Services on Demand
Journal
Article
Indicators
-
Cited by SciELO
-
Access statistics
Related links
-
Cited by Google
-
Similars in SciELO
-
Similars in Google
Share
Ingeniería e Investigación
Print version ISSN 0120-5609
Ing. Investig. vol.33 no.2 Bogotá May/Aug. 2013
A. Salas1, S. Delvasto2 and R. Mejía de Gutiérrez3
1 Andrés Salas. Ingeniero Civil, Universidad del Valle, Colombia. Doctor en Ingeniería, énfasis en Ingeniería de Materiales, Universidad del Valle, Colombia. Posdoctorado en Ingeniería Civil, University of Illinois, USA. Affiliation: Departamento de Ingeniería Civil y Agricola, Universidad Nacional de Colombia, Colombia. E-mail: asalasm@unal.edu.co
2 Silvio Delvasto. Ingeniero Químico, Universidad del Valle, Colombia. Doctor en Nuevos Materiales y sus Tecnologías de Fabricación, Universidad Politécnica de Valencia, España. Affiliation: Profesor Titular, Universidad del Valle, Grupo de Investigación Materiales Compuestos (CENM). E-mail: silvio.delvasto@correounivalle.edu.co
3 Ruby Mejía de Gutiérrez. Química, MSc, Universidad del Valle, Colombia. Doctor en Ciencias Químicas, Universidad Complutense, España, Affiliation: Titular Professor, Universidad del Valle, Grupo de Investigación Materiales Compuestos (CENM). E-mail: ruby.mejia@correounivalle.edu.co
How to cite: Salas, A., Delvasto, S., Mejía de Gutiérrez, R., Developing high-performance concrete incorporating highly-reactive rice husk ash., Ingeniería e Investigación. Vol. 33, No. 2. August 2013, pp. 49 - 8.
ABSTRACT
The aim of this study is to present results of an investigation about the developing of a highperformance concrete (HPC) using a highly reactive pozzolan made from chemically treated rice husk ash (ChRHA) prepared by a chemical-thermal attack to the rice husk. This particular rice husk ash (RHA) consists of 99% of silica, highly amorphous, white in color and of greater pozzolanic activity than the silica fume and another rice husk ash prepared with only by a thermal treatment. The results of the physical, chemical and mineralogical characteristics of ChRHA are analyzed. In this study, the compressive strength, flexural strength, water absorption, resistance to carbonation, total charge-passed derived from rapid chloride permeability test (RCPT) and modulus of elasticity of hardened concrete were determined in the laboratory. Test results indicate that it is possible to produce HPC with the incorporation the chemically treated RHA. The incorporation of the chemically treated rice husk ash into the concrete enhances the compressive strengthand the durability properties being comparable to the properties of high performance concretes with silica fume (SF) made with the same replacement levels.
Keywords: pozzolanic materials, rice husk ash, sustainability, high performance concrete.
RESUMEN
El propósito del presente estudio es el de investigar la posibilidad de producir concretos de alto desempeño (HPC, por sus siglas en inglés) mediante el uso de un material puzolánico de alta reactividad elaborado a partir de ceniza de cascarilla de arroz tratada químicamente (ChRHA, por sus siglas en inglés) y preparada mediante un ataque térmico-químico a la cascarilla de arroz. Esta particular ceniza de cascarilla de arroz consiste de 99% sílice de alta amorfidad, blanca, con mayor actividad puzolánica que el humo de sílice y que la ceniza de cascarilla de arroz preparada únicamente con tratamiento térmico (TRHA, por sus siglas en inglés). Las características físicas, químicas y mineralógicas de las cenizas producidas fueron analizadas. En el presente estudio se evaluó la resistencia a la compresión, la resistencia a la flexión, la absorción de agua, la resistencia a la carbonatación, la carga total que pasa, derivada del ensayo rápido de permeabilidad a cloruros (RCPT, por sus siglas en inglés) y el módulo de elasticidad de los concretos endurecidos. Los resultados obtenidos de los ensayos indican que es posible producir concretos de alto desempeño con la incorporación de RHA tratada químicamente (ChRHA) en las mezclas de concretos, mejorando las propiedades mecánicas y de durabilidad, que son comparables a las propiedades de concretos de alto desempeño con humo de sílice (SF, por sus siglas en inglés) manufacturados con los mismos niveles de reemplazo.
Palabras clave: materiales puzolánicos, ceniza de cascarilla de arroz, sostenibilidad, concretos de alto desempeño.
