eje dado.
Las tolerancias de los ángulos para fundiciones dependen de su ubicación en la pieza. Varían de ± 1/2° para lugares bien sostenidos a ± 2° en aquellos sitios donde se puede esperar una distorsión inherente. Según Bralla, las tolerancias dependen de la conFiguración de la pieza; tolerancias recomendadas para los ángulos que se muestran en la Figura 13 son:
a. Aberturas angulares como la a (± 1.5 º)
b. Formas angulares como la b (± 0.5º)
c. Paralelismo como en c (± 2.0º)
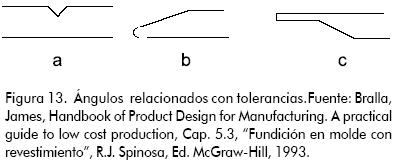
Superficies cóncavas y convexas
Las superficies convexas se pueden fundir con más exactitud que las cóncavas, ya que el metal, cuando se solidifica y contrae, se adhiere al molde en lugar de separarse. Para Yankee, una regla general para tolerancias de redondez puede ser 0.005 mm/mm (0.005 in/in).
Conicidad
Se necesita una pequeña conicidad para sacar los modelos de cera del molde. Según Bralla, los ángulos adecuados están entre ¼º y ½º.
Figuras de contornos redondos
Concentricidad:
Es una condición en la cual dos o más Figuras en cualquier combinación tienen un eje común. En los diámetros de un eje es una función de la rectitud.
1. Se consideran centros excéntricos dentro de una tolerancia de ±0.127 mm por 25 mm de separación máxima.
2. Los centros de diámetro interior y de diámetro exterior serán concéntricos dentro de los 0.076 mm por 13 mm de espesor de pared.
Redondez - Barras:
Es una función de las variaciones de la contracción del metal. La variación de la contracción se incrementa con el diámetro y la tolerancia que se requiere aumenta proporcionalmente. Se puede aplicar como regla general ±0,127 mm por 25 mm.
Redondez Tubería:
La tolerancia de redondez especifica la zona de tolerancia limitada por dos círculos concéntricos, entre los cuales cada elemento de superficie circular debe permanecer. En una tubería la tolerancia general para fundición es de ±0.127 mm por 25 mm. La Tabla 13 establece las tolerancias para redondez de tubería.
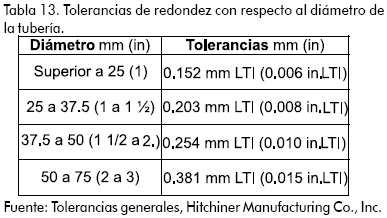
La sección tubular que se encuentra fuera de redondez, se puede alterar mecánicamente de acuerdo con el espesor de la pared y con la ductilidad.
Superficies para mecanizado
Dependiendo de la aleación, los rangos de acabado superficial están entre 2.2 y 3.8 µm (90 y 150 µin). Hitchiner Manufacturing indica que en la mayoría de los casos, por lo tanto, las únicas superficies que necesitan mecanizado son las que requieren buena apariencia visual, y aquellas que están relacionadas con contactos metal - metal. La Figura 14 muestra dos elementos: en el primero se encuentra un agujero no concéntrico y redondo, y en el segundo, un agujero concéntrico pero sin redondez.
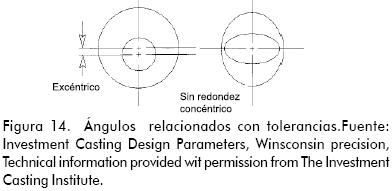
Acabados superficiales
Los valores de los acabados superficiales dependen de los materiales del patrón y del tipo de material a fundirse. Un acabado superficial mínimo de 30 µm. se obtiene usando patrones plásticos y técnicas de control de proceso especiales. La Tabla 14 muestra los acabados superficiales que se pueden producir dependiendo del metal de fundición.
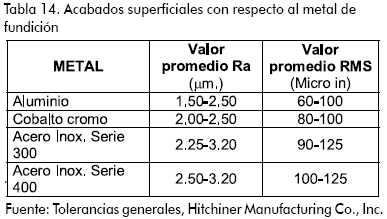
Partiendo de las reglas de diseño mencionadas anteriormente, se estableció una metodología de diseño para microfundición DFIC.
