Services on Demand
Journal
Article
Indicators
-
Cited by SciELO
-
Access statistics
Related links
-
Cited by Google
-
Similars in SciELO
-
Similars in Google
Share
CT&F - Ciencia, Tecnología y Futuro
Print version ISSN 0122-5383On-line version ISSN 2382-4581
C.T.F Cienc. Tecnol. Futuro vol.2 no.2 Bucaramanga Jan./Dec. 2001
*2Ecopetrol - Instituto Colombiano del Petróleo, A.A. 4185 Bucaramanga, Santander, Colombia
RESUMEN
Se ha analizado la fuerte contaminación ambiental producida por el ruido generado por el paso de los gases de combustión, a través de la válvula de control, en la planta de ruptura catalítica, Modelo IV de la Refinería de Barrancabermeja. Se aplican distintos modelos analíticos para determinar la dinámica del ruido y exponer una solución definitiva, técnicamente sustentada. El nivel de ruido puede ser reducido desde los 120 dB (A) actuales, hasta los aceptables 85 dB (A) de aplicarse los correctivos propuestos en este trabajo.
Palabras clave: gasodinámica, válvula de control, ruido.
ABSTRACT
It has been analized the hard enviroment contamination by noise generated by gases passing through control valve in fluid flow catalitic cracking plant Model IV in Barracabermeja refinery. It was applicated analitic models to fixed dynamic noise and propose some definitive solutions. Noise level could be minimized from actually 120 dB (A) to admissibly 85 dB(A) by corrective application proposed in this work.
Keywords: gasodinamica, control valve, noise.
INTRODUCCIÓN
En la planta de Ruptura Catalítica, Modelo IV de la Gerencia del Complejo de Barrancabermeja, se halla la zona más ruidosa del complejo industrial con niveles que alcanzan los 112 dB(A), localizados en diversas frecuencias del espectro audible. Concretamente el ruido se localiza en la zona del Enfriador de Gases Combustibles, EGC ó FGC (E-351) (Figura 1). La presión creciente sobre los procesos industriales para que minimicen el impacto ambiental ha obligado a promulgar y aplicar reglamentaciones industriales de protección -con el menor impacto posible sobre el medio ambiente- a fin de generar y establecer mejores condiciones de trabajo para el personal que labora en las plantas de proceso.
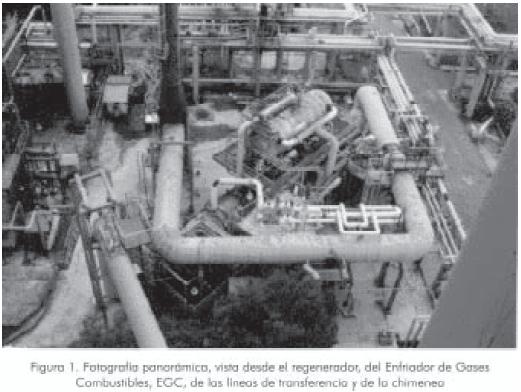
En los casi 120 metros de la línea de transferencia, desde el regenerador (R-301) hasta la chimenea, se encuentran: el intercambiador (E351), la válvula corredera de control (ZICV 301) y la placa de orificio (RO-350); el esquema de la planta puede observarse en la Figura 2. La función de la válvula corredera de control es la de mantener un diferencial de presión (13789 Pa, máx.) entre el reactor y el regenerador; o la de mantener la presión en el regenerador entre 103.500 Pa y 110.400 Pa. La válvula corredera está diseñada para generar grandes de caídas de presión (69.000 Pa) estando casi totalmente cerrada -como es el caso actual- pero a costa de generar elevados niveles de ruido, vibración y desgaste. De otra parte, la misión de las válvulas es otorgar, mediante su accionamiento, flexibilidad en la operación de la planta. Flexibilidad que se ha perdido en la URC modelo IV, debido a que la válvula de chimenea debe permanecer casi totalmente cerrada con el fin de propiciar la caída de presión establecida actualmente. Al EGC lo conforman dos intercambiadores: el E-350 que es un serpentín de vapor supercalentado y el E-351 que es la zona de enfriamiento de los gases combustibles.