Received: April 5th 2013 Accepted: June 5th 2013
Introduction
Much research has been carried during the last few decades into various aspects related to producing high performance concretes (Zain et al., 2000; Zhang et al., 1996; Isaia et al., 2003; Van Tuan et al., 2011; Malhotra et al., 2000; Aïtcin, 2003; Aïtcin, 1999; Aïtcin, 1998). Constituent materials, mix design methodologies, curing procedures and test methods have been extensively studied to enhance both concrete durability and strength for obtaining high performance concrete (Aitcin and Neville, 1993). it can be established that the mechanical and durability properties of high strength concrete are as good as or better than conventional concretes and that such improved properties can be reached by using low water/binder (w/b) ratios and supplementary cementing materials (Sakr, 2006). Portland cement clinker is the basis for most cementitious binders used in concrete, the manufacture of which is the most energy-intensive process after aluminium and steel (Zhang et al., 1996). Considerable efforts have been made around the world to use residues mainly produced by industry, agriculture and thermoelectric plants to produce concrete due to environmental concerns and the need to use less energy-intensive products. Using pozzolanic materials in cement or concrete mixes has played an important part in producing high-performance concrete over the past years, as their use brings benefits in technical, economic and environmental terms. Such benefits would include low hydration heat, high ultimate strength and low permeability (Zhang et al., 1996).
Improvements arising from the above-mentioned residual mineral additions are necessary for producing sustainable high performance concrete. Residues commonly used are silica fume (SF), metakaolin (MK) and fly ash (FA); however, depending on local availability, other types of residue could be used, such as RHA, a highly reactive pozzolanic material produced by the controlled burning of rice husks (Mehta, 1992; Bui, 2001; Chandrasekhar et al., 2003; Abu Bakar et al., 2011; Ramasamy, 2012). Even so, ash properties vary due to differences in incinerating conditions, heating rate, geographical location and fineness (Zerbino et al., 2011; Chao-Lung et al., 2011). Many studies have been completed in this field, but the use of this material is still limited in most countries due to its sensitivity to the aforementioned conditions (Sugita et al., 1997 (a); Sugita et al., 1997 (b)). In previous papers (Sugita, S. et al., 1997; Patel, M et al., 1987; Chandrasekhar, S. et al., 2005; Yalçin, N. et al., 2001; Salas A., et al., 2007) it was found that after removing various ions in the husk with an acid treatment, it is possible to produce amorphous silica of high purity and reactivity, characterized by high surface area and pore volume. Acid treatment has been found to decrease the degree of crystallization of silica and carbon in rice husks and also reducing the sensitivity of the pozzolanic activity of the rice husk ash to the manufacture conditions, specifically during the operation of combustion.
It has been shown (Salas, 2006; Salas et al., 2009) that incorporating chemically-treated rice husk ash (ChRHA) into concrete enhances its compressive strength compared to concretes containing silica fume (SF) at the same level of replacement. Regarding durability, it has been reported that ChRHA concrete resistance to chloride ion penetration was higher than that of control concrete and that of thermally-treated rice husk ash (TRHA) concrete and similar to SF concrete, showing that ChRHA is a very effective pozzolanic material (Salas et al., 2009). Such effectiveness has been attributed to the high content of amorphous silica and the very large surface area governed by the porous structure of the particles. Little research has been done into using ChRHA as a supplementary material in producing sustainable high performance concrete in Colombia, where SF, MK and high quality FA are limited and represent expensive materials for producing that type of concrete. ChRHA is an attractive sustainable alternative to this. Using ChRHA as a pozzolan for producing high performance concrete is a relatively new field of application. Potential benefits on the use of ChRHA in concrete could be to reduce the content of Portland cement, to develop high strength, to control the alkali silica reaction, to reduce chloride associated corrosion and sulfate attack and to increase the early age strength of the concrete. For this reason, the purpose of this investigation is to examine the effect of a partial replacement of Portland cement by a pozzolan - the chemically treated rice husk ash (ChRHA) - on the mechanical and durability properties of high performance concrete. The results are compared with those of concretes made with conventional RHA (TRHA) and silica fume (SF) at the same replacement levels.
Experimental programme
Materials
Two types of rice husk ashes were used in the present study: TRHA and ChRHA. The former was produced by thermal treatment and the latter by chemical and thermal treatment. These processes have been described in previous article (Salas et al., 2009). A commercially-available silica fume (SF) on the Colombian market was used as reference pozzolan in this study. Type V Portland cement conforming to Colombian standard codes NTC 30 and 31 was used for all the concrete mixtures. The chemical composition and physical characteristics of these materials are given in Table 1.