Metodología de diseño para microfundición
Si se quiere realizar un buen diseño para microfundición, es necesario establecer varios pasos que permitan llevar a cabo la estructuración del producto, teniendo en cuenta todos los aspectos importantes a contemplar, para lograr un diseño fácil de fabricar por este proceso, que a su vez sea más económico.
La Figura 15 muestra de manera general la metodología propuesta, partiendo del diseño conceptual e incluyendo la selección del proceso de fabricación y las consideraciones de diseño. Esta metodología es descrita globalmente a continuación.
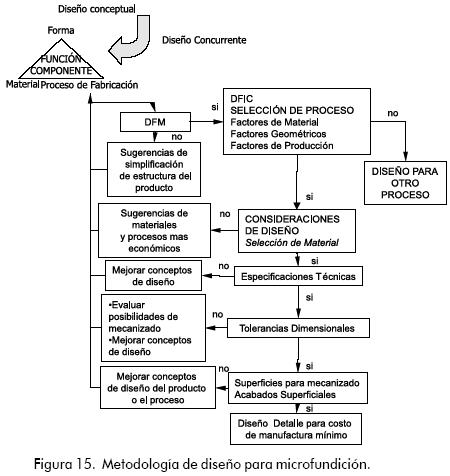
1. Habiendo seleccionado la opción de diseño conceptual que se va a trabajar, al realizar el diseño preliminar es necesario evaluar si el diseño que se tiene cumple con los requerimientos generales del DFM. Si no los cumple, es necesario establecer las simplificaciones de la estructura del producto.
2. Si cumple con los requerimientos generales de DFM, se debe evaluar si el diseño es adecuado con respecto al proceso en cuanto a la geometría, material y los aspectos relacionados con la producción. Si no es apropiado con respecto a estos conceptos, se debe seleccionar otro proceso.
3. Cuando se presenta sustitución de proceso, es indispensable establecer una comparación entre los propuestos, a fin de examinar cuál cumple con una mayor facilidad de fabricación y economía para la cantidad de piezas a manufacturar.
4. Si es apropiado el diseño para este proceso, se hace la selección de material o se establece si el seleccionado puede ser fácilmente trabajado por este proceso. Si no cumple, es necesario hacer sugerencias en cuanto a materiales más económicos y que cumplan con requisitos de diseño y manufacturabilidad.
5. Una vez seleccionado el material, se deben evaluar las especificaciones técnicas mencionadas anteriormente, con respecto a los límites que se tienen en cada uno de los aspectos propuestos. Si no las cumple, es necesario realizar mejoras en los conceptos de diseño.
6. Cuando se ha confirmado que se cumple con las especificaciones técnicas, se deben evaluar las tolerancias dimensionales que no se hayan contemplado en un principio.
7. Si el diseño se sale de las tolerancias que el proceso permite, es necesario examinar la posibilidad de realizar procesos complementarios para obtenerlas si el diseño las requiere. Sin embargo, conviene tener en cuenta las recomendaciones de DFM en cuanto a reducir el número de operaciones. Por lo tanto, es prudente evaluar si se pueden mejorar conceptos de diseño con respecto a las tolerancias.
8. Si cumple con las limitantes de las tolerancias para el proceso de IC, se evalúan los requerimientos de acabados superficiales. Si no es posible encontrar los acabados deseados, se debe examinar nuevamente la posibilidad de otros procesos para culminar la fabricación del elemento, o establecer mejoras en el diseño para evitar acabados superficiales superiores a los que se pueden obtener por el proceso.
9. Si se cumple con los límites de acabados superficiales, se procede a hacer el diseño de detalle y posteriormente el prototipo de producción.
Conclusiones
La selección del proceso de fabricación afectará no solo las propiedades y la calidad del producto sino también sus costos.
Se pudo observar que el proceso de fundición de precisión, a pesar de haber sido utilizado durante siglos de manera artesanal, tiene un manejo de variables que requiere de gran habilidad y exactitud para la obtención de productos de buena calidad con una utilización óptima de las materias primas y los insumos involucrados en él.
El proceso de microfundición presenta varias ventajas para la fabricación de productos como los biomecánicos, en los cuales es importante tener la posibilidad de fabricar piezas de formas intrincadas en materiales que pueden ser difícilmente conformados por otro proceso de fabricación.