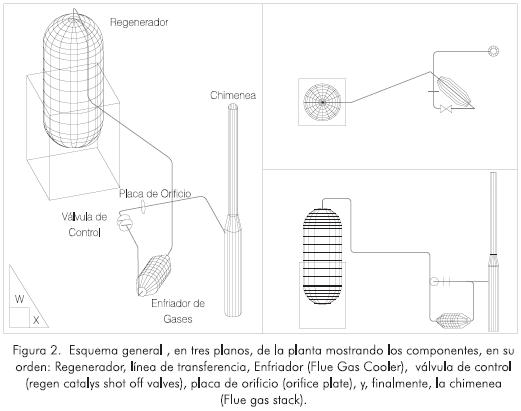
El resultado de este estudio explica el origen del alto nivel de ruido en el EGC de la planta Ruptura Catalítica Modelo IV y señala las estrategias técnicas más convenientes para reducir el nivel a límites aceptables. Para analizar el ruido este estudio se apoya en los fundamentos básicos de la dinámica de gases y en la aplicación de herramientas del modelamiento numérico.
Antecedentes
El ruido se inicia desde principios de los años 80 cuando se instala el EGC. En 1982 se instala la platina de orificios (RO-350) diseñada por la Exxon; que no obstante, no logra reducir los altos niveles de ruido. En 1988 se inician las mediciones sistemáticas del ruido y se identifican los altos niveles existentes, causados por el cierre de la válvula de control (cerrada en un 96% generando alta velocidad de fluido). Durante la parada de 1992 se propone tapar tres de los nueve huecos de la platina a fin de aumentar la caída de presión y poder abrir la válvula de control; sin embargo, no se obtienen buenos resultados. Un estudio realizado por Stopson Española S.A., en 1994, propone instalar un silenciador en la base de la chimenea, justificado por el fenómeno de resonancia que se presenta en este sector. Sin embargo, esta alternativa no se implemento debido al posible taponamiento en el silenciador, producto de la elevada cantidad de material particulado que se maneja durante la operación y los ulteriores trabajos de mantenimiento que tendrían que realizarse para corregir este problema. La última medición de los niveles de ruido en Agosto de 1999 indican valores similares a los medidos diez años atrás; lo que indica la persistencia del alto nivel.
Para efecto del los análisis realizados en el presente trabajo, se asume un flujo adiabático e isoentrópico (Streeter y Wylie, 1987) es decir, una vez el flujo ha salido del EGC no habrá intercambio de calor con el exterior. El flujo adiabático sin fricción (o isoentrópico) es una idealización que no puede ser alcanzada en el flujo de gases reales. No obstante, se considerará al gas combustible como un gas ideal ya que la mayor proporción es aire (o la combinación de nitrógeno y oxigeno). Por lo tanto, se mantendrá constante el calor específico; esto facilitará los cálculos que se emprenderán.
El objetivo principal de esta investigación es el de explicar el origen del alto nivel de ruido en el EGC de la ruptura catalítica modelo IV, con el fin de generar la alternativa más conveniente en la reducción del nivel de ruido. Específicamente, se desea realizar un estudio de dinámica de gases, en la línea de tubería partiendo de la salida del EGC hasta la chimenea de la respectiva unidad, con el fin de detectar condiciones criticas de flujo.
Características del fluido
El fluido manejado en la planta alcanza en condiciones normales 82.300 Kg por hora, y más del 80% en volumen está constituido por aire (éste es inyectado tomándolo de la atmosfera), el resto es C02 (13%), CO (3.5%), O2 (1%), SO2 (350 ppm), NOx (110 ppm). Con un peso molecular de 28.8 por mol.
El aire es inyectado en el regenerador para eliminar por combustión el coque que se deposita sobre el catalizador durante la ruptura catalítica, de tal manera que éste pueda ser reutilizado. El producto de esta combustión son los gases que irán al enfriador EGC para recuperar calor y luego serán expedidos a la atmósfera a través de la chimenea, pasando previamente por la válvula de control. Estos gases entran al enfriador a una temperatura de 750°C (1023 K) y salen a la atmósfera a 267°C (540 K). El calor recuperado será utilizado en el proceso de la planta. La caida de la presión a través de los ductos se observa en la Figura 3, allí se muestra el perfil de la presión en la línea de transferencia desde la entrada al enfriador hasta la salida en la chimenea, algunos valores han sido leídos en campo y otros han sido calculados. Las distancias entre 0 y 30,13 metros corresponden al EGC; la distancia entre 43,3 y 43,8 metros corresponden a la entrada y salida de la válvula ZICV-301; la distancia entre los 53,19 y 53,26 metros corresponden a la entrada y salida de la placa de orificios RO-350.