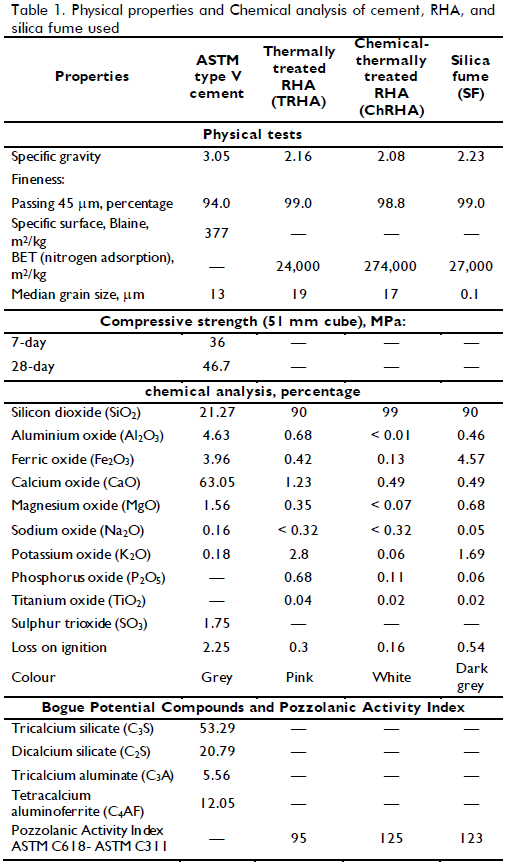
Particle size distribution of the materials was determined by a particle size analyzer using scattered light from laser beams projected through a stream of particles suspended in isopropanol. The average size of the rice husk ashes is larger than that of the cement particles and the SF grains. The ChRHA, however, has an extremely high specific surface of 274,000 m2/Kg evaluated by nitrogen absorption (BET), which is 11.5 times that for silica fume. According to Mehta (Mehta, P. K., 1978) the high specific surface of the ashes is due to its honeycomb microstructure. TRHA and ChRHA are highly amorphous materials (Salas A., et al., 2009) and the Pozzolanic Activity Index (ASTM C618 and C311) was 125 y 123% respectively. The scanning electron micrograph (Figure 1) shows that the morphology of TRHA and ChRHAparticles is angular.
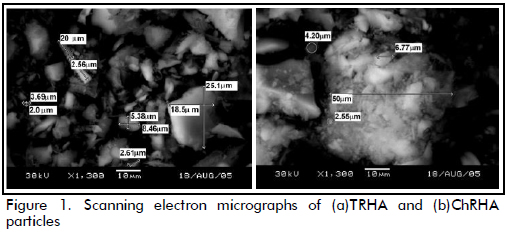
Crushed diabase was used as coarse aggregate, having 19 mm maximum nominal size; two graded river siliceous sands were used as fine aggregate, the first having 0 to 2.38 millimeters particle size and 1.78 fineness modulus whilst the latter had 0 to 9.51 millimeters particle size and 3.63 fineness modulus. Specific gravities were 2.75 for the coarse sand and 2.71 for the fine sand. Figure 2 shows the grading of the coarse and fine aggregates and the combined aggregate gradation used for the concretes.
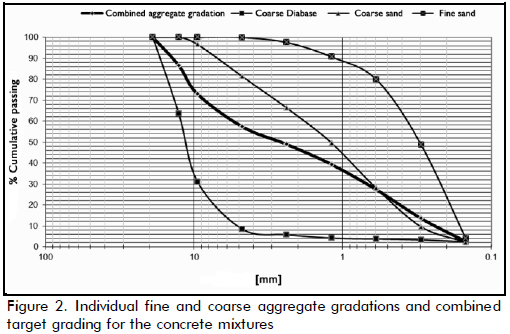
A naphthalene formaldehyde-based superplasticiser was used for most concrete mixes. The superplasticiser is a solution containing 42% solids.
Mixture proportions
The concretes were proportioned with 440 kg binder per m3 of fresh concrete and a 0.45 water/binder ratio. The aggregate proportions were: 37% coarse aggregate, 47% coarse sand and 16% fine sand. Superplasticizer dosage was 0.4% to 0.6% of binder mass. A total of 10 concrete mixtures were made, one being a control concrete (C0) and eight others having 5%, 10%, 15% and 20% TRHA or ChRHA as replacement to cement by weight. The last one contained 10% SF as reference material. Superplasticiser was added to ensure a slump between 125 to 175 mm.