Implementar el diseño para manufactura (DFM) hace posible, conociendo las características físicas del producto, las propiedades de los materiales en que se va a fabricar, las restricciones y capacidades del proceso, y los costos en que se incurre en su fabricación; establecer la viabilidad de su producción o si es necesario generar propuestas de mejoramiento en el diseño antes de llegar a la etapa de construcción, evitando incurrir en costos innecesarios.
Aunque DFM es una herramienta muy utilizada en la industria para generar diseños de bajo costo y alta calidad, su utilización debe hacerse con cuidado y los criterios seleccionados ser estudiados con cautela por los diseñadores, ya que no en todos los casos las decisiones van a impactar de manera positiva la calidad del artículo.
Para implementar DFM en un proceso específico en forma de reglas de diseño, es necesario partir del conocimiento profundo del proceso, de sus limitaciones y de la capacidad que tiene de producción.
Implementar DFM para un proceso específico en forma de reglas de diseño facilita la ubicación de puntos críticos en el diseño del artículo que se evalúa, de manera que permite una mejor utilización de los recursos y evita errores que pueden resultar en el incremento de los costos del producto.
En la aplicación de la metodología se puede observar que el cambio de material seleccionado no solo implica cambio en las características de la pieza debidas a las propiedades mecánicas requeridas, sino en las características del proceso de fabricación en cuanto a tolerancias factibles, contracciones dimensionales y acabados superficiales.
Las decisiones para la utilización de diseño para el IC y cualquier otro proceso requieren del empleo de metodologías propias de ingeniería concurrente; debe ser una tarea en la cual se involucren tanto los diseñadores como los ingenieros de producción de manera que se hagan cambios efectivos sin afectar las características funcionales de la pieza.
Bibliografía
AK steel, 316/316L Technical Data, 2000. [ Links ]
ASM, ASM Metals Handbook, 10th edition, Vol. 1, Properties and Selection Irons, Steels and High performance alloys. [ Links ]
ASM, ASM Metals Handbook, 10th edition, Vol. 2, Properties and Selection Non Ferrous Alloys. [ Links ]
ASM, ASM Metals Handbook, 8th edition, Vol. 5, Casting Article: Investment Casting. [ Links ]
Bernal, J., Martínez, F., Estudio de materiales para la construcción por microfundición de la turbina de un turbocargador., proyecto de grado presentado a la Universidad Nacional de Colombia para optar al título de ingeniero mecánico, 1996. [ Links ]
Boothroyd, G., Dewhrst, P., Knight, W., Product Design for Manufacture and Assembly., second , Marcel Dekker. [ Links ]
Bralla, J., Handbook of Product Design for Manufacturing, A practical guide to low cost production., McGraw-Hill, 1993. [ Links ]
Cast Metals Institute, Inc., 10 Rules For Cost Effective Casting Design, Metal Casting Design. [ Links ]
Chalmers, Bruce, Metalurgia física., Aguilar Ediciones, Madrid, 1968. [ Links ]
Colton, J.S., Manufacturing Processes and Engineering., Georgia Institute of Technology. [ Links ]
Crow, Kenneth., Design for Manuafacturing., DRM Associates, 2001. [ Links ]
Ebrahimi, S. A., Tortorelli, D. A. y Dantzig J. A., Sensitivity analysis and nonlinear programming applied to investment Casting design., University of Illinois at Urbana-Champaign. [ Links ]
Encyclopedic Handbook Of Biomaterials And Bioengineering, Part B, Applications., Vol. I, Marcel Dekker, Inc. 1995. [ Links ]
Etebari, A., Ferrante, J. y Wojcik, L., Advanced Lateral Mobility Prosthetic Ankle Design., Virginia Tech Spring Semester, 1998. [ Links ]
Gäumann, M. y Sholapurwalla, A., Investment Casting Simulation, Calcom SA (Lausanne, Switzerland, http://www.calcom.ch), UES Software Inc. (Annapolis MD USA, http://www.ues-software.com). [ Links ]