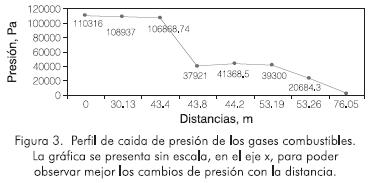
Caracterización del ruido en válvulas de control
La gran mayoría de los problemas de ruido en válvulas de control es aerodinámico. Se produce como consecuencia del flujo de gas. El mecanismo generador del ruido aerodinámico (Tabla 1), resulta del aumento de las velocidades de flujo en el proceso de estrangulamiento a través de la válvula.
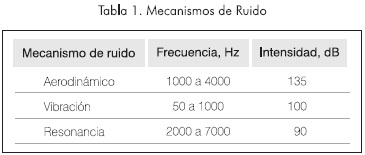
El proceso de estrangulamiento en válvulas de control y placas de orificio origina ondas de choque y/o turbulencia en los límites del fluido. Así mismo, un chorro expandido, aguas abajo de la válvula, produce esfuerzos de corte intensos que también producen ruido y turbulencia. Este mecanismo puede generar niveles de ruido de hasta 135 dB absolutos en frecuencias que van de los 1.000 a los 4.000 Hz.
Debido a que la amortiguación es muy baja en tuberías que transportan gas o vapor hay una buena posibilidad de que se presente radiación sonora aguas abajo del orificio de la válvula. Otra fuente de ruido es la vibración mecánica de los componentes de la válvula, originada por el choque del fluido contra partes móviles, esto produce ruido en el espectro de frecuencias de los 50 Hz a los 1000 Hz. El ruido en las frecuencias más altas se origina por fenómenos de resonancia en tuberías y accesorios; este ruido, de una intensidad de 90 dBa, se encuentra entre los 2000 y los 7000 Hz.
MEDICIONES EN PLANTA
La Figura 4 y la Tabla 2 muestran los datos medidos en campo en Agosto de 1999 para los niveles de ruido. Se toman datos en varias escalas, según las posibilidades del equipo de medida. No obstante, la escala crítica a tener en cuenta son los valores en dB(A).
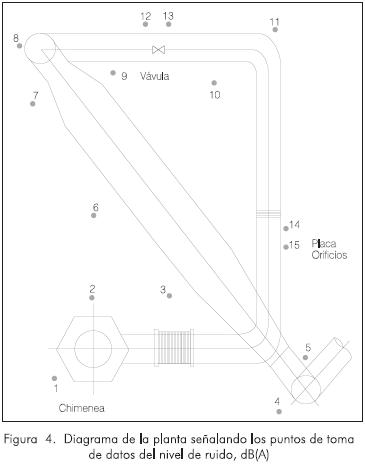
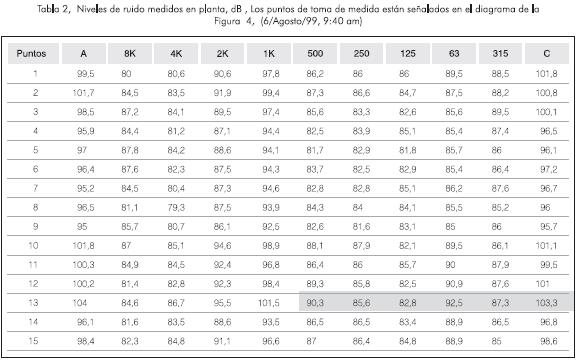
De la Tabla 2, puede razonarse que la totalidad de los puntos en la escala A (primera columna) están por arriba de los niveles permisibles de 85 dB(A), observándose que en los puntos 10, 11, 12 y 13 se hallan los valores más altos, que coinciden con la posición de la válvula. Esto demuestra, una vez más, que el problema del alto ruido está siendo generado en la válvula de control. Los otros rangos de medición mostrados en la Tabla 2, determinan la caracterización del ruido es decir, muestran si el origen del ruido es aerodinámico, es por vibración o es generado por resonancia. Para el caso particular de la válvula analizada, y según los resultados mostrados en al misma tabla se determina que el ruido es esencialmente aerodinámico.