Preparation and casting of test specimens
The concrete mixes were prepared using a tilting drum mixer. Mixing was in line with ASTM C192 (ASTM C192, 2007). The coarse aggregate was added to the mixing pan with about one-third of the mix water. The aggregate was then mixed for about 30 seconds for aggregate saturation. Mixing was then suspended and the cementitious materials and fine aggregate were added to the pan. The remainder of the water was slowly added while mixing. The final mixture was mixed for 3 minutes, rested for 3 minutes and then mixed for a final 2 minutes. When used, the superplasticizsers were added slowly during the first 3 minutes of mixing. 102 x 203 mm cylinders were cast from each mix for compressive strength and durability tests. The moulds were oiled, cast in three layers and compacted on a vibrating table. After casting, all specimens were left covered in the casting room at 20 ± 3 oC for 24 hours. The specimens were then demolded and transferred to a moist-curing room at 20 ± 3oC and 100 percent relative humidity until the time of testing.
Testing specimens
Fresh concrete properties were determined, including slump, air content, density and bleeding. The properties of hardened concrete mixtures included compressive strength at 28, 56, 90 and 180 days using five cylinders as follows: elastic modulus at 28 days on two cylinders, flexural strength at 28 days on three prisms and determining durability properties, such as absorption, chloride permeability, capillary suction and resistance to concrete carbonation at 56 days using cylinder portions. All the foregoing tests were carried out following the relevant ASTM standards.
Durability properties such as absorption according to ASTM C 642 (standard test method for density, absorption and voids in hardened concrete), chloride permeability according to ASTM C1202 (rapid determination of concrete chloride permeability), capillary suction and resistance to concrete carbonation (29oC, 3% CO2 content and %HR: 65-70%) were evaluated at 56 days of curing for the concretes using 10% of pozzolanic substitutes for Portland cement.
Tests results and Discussion
Fresh concrete properties
Fresh concrete properties are given in Table 2. The concretes had slumps ranging from 125 to 254 mm and unit weights from 2,294 to 2,397 kg/m3. Concrete air content ranged from 2.9% to 3.4%. Table 2 shows increased water demand as pozzolanic material use also increased. Higher amounts of superplasticiser were thus required for mixes T15, T20 and Ch15, Ch20, than those with SF; such mixes also had a high tendency to segregation and bleeding.
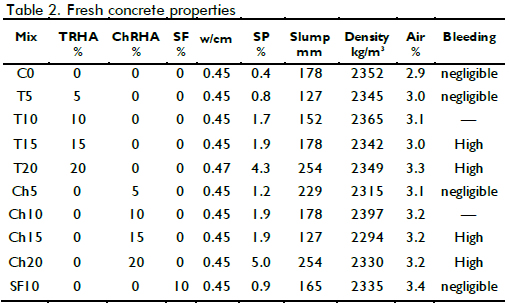
Mechanical properties
Compressive strength
Figure 3 shows the compressive strength development of the blended concretes specimens. The plotted bars represent the mean of five tests, all falling within 7% of the mean value. Comparing compressive strength data for 28, 56, 90 and 180 days curing times showed that compressive strength increased with TRHA and ChRHA by up to 10% and then concrete compressive strength decreased at 15% and 20%, this being lower than that of control concrete specimens. Concrete having 5% ChRHA had similar compressive strength to the 10%SF mix at all ages; mixes having 10% ChRHA had higher compressive strength than the 10%SF, values above 50 MPa, these being considered as coming within the range for high strength concrete (Kosmatka et al., 2011).
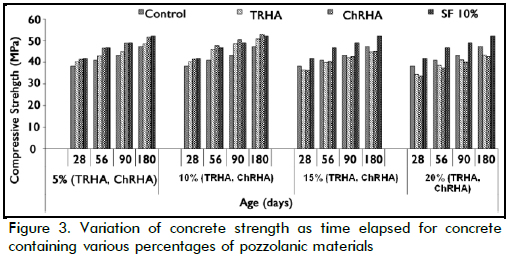
The reasons for high compressive strength development of ChRHA concrete and increased compressive strength up to 10% of cement replacement in concrete were attributed to silica content, ash fineness, amorphous phase, high specific surface area and pozzolanic reaction between calcium hydroxide and reactive silica in ChRHA in an alkaline environment, as reported in previous work (Zhang et al., 1996; Sakr, 2006; Bui, 2001; Zerbino et al., 2011; Salas et al., 2007).