Gebelin, J. C., Jolly, M. R., Modelling of the investment casting process, Journal of Materials Processing Technology, 2003. [ Links ]
Hallab, N., Mikecz, K., Akrami, J., Jacobs, J., Titanium And Chromium Release Into and Binding With Human Serum From: Titanium and Cobaltchromium Implant Alloy Degradation., 46th Annual Meeting Orthopaedic Research Society, Orlando, Florida, March, 2000. [ Links ]
Hamilton, R.W., See D., Butler S., Lee, P.D., Multiscale modeling for the prediction of casting defects in investment cast aluminum alloys., Materials Sciense and Engineering, Secction A, 2003. [ Links ]
Hermanek, F., Spike, R., Finding the lost wax process., Vol. 32, No.1, 2002. [ Links ]
Hitchiner Manufacturing Co., Inc., Designing for investment casting., Technical Updated 2D1. [ Links ]
Hitchiner Manufacturing Co., Inc., An Introduction to the Investment Casting Process., Technical Updated. [ Links ]
Hover, A., Titanio para fijación de fracturas, O & T nuevos Avances en ortopedia y traumatología., Año 3, No. 6, abril, 1998. [ Links ]
Hsu, W., Liu, B., Conceptual design: issues and challenges., National University of Singapore, Computer-Aided Design, 2000. [ Links ]
http://www.ccbda.org/publications/pub13e/13e-Section5.html [ Links ]
http://www.dfma.com/ [ Links ]
http://www.efunda.com/processes/metal_processing/invest_casting.cfm [ Links ]
http://www.hitchiner.com/home.html [ Links ]
http://www3.me.iastate.edu/me324_bahadur/Section%202.2/2_1.htm [ Links ]
http://www.munroassoc.com/index.htm [ Links ]
http://www.northernprecision.com/facts.htm [ Links ]
http://www.npd-solutions.com/designguidelines.html [ Links ]
http://www.sfsa.org/sfsa/dsgmtlcr.html [ Links ]
http://www.sintef.no/content/page1____3869.aspx [ Links ]
http://www.tms.org/pubs/journals/JOM/jom.html [ Links ]
IDA (Institute for Defense Analysis), report R-338, 1986. [ Links ]
Jolly, M., Cox, M., Gebelin, J., Jones, S., y Cendrowicz A., Modelling the Investment Casting Process, Fundamentals of Investment Casting (FOCAST) IRC in Materials., University of Birmingham, UK American Foundry Society, 2001. [ Links ]
Jones, S., Yuan, C., Advances in shell moulding for investment casting., Journal of Materials Processing Technology, 2003. [ Links ]
Lackritz, H., Chernomorsky, A., Fariabi, S., Selvaduray G., Biomaterials in Medical Devices. [ Links ]
Long, M., Rack, H.J., Titanium alloys in total joint replacementa materials science perspective., Biomaterials Elsevier, 1998. [ Links ]
McCloskey, J.C., Productivity in Investment Casting., American Jewelry Manufacturing, Vol. 38, No. 6, June, 1990, p. 32. [ Links ]
Memorias Segundo seminario de fundición de precisión a la cera perdida, Grupo de Cera Perdida, Medellín, Universidad de Antioquia, noviembre, 1992. [ Links ]
Nanua, S., Systems approach to Computer integrated design and manufacturing., John Wiley & Sons, 1996. [ Links ]
O’Driscoll, M., Design for Manufacturing., Journal of Materials Processing Technology, 2002. [ Links ]
Ohkubo, C., Watanabe, I., Ford, J.P., Nakajima, H., Hosoi, T., Okabe, T., The machinability of cast titanium and Ti6Al4V., Biomaterials, 2000. [ Links ]
O'Mahoney, D., Browne, D.J., Use of experiment and an inverse method to study interface heat transfer during solidification in the investment casting process., Experimental Thermal and Fluid Science, 2000. [ Links ]
Orlov, Ingeniería del diseño., Cap. 3, Diseño de piezas de fundición, Ed. Mir. [ Links ]
Ouellette, J., Biomaterials Facilitate Medical Breakthroughs., American Institute of Physics, 2001. [ Links ]
Ozols, A., Aleaciones Implantables., Facultad de Ingeniería, UBA, En http://www.odontologia-online.com/casos/tecnologia/TN2/tn2.html [ Links ]
Pérez, A. J., Estudio de materiales bioimplantables y factibilidad de producción en el País., proyecto de grado presentado a la Universidad Nacional de Colombia, para optar al título de ingeniero mecánico, 1986. [ Links ]