CARACTERIZACIÓN DEL COMPORTAMIENTO DE LA APERTURA DE LA VÁLVULA DE CONTROL
Se realizó una simulación de la válvula corredera de control (Tuma, 1998), para determinar el intervalo de apertura de la misma en el cual se tiene mayor control sobre el área de paso. Intervalo donde teóricamente debería quedar ajustada la válvula para responder más adecuadamente a las exigencias de control. Se llegó a la conclusión de que en esta válvula se tiene la misma posibilidad de controlar el área de paso durante todo el recorrido de apertura. En la Figura 5 se muestra una de las posiciones de paso de las compuertas de apertura/cierre de la válvula; la geometría que se va generando al paso de las compuertas es la sumatoria de tres áreas (A1, A2, yA3).
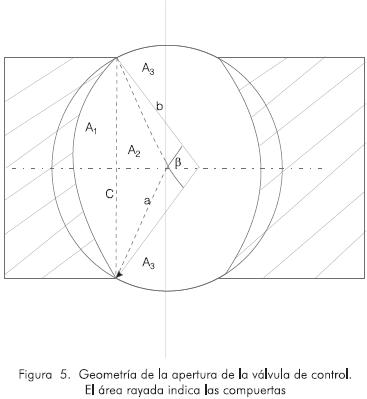
Las dimensiones establecidas páralos cálculos son:
- a: Radio interior de la válvula = 362 mm
- b: Radio de la compuerta = 444.5 mm
El área central o de paso del fluido en cualquier punto de desplazamiento de la compuerta está dada por la suma de tres geometrías: un sector de curva con radio a y ángulo θ (A3), un segmento de curva con radio b y ángulo β(A1), dos triángulos (A2).
Área de un segmento de curva, A1.
Área de un sector de curva, A3:
Área del triángulo, A2:
Los límites están dados así:
c varía entre cero y el doble del radio interior de la válvula, 2a
b varía entre cero grados y 69.7°
q varía entre 90° y 0°
La suma de las tres áreas dará el modelo del comportamiento de la vávula cuya curva está mostrada en la Figura 6. Como se observa el área de control de flujo varía linealmente con el desplazamiento de las compuertas (en la Figura, el cero de desplazamiento corresponde con las compuertas completamente desplazadas, válvula totalmente abierta dando un área máxima, y el recorrido de cada compuerta será de 28 cm: para dar el área mínima de paso del fluido). Con esto se espera la misma característica de respuesta durante todo el intervalo de operación; siendo el área proporcional al desplazamiento de la compuerta. El área de cierre total de las compuertas equivale al 86.6% respecto al área con las compuertas completamente abiertas. El área de máximo paso de fluido es de 4.116,8 cm2 y el área de máxima restricción del fluido es de 551,7 cm2. Para efectos de cálculo aerodinámico o de dinámica de gases, se tomará un diámetro equivalente.
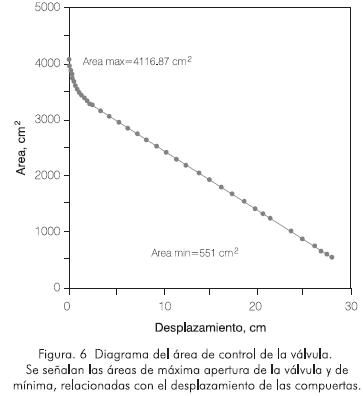
CARACTERIZACIÓN DEL FLUJO EN LA LÍNEA DE TUBERÍA. CÁLCULOS ANALÍTICOS
El estudio práctico de la dinámica de gases, comienza por determinar si el comportamiento del gas, para el caso particular, se puede modelar como flujo incompresible, mediante la aplicación de la siguiente ecuación:
Si se cumple la anterior condición el modelo se puede aproximar al flujo incompresible, de lo contrario será de flujo compresible. Para el caso de la planta Modelo IV, los resultados del cálculo indican un flujo compresible. En la Tabla 3 se incluyen todas las ecuaciones analíticas empleadas para estos cálculos. Las ecuaciones de la Tabla 3 han sido extractadas de ISA S75.17 (1989); ISA S75.01 (1985); ISA Handbook (1976); y de Greene (1989). Una velocidad de flujo de Mach 1 casi garantiza la generación de ruido. Sin embargo, cuando se manejan grandes volúmenes de flujo se puede producir ruido con velocidades de Mach 0,4 en presencia de caídas de presión relativamente pequeñas, cuando se manejan grandes volúmenes de flujo. La velocidad en cada tramo de la línea debe ser inferior a 0,3 Mach, que es la máxima velocidad permitida por los códigos de tuberías para evitar o minimizar el ruido. Para el caso de la Modelo IV se obtiene un número de Mach cercano a la unidad, flujo subsónico. El nivel del ruido calculado, 103 dB(A) coincide con los valores leídos en campo, 104 dB(A), indicando que los modelos elegidos para el cálculo son correctos y por lo tanto pueden ser utilizados para calcular las reformas que se propongan.