Figure 3 shows that relatively high strength concrete (above 40 MPa) could be produced for all the mixes by adding up to 10% pozzolanic materials but strength decreased (compared to control mix) when lower TRHA percentages (15% and 20%) of ChTRHA were added. Due to the aforementioned reasons and because of the requirement for a higher dosage of superplasticiser for such concrete, concrete mixes having 10% of both ashes seemed to be the optimal limit for comparing strength and durability properties with those of control Portland cement and 10% silica fume concrete.
Elastic modulus
The elastic moduli measured at the age of 28 days with 10% added to concrete (as mentioned above) are shown in Figure 4. The test specimens for modulus of elasticity were loaded to a maximum 40% stress of maximum compressive strength according to ASTM C469 (ASTM C469, 2010). The load and deformation were recorded for each specimen and the value of the elastic modulus was calculated from recorded loads and deformations. Incorporating ChRHA mixes improved the concrete's elastic modulus compared to the SF concrete made with the same replacement level, and it was considerably higher than that of TRHA and control concretes. The effect of including ChRHA in the concrete on the elastic modulus of concrete revealed a similar trend to its effect on compressive and flexural strengths. The elastic moduli of concretes were higher when compressive strength also increased.
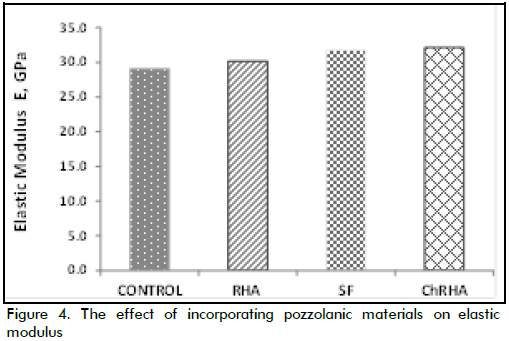
Flexural strength
The flexural strength of concrete under third-point loading was measured following ASTM C78 (standard test method for flexural strength of concrete, using simple beam with third-point loading). The tests were performed using a Forney universal testing machine (QC-0410 model) having 1,780 kilonewton capacity at 453 kilograms/minute loading rate. Three specimens from each mixture were cast. The dimensions of all beams were 150x80x700 mm (height x width x length), having a 600 mm span. A photograph of the test set-up is shown in Figure 5. The tests results for flexural strength (modulus of rupture, MOR) of the concretes are given in Figure 6. ChRHA produced higher mean flexural strength for each blended mixture, ChRHA produced higher mean flexural strength compared to the control and TRHA mixtures. The flexural strength of ChRHA and SF concretes showed that there was no discernible trend between those mixes.
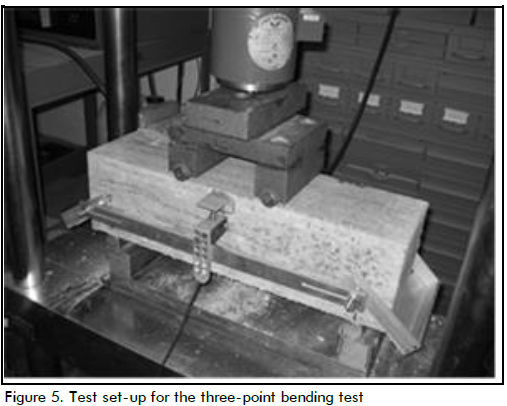
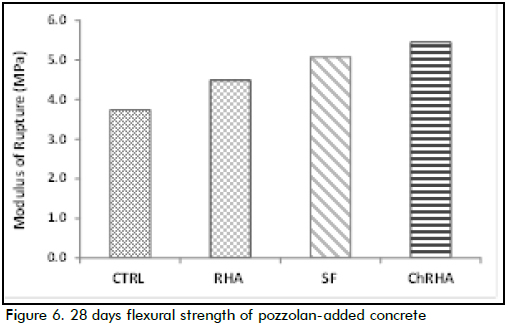
Durability aspects
The term high performance concrete is not just related to strength; durability is also one of the key attributes of HPC as a construction material; durability tests should thus be carried out to verify high performance. Concrete durability may be inferred by measuring the diffusion coefficient, the coefficient of permeability, the absorption rate, the concrete resistivity and the corrosion rate (Francy and Francois, 1998). Concrete permeability is a key factor influencing concrete durability. The ingress of various ions from the environment and their movement through building materials are responsible for structure deterioration. Controlling concrete permeability thus plays an important role in providing resistance to aggressive environments. In view of HPC durability, it is thus proposed that concrete must be designed to have a limited flow penetration rate to achieve a durable concrete, so as to minimise vulnerability to water and chemical ion attack during its service life.