Piehler, H. R., The Future of Medicine: Biomaterials., mrs bulletin, august, 2000. [ Links ]
Prasad, K.D.V., Yarlagadda, SiangHock, T., Statistical Análysis on Accuracy of Wax Patterns Used in Investment Casting Process., Journal of Material Processing and Technology, 2003. [ Links ]
Ravi, B., Casting Design and Analysis., Lecture Notes, II T, Bombai, 2002. [ Links ]
Reed, S., Investment Casting of Titanium Using the Induction Skull Melting Process., Flowserve Corporation, Jai Narayan Consarc Corporation. [ Links ]
Röhrig, K., Castings from stainless steels and nickel-base alloys., Consultant to the Nickel Development Institute. [ Links ]
Rosero, M.V., Estudio de los biomateriales para el desarrollo de endoprótesis., proyecto de grado presentado a la Universidad Nacional de Colombia, para optar al título de ingeniero mecánico, 2003. [ Links ]
Sánchez, J., Priest, J., Soto, R., An Intelligent Reasoning Assistant for Incorporating Manufacturability issues into the Design Process., Expert Systems with Applications, Vol. 12, No. 1, 1997. [ Links ]
Sánchez, C., Conceptos de diseño para manufactura DFM de piezas microfundidas para aplicación en dispositivos biomecánicos., proyecto de grado presentado a la Universidad Nacional de Colombia, para optar al título de ingeniera mecánica, 2003. [ Links ]
Shina, S. G., Faster New Product Development Through DFM and Concurrent Engineering., NEPCON’99. en Suntio, Teuvo Electronic Product Design, Power Electronics, University of Oulu 2001. [ Links ]
Simmons, J. M., Designing for investment casting, Machine design., 2000. [ Links ]
Starbek, M., Grum, J., Concurrent engineering in small companies., international Journal of Machine Tools & Manufacture, Vol 42, pp. 417-426, 2002. [ Links ]
Su X., Computer Aided Optimization of an Investment Bi-Metal Casting Process., University of Cincinnati, 2001. [ Links ]
The century in Ortopedics., en: Orthopedics Today, January, 2000. [ Links ]
The Legacy of Investment Casting, Hitchiner Manufacturing Co., Inc, April, 1998. [ Links ]
Thomas, B.G., Metals processing, Chapter 14: Structure, processing and properties of engineering Materials, Ed. Adison Wesley [ Links ]
Tien-Chien, C., Wysk, R.A. y Hsu-Pin, W., Computer-Aided Manufacturing, second edition, pp. 596-598, Prentice- Hall, 1998. [ Links ]
Tolerancias generales, Hitchiner Manufacturing Co., Inc. [ Links ]
Tu, J. S., Foran, R. K., Hines, A. M. y Aimone, P.R., An Integrated Procedure for Modeling Investment Castings., JOM (Minerals Metals and Materials Society publication). [ Links ]
Ulrich, K., Eppoinger, S., Product Design and Development., McGraw-Hill, 1995. [ Links ]
Bañadme, N. S., Que, L., Topoleski, L. D. T., Carbide surface coating of Co-Cr-Mo implant alloys by a microwave plasma-assisted reaction., en: Journal of Materials Science, 1999. [ Links ]
Vernon, C., Design for Manufacturing., OISM, 2001. [ Links ]
Winsconsin precision, Investment Casting Design Parameters, Technical information provided wit permission from The Investment Casting Institute. [ Links ]
Yankee, H., Manufacturing Processes., Ed. Prentice-Hall, 1979. [ Links ]
Yao, W.L., Leu, M.C., Analysis and design of internal web structure of laser stereolithography patterns for investment casting., Materials and Design, 2000. [ Links ]
Yoneda, T., Sato, T., Niyama, E., Apparent Solidification Shrinkage of Titanium Castings Induction-Melted in Lime Crucible., 1995. [ Links ]
Yu, J.C., Krizan, S., Ishii, K., Computer Aided Design for Manufacturing Process Selection., Ohio State University, en Journal of Intelligent Manufacturing, 1992. [ Links ]
Yu, Jyh-Cheng, Krizan, S., Ishii, K., Computer Aided Design for Manufacturing Process Selection., Ohio State University, en: Journal of Intelligent Manufacturing, 1992. [ Links ]