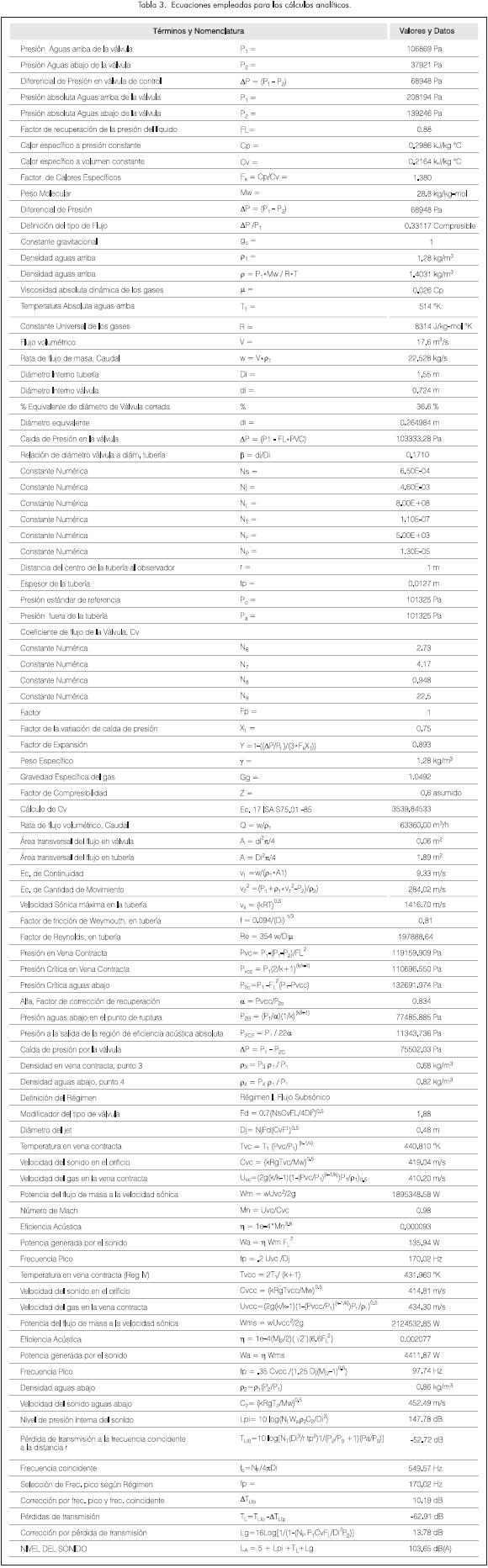
Análisis de los resultados
Todos los análisis realizados indican, sin lugar a dudas, que el problema está centrado en la válvula corredera. La onda de choque generada al pasar el fluido de régimen sónico a subsónico o a supersónico -causa directa del fuerte cambio en la presión- alimenta el ruido observado en la planta. La platina de orificio instalada aguas abajo no puede disminuir el ruido, toda vez que la información de ésta no llega a la válvula, justamente por que la onda de choque lo impide. Por lo tanto, se trata de aumentar la presión a la salida de la válvula de control, permitiendo abrir proporcionalmente las compuertas sin que esto afecte la presión en el regenerador. Otros elementos aguas abajo, deberán reducir gradualmente la presión hasta alcanzar la atmosférica.