Absorption
Water absorption was evaluated by ASTM C642 (standard test method for hardened concrete density, absorption and voids). The results are shown in Table 3. Absorption test results showed that concretes containing ChRHA and SF had lower permeability than the control and TRHA concretes, similar to the ranking of compressive strength for the four hardened mixes.
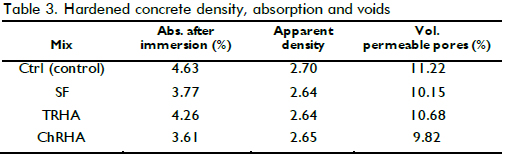
Capillary suction:
Water capillary sorption was measured following ASTM C 1585 (standard test method for measuring hydraulic-cement concrete water absorption rate).
Figure 7 compares sorption data for an exposure period of over 37 days for the oven dried samples. The sorption data shows the absorbed water versus (time)1/2. The mix having the highest porosity was the control mix; total water absorbed value was higher for the control mix, followed by TRHA and the lowest values were for SF and ChRHA concretes. It should be noted that the slope (sorptivity, S) of the curve was different, especially for the control mixture having the highest slope compared to ChTRHA concrete having the lowest slope; such difference in sorptivity would have reflected different capillary and gel pore sizes (Martys and Ferraris, 1997) in which higher size capillary pores dominated sorption at early times for the control mix. This meant that ChRHA substantially reduced blended mix absorption capacity, refining pore structure and densifying the material.
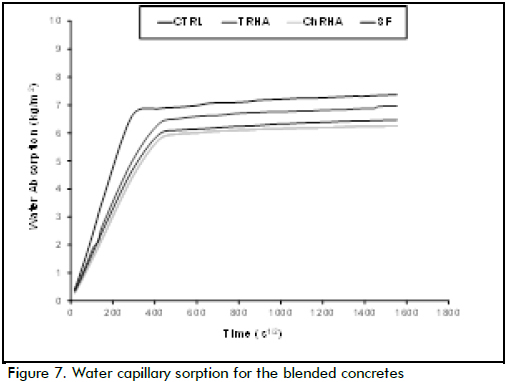
Chloride permeability
Resistance to chloride ion penetration was measured in line with ASTM C1202 (standard test method for electrical indication of concrete's ability to resist chloride penetration) as the charge in Coulombs (C) passed through the concrete by applying an external electrical field (60V) during a six-hour period. The test was carried out on 50 mm thick cylindrical specimens after 56 days curing. This test, called rapid chloride permeability test (RCPT), is essentially a measurement of electrical conductivity depending on both pore structure and pore solution chemistry.
The results are illustrated in Figure 8, including ASTM C1202 rapid chloride ion penetrability classification ranges. After 56 days, the control mix showed a moderate range of rapid chloride penetrability. Chloride ion penetrability had a low range (less than 2,000 C) in concrete made with TRHA, the 56-day rapid chloride ion penetrability was in a low range (less than 2000 C). The most efficient mixtures in this test were concretes incorporating either silica fume or ChRHA in a very low range (less than 1000 C).
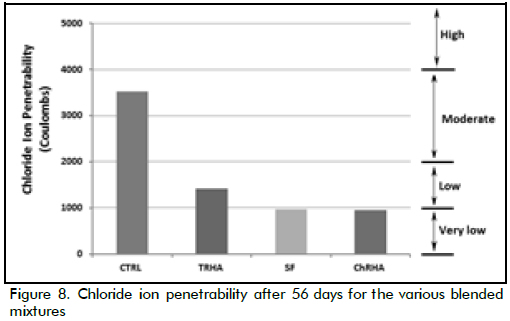
Concrete carbonation tests
The concrete specimens were subjected to accelerated carbonation; 75 mm diameter by 150 mm high samples were placed in a storage room at 29oC, 3% CO2 content and 65-70% HR. The specimens were divided into two halves after 75 days and carbonation depth was examined by spraying a fine mist of an aqueous 1% phenolphthalein solution in 70% ethyl alcohol used as pH indicator on the specimens' broken surface (Sanjuán et al., 2003). Table 4 and Figure 9 show that accelerated conditions produced similar average penetration carbonation depths after 75 days between concretes. These results were similar to those reported by Sanjuán et al., (Sanjuán et al., 2003) in concretes using fly ash and SF in severe exposure conditions and different water/cementitious ratios.
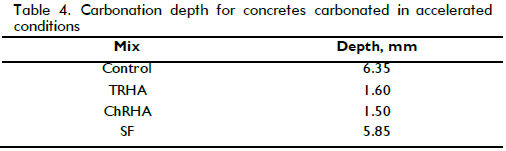
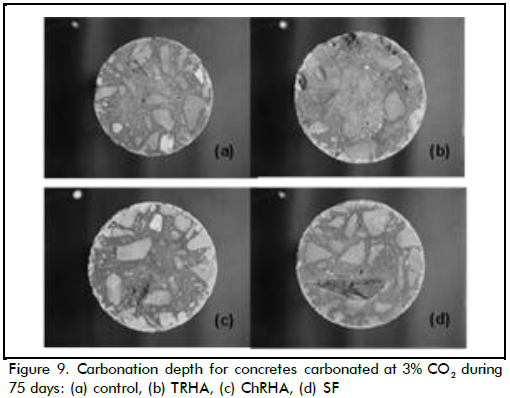
Conclusions
The following conclusions can be drawn from the results from the tests on concrete mixes where ordinary Portland cement (OPC) was replaced by pozzolanic materials:
- High performance concretes can be produced by using highly reactive rice husk ash (ChRHA) which showed enhanced properties when compared to ordinary Portland cement concrete, especially regarding compressive strength and durability;
- The general trends observed indicated that 10% ChRHA was an optimum OPC replacement level, enhancing compressive strength, the elastic modulus and flexural strength, showing higher values than concrete incorporating SF;
- Water requirement increased with ChRHA replacement ratio compared to a reference concrete using only OPC, having a detrimental effect on the mechanical properties of concrete mixes;
- Water absorption by immersion decreased drastically by incorporating 10% ChRHA, and chloride ion permeability also became significantly reduced, comparable to results obtained by incorporating SF;
- Carbonation resistance became reduced by adding ChRHA to the concrete; CO2 penetration depth increased 2.9-fold for concrete made with 10% SF and around 3.3-fold for concrete made solely with OPC; and
- Based on the aforementioned results, comparative tests between concrete specimens led concluding that high performance concrete can be prepared by using highly reactive rice husk ash (ChRHA), which was shown to have enhanced properties when compared to ordinary Portland cement concrete, especially regarding compressive strength and durability.
Acknowledgements
The authors wish to thank the University of Valle (Colombia), the Colombian Institute for Science and Technology "Francisco José de Caldas" (COLCIENCIAS), Arrocera La Esmeralda (rice-producing company), the Excellence Center for Novel Materials (CENM) and Doctor David Lange at the Airport Technology Centre for Excellence at the University of Illinois, Urbana-Champaign for supporting this study.
References
Abu Bakar, B. H., et al., Effect of rice husk ash fineness on the chemical and physical properties of concrete., Magazine of Concrete Research, Vol. 63, No. 5, 2011, pp. 313-320. [ Links ]
Aitcin, P., Neville, A., High-performance concrete demystified., Concrete International, Vol. 15, No. 1, 1993, pp. 21-26. [ Links ]
Aïtcin, P., High performance concrete., E & FN Spon, 1998, pp. 591. [ Links ]
Aïtcin, P., The art and science of high performance concrete., Materials Science of Concrete V, American Ceramic Society, 1999. [ Links ]
Aïtcin, P., The durability characteristics of high performance concrete: A review., Cement and Concrete Composites, Vol. 25, No. 4-5, May-July, 2003, pp. 409-420. [ Links ]
ASTM C192. Standard Practice for Making and Curing Concrete Test Specimens in the Laboratory., West Conshohocken, ASTM International, 2007, pp. 8. [ Links ]
ASTM C469 / C469M. Standard Test Method for Static Modulus of Elasticity and Poisson's Ratio of Concrete in Compression., West Conshohocken, ASTM International, 2010, pp. 5. [ Links ]
Bui, D., Rice husk ash as a mineral admixture for high performance concrete., Netherlands, Technische Univ. Delft, 2001, pp. 138. [ Links ]
Chandrasekhar, K., et al., Review processing, properties and applications of reactive silica from rice husk - an overview., J. Mater. Sci, Vol. 38, 2003, pp. 3159-3168. [ Links ]
Chandrasekhar, S., et al., Effect of organic acid treatment on the properties of rice husk silica., Journal of Materials Science, Vol. 40, 2005, pp. 6535-6544. [ Links ]
Francy, O., Francois, R., Measuring chloride diffusion coefficient from non-steady state diffusion tests., Cement and Concrete Research, Vol. 28, No. 7, 1998, pp. 947-953. [ Links ]