De acuerdo con los resultados analíticos y de modelamiento numérico se propone instalar tres placas de orificios aguas abajo de la válvula de control. Distanciadas entre sí cinco metros, que reduzcan la caída de presión cada una un 50%, en los últimos 25 metros de la tubería. Esto permitirá abrir la válvula de control, reduciendo los niveles de ruido. Cada placa deberá tener una caída de presión de 27.580 Pa; esto implica que la válvula corredera se podrá abrir entre un 90% y 95%, reduciendo el nivel de ruido a 90 dB(A). Las dos nuevas placas pueden situarse a lado y lado de la actual (RO-350) a cinco metros de ésta; procurando que los orificios queden descentrados respecto de una a la otra; de tal manera que obligue al flujo a cambiar de dirección, reduciéndole la energía y por ende la velocidad. Adicionalmente se pueden instalar aislamientos en la tubería (Suárez, 1999) los cuales deben ser resistentes a la abrasión del fluido particulado y a la temperatura. En la Figura 7 se muestran los niveles de reducción del ruido según el espesor aplicado y tipo de aislante. De acuerdo con ciertos fabricantes de aislamientos acústicos, diseñadores de barreras, etc., se recomiendan tres métodos factibles para reducir los niveles de ruido, estos son: (i) Disminución del nivel de ruido en la fuente. Es decir cambios en la velocidad, en la presión u otra fuente. (ii) Interponer barreras que coloquen sombra acústica al receptor como cabinas, muros, silenciadores, etc. Este método puede tener entre 30% y 50% de absorción del ruido. Los materiales recomendados como barreras deben tener un peso específico entre 10 y 20 kg/m2. (iii) Aumentar la distancia entre la fuente del receptor con el fin de ganar en atenuación del ruido por el aire. En forma aproximada se reduce en 6 dB(A) el sonido por cada vez que se duplica la distancia entre ellos. Además es conveniente ubicar suelos absorbentes (árboles, pasto, etc.), entre la fuente y el receptor, los cuales evitan el refuerzo de las ondas por rebote contra piso duros.
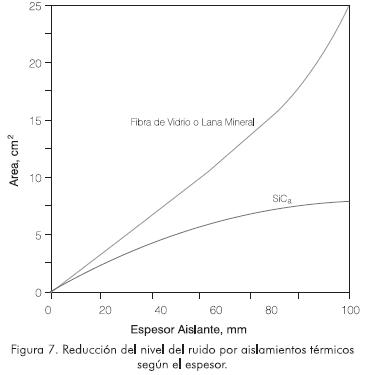
CONCLUSIONES
-
El ruido que se genera en el EGC de la unidad RC Modelo IV es de origen aerodinámico y esencialmente se debe a tres factores:
-
La válvula corredera (ZICV-301) opera muy cerrada (96%) generando potencias sonoras del orden de los 128 vatios, velocidades de flujo en la vena contracta que alcanza los 388 m/s y niveles de ruido mayores a los 100 dB(A). La velocidad del sonido aguas abajo es de 449 m/s, junto con el elevado material particulado generan grandes índices de erosión y vibración en la válvula.
-
La placa de orificios (RO-350) produce una caída de presión de 11721 Pa, 1.7 psig (había sido diseñada para 35.852,7 Pa; 5.2 psig), velocidades de 238 m/s y niveles de ruido de 97 dB(A). La información de la actual platina de orificios, no llega a la válvula debido a la onda de choque que se produce por el cambio de régimen en el fluido.
-
Los sistemas de conducción de gases presentan altos niveles de radiación sonora en todas las direcciones, pero preferencialmente aguas abajo de las válvulas. La suma del ruido generado por las válvulas y el producido por la placa alcanza los 102 dB. Adicionalmente la configuración geométrica de la tubería contribuye a elevar el nivel de ruido en uno o dos decibeles.
-
La reducción del ruido a niveles aceptables puede ser realizable por la instalación de tres placas de orificio aguas abajo de la válvula de control.
AGRADECIMIENTOS
Los autores agradecen de una manera muy especial al Dr. V. Demirel, por sus aportes y observaciones en este trabajo.
REFERENCIAS
Greene, R., 1987. "Válvulas: selección, uso y mantenimiento". México, McGraw-Hill. [ Links ]
Handbook of noise control, 1979. 2nd edition. [ Links ]
ISA Handbook of control valves, 1976. 2nd Edition. [ Links ]
ISA S75.17-1989. "Control Valve Aerodynamic noise prediction". [ Links ]
ISA S75.01-1985. "Flow equations for sizing control valves". [ Links ]
Streeter, V.L., Wylie, E. B., 1987. "Mecánica de los fluido". 8 Edición, México, McGraw-Hill. [ Links ]
Suárez, J, 1999 "Ingeniería de Control de Ruido". Primer congreso nacional de ingeniería mecánica, Universidad Nacional, Bogotá, Nov. [ Links ]
Tuma, J, 1998. "Engineering Mathematics Handbook". [ Links ]