Chao-Lung, H., et al., Effect of rice husk ash on the strength and durability characteristics of concrete., Construction and Building Materials, Vol. 25, 2011, pp. 3768-3772. [ Links ]
Isaia, G., et al., Physical and pozzolanic action of mineral additions on the mechanical strength of high performance concrete., Cement and Concrete Composites, Vol. 25, 2003, pp. 69-76. [ Links ]
Kosmatka, S., et al., Design and control of concrete mixtures., 15th ed., Portland Cement Association, 2011, pp. 444. [ Links ]
Malhotra, V. M., et al., Long-Term Mechanical Properties and Durability Characteristics of High-Strength/High-Performance Concrete Incorporating Supplementary Cementing Materials under Outdoor Exposure Conditions., ACI Materials Journal, Vol. 97, No. 5, September-October, 2000, pp. 518-525. [ Links ]
Martys, N. S., Ferraris, C. F., Capillary Transport in Mortars and Concrete., Cement and Concrete Research, Vol. 27, No.5, 1997, pp. 747-760. [ Links ]
Mehta, P. K., Siliceous Ashes and Hydraulic Cements Prepared Therefrom, Belgium Patent 802909, July 1973, U.S. Patent
4105459, August 1978. Retrieved from: http://www.patentability.com/US4105459.html. [ Links ]
Mehta, P., Rice husk ash, a unique supplementary cementing material., Adv. Conc. Tech., CANMET, 1992, pp. 407-432. [ Links ]
Patel, M., et al., Effect of thermal and chemical treatments on carbon and silica contents in rice husk., Journal of Materials Science, Vol. 22, 1987, pp. 2457-2464. [ Links ]
Ramasamy, V., Compressive Strength and Durability Properties of Rice Husk Ash Concrete., KSCE Journal of Civil Engineering, Vol. 16, No. 1, 2012, pp. 93-102. [ Links ]
Sakr, K., Effects of Silica Fume and Rice Husk Ash on the Properties of Heavy Weight Concrete., Journal of Materials in Civil Engineering, May-June, 2006, pp. 367. [ Links ]
Salas, A., Efecto de la Ceniza de Cascarilla de Arroz Obtenida Mediante Tratamientos Térmico y Químico en Concretos de Altas Prestaciones., a PhD thesis presented at the Universidad del Valle, Colombia, 2006. [ Links ]
Salas, A., Ospina, M. A., Delvasto, S., Mejía de Gutierrez, R., Study on the pozzolanic properties of silica obtained from rice husk by chemical and thermal process., phys. stat. sol. (c), Vol. 4, No. 11, 2007, pp. 4311-4318. [ Links ]
Salas, A., Delvasto, S., Mejía de Gutierrez, R., Lange, D., Comparison of two processes for treating rice husk ash for use in high performance concrete., Cement and Concrete Research, Vol. 39, 2009, pp. 773-778. [ Links ]
Sanjuán, M., et al., Concrete carbonation tests in natural and accelerated conditions., Advances in Cement Research, Vol. 15, No. 4., Oct., 2003, pp. 171-180. [ Links ]
Sugita, S., et al., On the semi-industrial production of highly reactive rice husk ash and its effect on cement and concrete properties., International Congress on the Chemistry of Cement, Proceedings, Trondheim ICCC, 1997. [ Links ]
Sugita, S., et al., The resistance of rice husk ash concrete to carbonation, acid attack and chloride ion penetration., Adv. Conc. Tech., Proceedings of the International Conference, ACI, 1997, pp. 29-43. [ Links ]
Van Tuan, N., et al., Hydration and microstructure of ultra-high performance concrete incorporating rice husk ash., Cement and Concrete Research, Vol. 41, 2011, pp. 1104-1111. [ Links ]
Yalçin, N., et al., Studies on silica obtained from rice husk., Ceramic International, Vol. 27, 2001, pp. 219-224. [ Links ]
Zain, et al., Development of high performance concrete using silica fume at relatively high water-binder ratios., Cement and Concrete Research, Vol. 30, 2000, pp. 1501-1505. [ Links ]
Zerbino, R., Giaccio, G., Isaia, G. C., Concrete incorporating rice-husk ash without processing., Construction Building and Materials, Vol. 25, No. 1, 2011, pp. 371-378. [ Links ]
Zhang, M., et al., High performance concrete incorporating rice husk ash as a supplementary cementing material., ACI Materials Journal, Vol. 93, No. 6, Nov.-Dec., 1996. [ Links ]